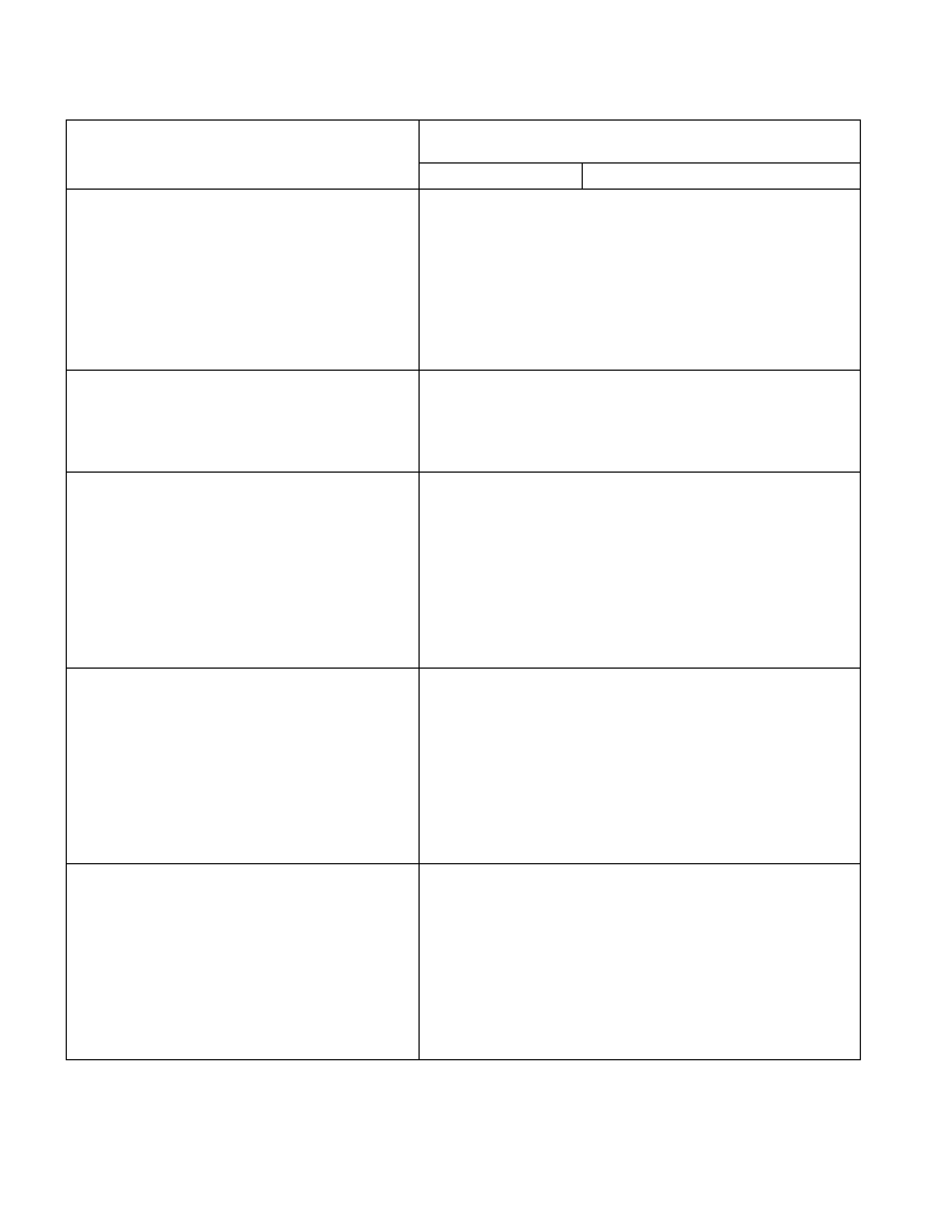
4×
××
×4 MODEL & 4X2 V6 ENG I NE
Front Suspension Type Independent wishbone arms. torsion bar springs with
stabilizer bar
Short wheel base Long wheel base
Front wheel alignment
When not loaded
Tread mm(in) 1438 (56.61)
Camber 0°30' ± 60'
(Left and right side to be equal within 45')
Caster *1°55' ± 45' | *2°10' ± 45'
* Left and right side to be equal within 35'
Toe-in mm(in) 2 ± 2 (0.08±0.08)
Kingpin inclination 10° ± 60'
Torsion Bar Spring Data
Length × diameter mm(in) 998×23.4 (39.29×0.321)
Wheel Rate/Side N/mm (kg/mm/lb/in) 32.6 (3.33/186)
Spring Constant N⋅m/deg (kg⋅m/deg/lb⋅ft) 41.2 (4.20/30.4)
Spring Capacity N (kg/lb) Gasoline engine 490 (500/1102)
Shock Absorber Data
Type Hydraulic double acting, telescopic
Maximum Length mm(in) 375 (14.76)
Minimum Length mm(in) 235 (9.25)
Stroke mm(in) 140 (5.51)
Damping Force
Rebound Side 110 kg at 0.3 m/sec.
(1079 N at 0.3 m/sec./243 lb. at 11.8 in/sec.)
Compression Side 32 kg at 0.3 m/sec.
(313 N at 0.3 m/sec./70.5 lb. at 11.8 in/sec.)
Shock Absorber Data (For Australia)
Type Gas-sealed, hydraulic double acting telescopic
Maximum Length mm(in) 377 (14.84)
Minimum Length mm(in) 237 (9.33)
Stroke mm(in) 140(5.51)
Damping Force
Rebound Side 200 kg at 0.3 m/sec.
(1961 N at 0.3 m/sec./441 lb. at 11.8 in/sec.)
Compression Side 138 kg at 0.3 m/sec.
(1353 N at 0.3 m/sec./304 lb. at 11.8 in/sec.)
Shock Absorber Data (TFS25)
Type Gas-sealed, hydraulic double acting telescopic
Maximum Length mm(in) 377 (14.84)
Minimum Length mm(in) 237 (9.33)
Stroke mm(in) 140(5.51)
Damping Force
Rebound Side 199 kg at 0.3 m/sec.
(439 lb. at 11.8 in/sec./1952 N at 0.3 m/sec.)
Compression Side 126 kg at 0.3 m/sec.
(278 lb. at 11.8 in/sec./1236 N at 0.3 m/sec.)