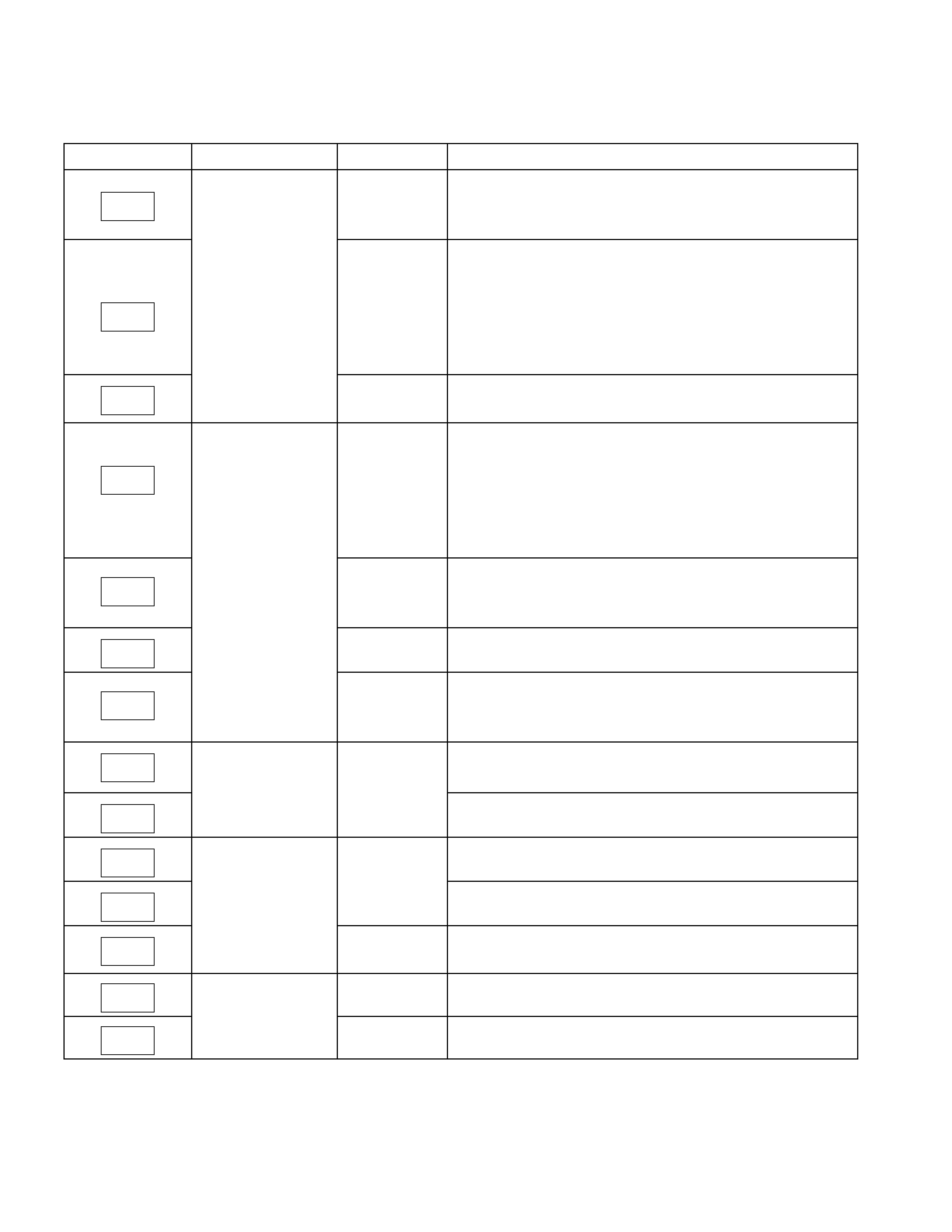
Grounding Poi nt
Reference Table
Connector No. Cable harness Location Parts (Load)
B-9 Body-LH Fan SW, FRT power window & door lock SW-
passenger side, RR power window SW, Key, light O/D
Off switch (4JH1-A/T)
B-28 Body harness Body-RH
Illumination light (meter, Heater & A/C control panel,
Cigarette lighter, Ashtray, RR defog SW, Audio, Hazard
SW), Turn signal indicator light, FRT power window &
door lock SW-driver side, Power window relay, Door
mirror control SW, RR defog, RR defog SW, Door lock
SW-driver side, Audio, Clock, Cigarette lighter
B-34 Body-RR Fuel tank unit, Tail light, License plate light, Fuel pump,
Stop light, RR turn signal light, Back up light
C-2 Fender-RH
Vehicle speed sensor, 4WD SW, Brake fluid level SW,
Heater relay, Dimmer⋅passing SW, Lighter SW, Starter
relay, Windshield intermittent relay, Windshield wiper
motor, Flasher unit, Side turn signal light-RH,
Condenser fan relay, ST cut relay, Idle up resister
(4JH1-TURBO)
C-36 Engine room
harness Fender-LH Clearance light, Seat belt SW Windshield washer
motor, Side turn signal light-LH, FRT turn signal light,
ST cut relay, ECM (4JH1TC)
C-95 Engine-RH Condenser fan
C-94 Engine-LH Speedometer, Tachometor (W/Tachometer), Engine
coolant temperature gauge (W/Tachometer), Fuel
gauge
E-10 ECM (C22NE), Injection pump (4JH1TC), TCM
(4JH1TC)
E-16 Engine harness Engine ECM (C22NE)
E-72 Data link connector, ECM, Crank angle sensor
E-73 Engine harness
Common
chamber- RH Ignition coil, ECM
E-74 Common
chamber- LH Ignition coil, ECM, MAF sensor shield, Cam angle
sensor shield, Throttle position sensor shield
P-7 Body-RH Right side of body
P-10 Battery harness Body-RH Right side of Engine