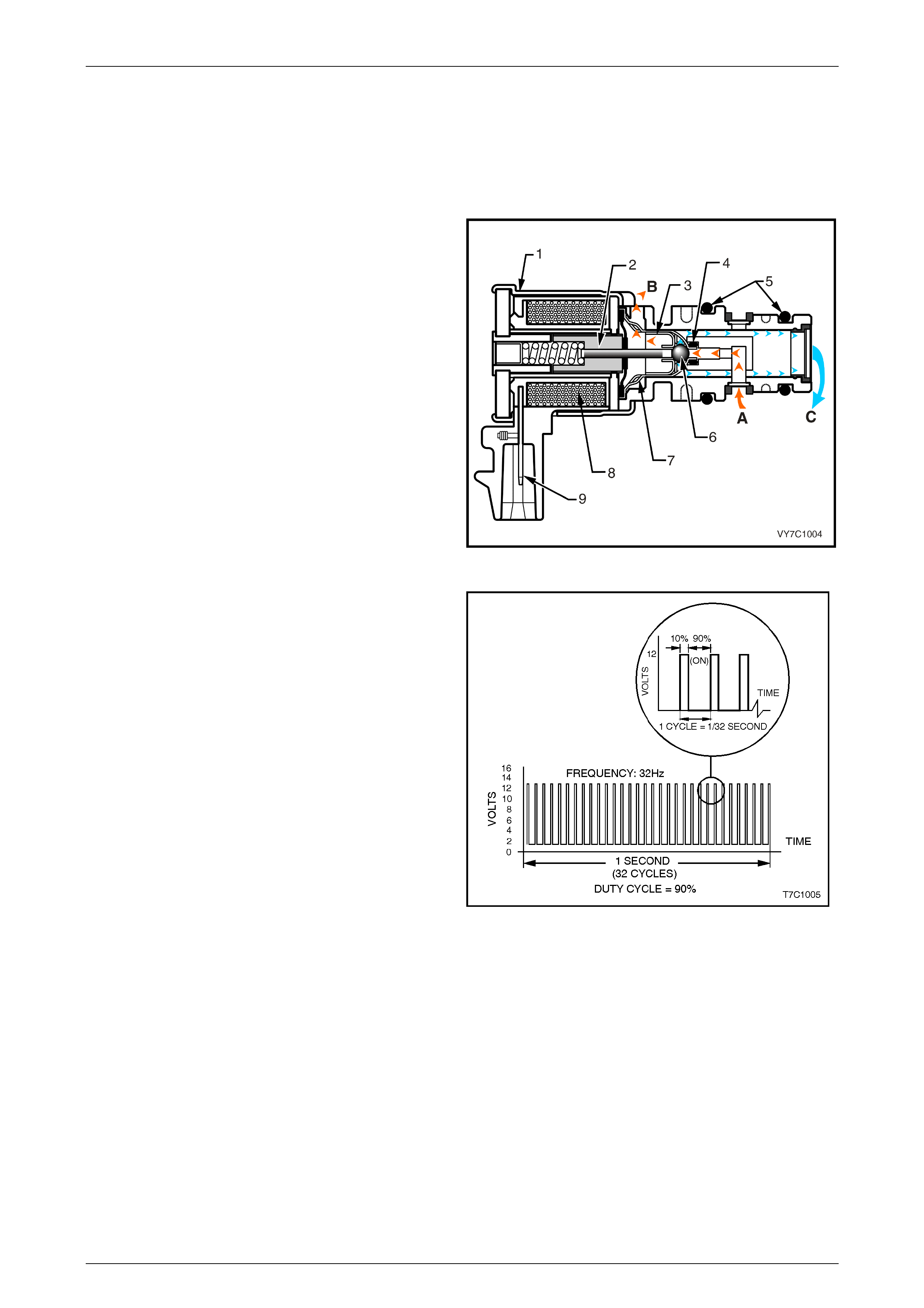
Hydra-Matic 4L65-E Automatic Transm issi on – General Information Page 7D1-3
Page 7D1-3
Torque Converter Clutch Cont rol
First applied to MY 2003 VY Series Regular Cab vehicles fitted with automatic transmission and the GEN III V8 engine,
an Electronically Controlled Converter Clutch (ECCC), is now enabled for all VY Series II vehicles fitted with automatic
transmission and the GEN III V8 engine, including MY 2004 AWD Crew Cab.
Torque Converter Clutch Pulse Width Modulated (TCC PWM) Solenoid Valve
The TCC PWM solenoid valve is a normally closed, pulse
width modulated (PWM) solenoid used to control the apply
and release of the converter clutch. The Powertrain Control
Module (PCM) operates the solenoid with a negative duty
cycle at a fixed frequency of 32 Hz to control the rate of
TCC apply/release. The solenoid's ability to "ramp" the TCC
apply and release pressures results in a smoother TCC
operation.
Legend:
1 Housing
2 Armature
3 Exhaust Seat
4 Internal O-Ring
5 O-Rings
6 Metering Ball
7 Inlet Seat
8 Coil Assembly
9 Connector Terminal
A Actuator Feed Limit (AFL) Fluid
B Exhaust
C Converter Clutch Signal (CC SIGNAL) Fluid Figure 7D1 – 2
Shown is an example of the TCC PWM solenoid, operating
with a 90% negative duty cycle at a constant operating
frequency of 32 Hz (cycles per second). The frequency
means that the solenoid is pulsed (energised) with current
from the PCM 32 times per second. The 90% negative duty
cycle means that during each of these 32 cycles the
solenoid is energised (ON) and 0 volts is measured on the
low (negative) sid e of the circu it, 90% of the time.
At road speeds below approximately 13 km/h, the negative
duty cycle will be 0%, which means that no current will flow
through the TCC PWM solenoid, deactivating it. When in
this condition, spring force will move the plunger (refer
Figure 7D1-2), seating the metering ball and blocking the
filtered Actuator Feed Limit (AFL) fluid from entering the
Converter Clutch Signal (CC SIGNAL) circuit. This action
opens the Converter Clutch Signal fluid circuit to exhaust
through the solenoid.
Above road speeds of approximately 13 km/h, the TCC
PWM solenoid will be operating at about a 90% duty cycle.
This action will cause the metering ball to close off the path
to exhaust, most of the time and allow AFL fluid to flow past
the metering ball and into the CC SIGNAL circuit, in
readiness for the apply of the torque converter clutch.
Figure 7D1 – 3
When the PCM signals TCC apply, the TCC PW M solenoid operates with a variable, negative duty cycle, ranging from
90% to 0%, with an operating frequency of 32 Hz. This allows the PCM to control the current flow through the solenoid
coil according to the duty cycle it sets. This has the effect of creating a variable magnetic field, that magnetises the
solenoid core, attracting the metering ball to seat against spring force. A high percentage duty cycle keeps the metering
ball will be seated more ofte n, thereby creat ing higher TCC signal fluid pr es sure s.
TCC PWM Solenoid Valve Operation
The TCC PWM solenoid valve is one of two electronic control components in the TCC apply and release system. The
other component is the TCC solenoid valve, which enables TCC 'ON' and 'OFF'. The other components are all hydraulic
control or regulating valves.