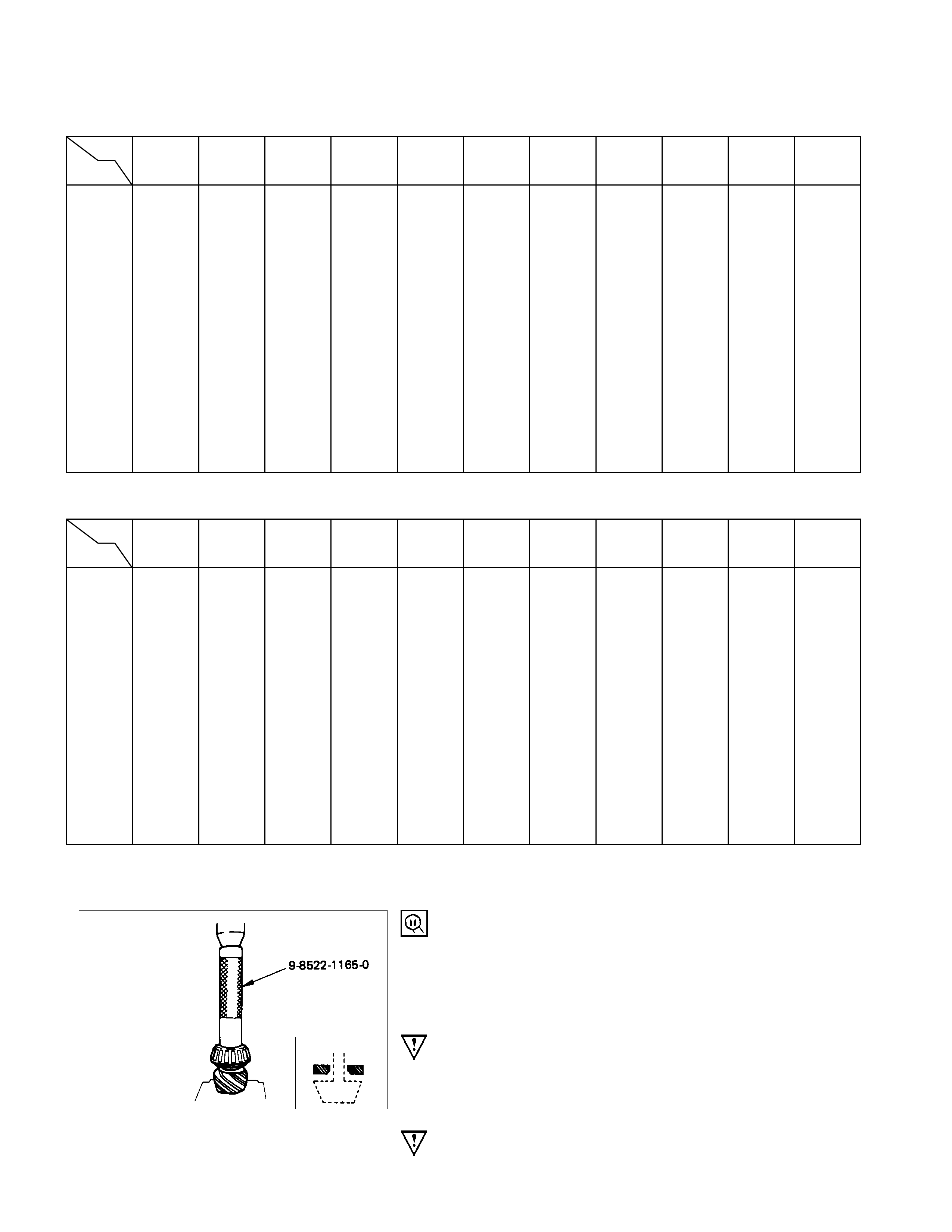
(7)Select the shim using table below.
