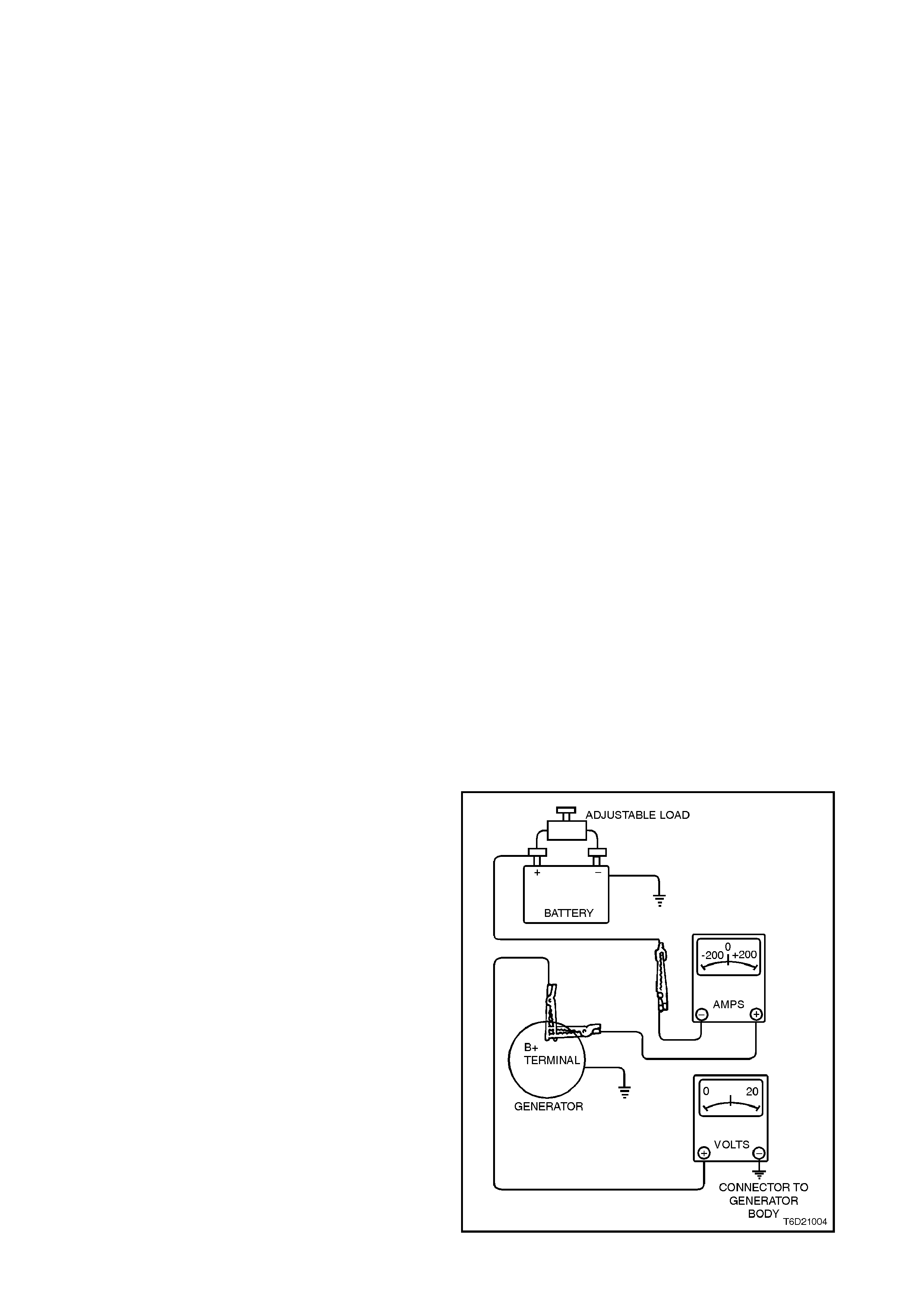
2.2 MAINTENANCE AND ON-VEHICLE TESTING
At regular intervals, inspect the terminals of the generator for corrosion, loose connectors and the wiring for
damaged insulation. Check the mounting bolts for tightness, check the drive belt for alignment and wear and the
drive pulley for damage. The drive belt adj us tment f or the engine ancillar ies, s uc h as the generator and water pump
etc., is provided by a spring-loaded tensioner. The drive belt therefore, does not require any regular adjustment.
LUBRICATION
The ball bearings supporting the rotor shaf t ar e pr e-lubr icated and s ealed, ther ef or e no lubric ation is poss ible during
service.
The bearings used in this generator are high tolerance type. If the bearings are removed during the generator
disassembly, new bearings must be installed to restore the generator to original specification.
TESTING THE GENERATOR OUTPUT AND VOLTAGE REGULATOR
Testing Prerequisites
Before testing the generator output, m ake certain that the generator circuit is thoroughly check ed for loose or dirty
connections. The generator must always be connected to the battery during testing, otherwise damage to the
diodes could result.
The battery should be fully charged. Test the specific gravity of the individual cells. The readings should be within 10
points of each other. It is recommended that the average specific gravity should be 1.260 or higher.
A load test should be carried out to determine the ability of the battery to supply and accept c urrent. This is a good
indicator as to the general condition of the battery. Refer to Section 12A BATT ERY AND CABLES of the VT Series
I Service Information for details of battery testing.
The generator warning light, in addition to indicating that the generator is charging, is also nec essary for initial field
excitation.
Inspect drive belt and tensioner markings to determine if belt is within operating limits. Replace belt if it is
excessively worn or outside tensioner’s operating range, refer to Section 6A1 ENGINE MECHANICAL - V6
ENGINE of the VT Series I Service Information for details.
TESTING GENERATOR OUTPUT
Regulating Voltage Test On The Vehicle
1. Ensure that all the electrical equipment is
turned off, and the ignition switch is in the OFF
position.
2. Disconnect battery earth cable at battery.
3. Disconnect the generator positive lead (Red
wire) from the ‘B+’ generator terminal.
4. Connect the positive lead of an ammeter (0 –
100 amp scale) to the generator ‘B+’ terminal,
and the ammeter negative lead to the
disconnected generator positive lead (Red
wire).
5. Connect positive lead of a voltmeter (0 – 20
volt scale minimum) to the generator ‘B+’
term inal, and voltmeter negative lead to a good
earth connection on the generator housing.
CAUTION: INSULATE THE GENERATOR
POSITIVE LEAD (RED WIRE) TERMINAL TO
PREVENT CONTACT WITH ANY METAL PART
OF THE VEHICLE. IF THE TERMINAL IS
EARTHED, DAMAGE TO THE CHARGING
CIRCUIT WILL RESULT WHEN THE BATTERY
IS RECONNECTED.
6. Reconnect the battery earth cable. Fit a loading
device across battery terminals, i.e. an
adjustable carbon pile.
NOTE: Loading device must have a minimum
power consumption of 1000 watts.
Figure 6D1-1-4