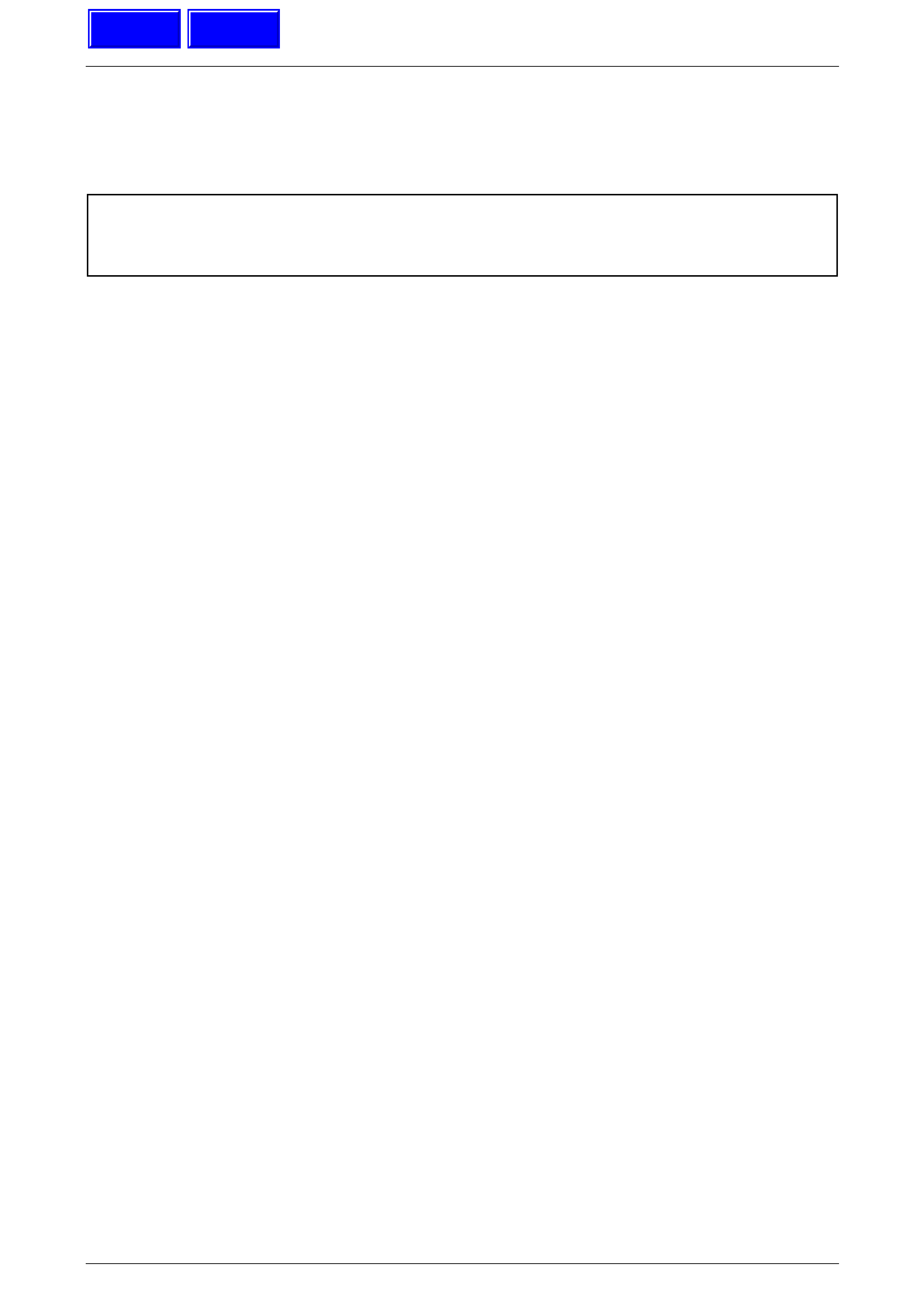
Exhaust System Page 8B–1
Page 8B–1
Section 8B
Exhaust System
ATTENTION
Before performing any service operation or other procedure described in this Section, refer to Section 00
Warnings, Cautions and Notes for correct workshop practices with regard to safety and/or property damage.
1 General Information ...............................................................................................................................3
1.1 Emission Reductions ............................................................................................................................................ 3
1.2 Catalytic Converter................................................................................................................................................ 4
Service Notes......................................................................................................................................................... 5
ADR 79/00 (Euro II) Emissions Standards ........................................................................................................... 5
1.3 Exhaust System Configurations........................................................................................................................... 6
Alloytec 190 Engine............................................................................................................................................... 6
GEN III V8 Engine................................................................................................................................................... 7
2 Service Operations – Alloytec 190 .......................................................................................................9
2.1 Service Notes......................................................................................................................................................... 9
Catalytic Converter................................................................................................................................................ 9
Oxygen Sensors..................................................................................................................................................... 9
2.2 Exhaust System................................................................................................................................................... 10
2.3 Complete Exhaust System Assembly................................................................................................................ 11
Remove................................................................................................................................................................. 11
Reinstall................................................................................................................................................................ 12
2.4 Rear Exhaust Assembly...................................................................................................................................... 13
Remove................................................................................................................................................................. 13
Reinstall................................................................................................................................................................ 13
2.5 Intermediate Exhaust Assembly......................................................................................................................... 14
Remove................................................................................................................................................................. 14
Reinstall................................................................................................................................................................ 14
2.6 Front Exhaust Assembly..................................................................................................................................... 15
Remove................................................................................................................................................................. 15
Reinstall................................................................................................................................................................ 16
2.7 Tightening Sequence........................................................................................................................................... 17
3 Service Operations – GEN III V8 .........................................................................................................19
3.1 Service Notes....................................................................................................................................................... 19
Catalytic Converter.............................................................................................................................................. 19
Oxygen Sensors................................................................................................................................................... 19
3.2 Exhaust System................................................................................................................................................... 20
3.3 Complete Exhaust System Assembly................................................................................................................ 21
Remove................................................................................................................................................................. 21
Reinstall................................................................................................................................................................ 22
3.4 Rear Exhaust Assembly...................................................................................................................................... 24
Remove................................................................................................................................................................. 24
Reinstall................................................................................................................................................................ 25
3.5 Intermediate Exhaust Assembly......................................................................................................................... 26
Remove................................................................................................................................................................. 26
Reinstall................................................................................................................................................................ 26
3.6 Front Exhaust Assembly..................................................................................................................................... 27
Remove................................................................................................................................................................. 27
Reinstall................................................................................................................................................................ 28
3.7 Tightening Sequence........................................................................................................................................... 30