[194 mm] mm(in)
Pinion
marking +10 +8 +6 +4 +2 0 -2 -4 -6 -8 -10
Dial indicator
reading (inches)
0.081 2.18 (0.0858)
0.082 2.18 (0.0858) 2.20 (0.0866)
0.083 2.18 (0.0858) 2.20 (0.0866) 2.24 (0.0882)
0.084 2.18 (0.0858) 2.20 (0.0866) 2.24 (0.0882) 2.26 (0.0890)
0.085 2.18 (0.0858) 2.20 (0.0866) 2.24 (0.0882) 2.26 (0.0890) 2.28 (0.0898)
0.086 2.18 (0.0858) 2.20 (0.0866) 2.24 (0.0882) 2.26 (0.0890) 2.28 (0.0898) 2.32 (0.0914)
0.087 2.18 (0.0858) 2.20 (0.0866) 2.24 (0.0882) 2.26 (0.0890) 2.28 (0.0898) 2.32 (0.0914) 2.34 (0.0921)
0.088 2.18 (0.0858) 2.20 (0.0866) 2.24 (0.0882) 2.26 (0.0890) 2.28 (0.0898) 2.32 (0.0914) 2.34 (0.0921) 2.36 (0.0929)
0.089 2.18 (0.0858) 2.20 (0.0866) 2.24 (0.0882) 2.26 (0.0890) 2.28 (0.0898) 2.32 (0.0914) 2.34 (0.0921) 2.36 (0.0929) 2.38 (0.0937)
0.090 2.18 (0.0858) 2.20 (0.0866) 2.24 (0.0882) 2.26 (0.0890) 2.28 (0.0898) 2.32 (0.0914) 2.34 (0.0921) 2.36 (0.0929) 2.38 (0.0937) 2.42 (0.0953)
0.091 2.18 (0.0858) 2.20 (0.0866) 2.24 (0.0882) 2.26 (0.0890) 2.28 (0.0898) 2.32 (0.0914) 2.34 (0.0921) 2.36 (0.0929) 2.38 (0.0937) 2.42 (0.0953) 2.44 (0.0961)
0.092 2.20 (0.0866) 2.24 (0.0882) 2.26 (0.0890) 2.28 (0.0898) 2.32 (0.0914) 2.34 (0.0921) 2.36 (0.0929) 2.38 (0.0937) 2.42 (0.0953) 2.44 (0.0961) 2.46 (0.0969)
0.093 2.24 (0.0882) 2.26 (0.0890) 2.28 (0.0898) 2.32 (0.0914) 2.34 (0.0921) 2.36 (0.0929) 2.38 (0.0937) 2.42 (0.0953) 2.44 (0.0961) 2.46 (0.0969) 2.48 (0.0977)
0.094 2.26 (0.0890) 2.28 (0.0898) 2.32 (0.0914) 2.34 (0.0921) 2.36 (0.0929) 2.38 (0.0937) 2.42 (0.0953) 2.44 (0.0961) 2.46 (0.0969) 2.48 (0.0977) 2.52 (0.0992)
0.095 2.28 (0.0898) 2.32 (0.0914) 2.34 (0.0921) 2.36 (0.0929) 2.38 (0.0937) 2.42 (0.0953) 2.44 (0.0961) 2.46 (0.0969) 2.48 (0.0977) 2.52 (0.0992) 2.54 (0.1000)
0.096 2.32 (0.0914) 2.34 (0.0921) 2.36 (0.0929) 2.38 (0.0937) 2.42 (0.0953) 2.44 (0.0961) 2.46 (0.0969) 2.48 (0.0977) 2.52 (0.0992) 2.54 (0.1000) 2.56 (0.1008)
0.097 2.34 (0.0921) 2.36 (0.0929) 2.38 (0.0937) 2.42 (0.0953) 2.44 (0.0961) 2.46 (0.0969) 2.48 (0.0977) 2.52 (0.0992) 2.54 (0.1000) 2.56 (0.1008)
0.098 2.36 (0.0929) 2.38 (0.0937) 2.42 (0.0953) 2.44 (0.0961) 2.46 (0.0969) 2.48 (0.0977) 2.52 (0.0992) 2.54 (0.1000) 2.56 (0.1008)
0.099 2.38 (0.0937) 2.42 (0.0953) 2.44 (0.0961) 2.46 (0.0969) 2.48 (0.0977) 2.52 (0.0992) 2.54 (0.1000) 2.56 (0.1008)
0.000 2.42 (0.0953) 2.44 (0.0961) 2.46 (0.0969) 2.48 (0.0977) 2.52 (0.0992) 2.54 (0.1000) 2.56 (0.1008)
0.001 2.44 (0.0961) 2.46 (0.0969) 2.48 (0.0977) 2.52 (0.0992) 2.54 (0.1000) 2.56 (0.1008)
0.002 2.46 (0.0969) 2.48 (0.0977) 2.52 (0.0992) 2.54 (0.1000) 2.56 (0.1008)
0.003 2.48 (0.0977) 2.52 (0.0992) 2.54 (0.1000) 2.56 (0.1008)
0.004 2.52 (0.0992) 2.54 (0.1000) 2.56 (0.1008)
0.005 2.54 (0.1000) 2.56 (0.1008)
0.006 2.56 (0.1008)
[220 mm] mm(in)
Pinion
marking +10 +8 +6 +4 +2 0 -2 -4 -6 -8 -10
Dial indicator
reading (inches)
0.073 1.94 (0.0764) 1.96 (0.0772)
0.074 1.94 (0.0764) 1.96 (0.0772) 1.98 (0.0779)
0.075 1.94 (0.0764) 1.96 (0.0772) 1.98 (0.0779) 2.00 (0.0787)
0.076 1.94 (0.0764) 1.96 (0.0772) 1.98 (0.0779) 2.00 (0.0787) 2.02 (0.0795) 2.04 (0.0803)
0.077 1.96 (0.0772) 1.98 (0.0779) 2.00 (0.0787) 2.02 (0.0787) 2.04 (0.0803) 2.06 (0.0811)
0.078 1.94 (0.0764) 1.96 (0.0772) 1.98 (0.0779) 2.00 (0.0787) 2.02 (0.0787) 2.04 (0.0803) 2.06 (0.0811) 2.08 (0.0819)
0.079 1.94 (0.0764) 1.96 (0.0772) 1.98 (0.0779) 2.00 (0.0787) 2.02 (0.0787) 2.04 (0.0803) 2.06 (0.0811) 2.08 (0.0819) 2.10 (0.0827)
0.080 1.94 (0.0764) 1.96 (0.0772) 1.98 (0.0779) 2.00 (0.0787) 2.02 (0.0787) 2.04 (0.0803) 2.06 (0.0811) 2.08 (0.0819) 2.10 (0.0827) 2.12 (0.0835) 2.14 (0.0842)
0.081 1.96 (0.0772) 1.98 (0.0779) 2.00 (0.0787) 2.02 (0.0787) 2.04 (0.0803) 2.06 (0.0811) 2.08 (0.0819) 2.10 (0.0827) 2.12 (0.0835) 2.14 (0.0842) 2.16 (0.0850)
0.082 1.98 (0.0779) 2.00 (0.0787) 2.02 (0.0787) 2.04 (0.0803) 2.06 (0.0811) 2.08 (0.0819) 2.10 (0.0827) 2.12 (0.0835) 2.14 (0.0842) 2.16 (0.0850) 2.18 (0.0858)
0.083 2.00 (0.0787) 2.02 (0.0787) 2.04 (0.0803) 2.06 (0.0811) 2.08 (0.0819) 2.10 (0.0827) 2.12 (0.0835) 2.14 (0.0842) 2.16 (0.0850) 2.18 (0.0858) 2.20 (0.0866)
0.084 2.04 (0.0803) 2.06 (0.0811) 2.08 (0.0819) 2.10 (0.0827) 2.12 (0.0835) 2.14 (0.0842) 2.16 (0.0850) 2.18 (0.0858) 2.20 (0.0866) 2.22 (0.0874) 2.24 (0.0882)
0.085 2.06 (0.0811) 2.08 (0.0819) 2.10 (0.0827) 2.12 (0.0835) 2.14 (0.0842) 2.16 (0.0850) 2.18 (0.0858) 2.20 (0.0866) 2.22 (0.0874) 2.24 (0.0882) 2.26 (0.0890)
0.086 2.08 (0.0819) 2.10 (0.0827) 2.12 (0.0835) 2.14 (0.0842) 2.16 (0.0850) 2.18 (0.0858) 2.20 (0.0866) 2.22 (0.0874) 2.24 (0.0882) 2.26 (0.0890) 2.28 (0.0898)
0.087 2.12 (0.0835) 2.14 (0.0842) 2.16 (0.0850) 2.18 (0.0858) 2.20 (0.0866) 2.22 (0.0874) 2.24 (0.0882) 2.26 (0.0890) 2.28 (0.0898) 2.30 (0.0906) 2.32 (0.0913)
0.088 2.14 (0.0842) 2.16 (0.0850) 2.18 (0.0858) 2.20 (0.0866) 2.22 (0.0874) 2.24 (0.0882) 2.26 (0.0890) 2.28 (0.0898) 2.30 (0.0906) 2.32 (0.0913) 2.34 (0.0921)
0.089 2.16 (0.0850) 2.18 (0.0858) 2.20 (0.0866) 2.22 (0.0874) 2.24 (0.0882) 2.26 (0.0890) 2.28 (0.0898) 2.30 (0.0906) 2.32 (0.0913) 2.34 (0.0921) 2.36 (0.0929)
0.090 2.18 (0.0858) 2.20 (0.0866) 2.22 (0.0874) 2.24 (0.0882) 2.26 (0.0890) 2.28 (0.0898) 2.30 (0.0906) 2.32 (0.0913) 2.34 (0.0921) 2.36 (0.0929)
0.091 2.22 (0.0874) 2.24 (0.0882) 2.26 (0.0890) 2.28 (0.0898) 2.30 (0.0906) 2.32 (0.0913) 2.34 (0.0921) 2.36 (0.0929)
0.092 2.24 (0.0882) 2.26 (0.0890) 2.28 (0.0898) 2.30 (0.0906) 2.32 (0.0913) 2.34 (0.0921) 2.36 (0.0929)
0.093 2.26 (0.0890) 2.28 (0.0898) 2.30 (0.0906) 2.32 (0.0913) 2.34 (0.0921) 2.36 (0.0929)
0.094 2.28 (0.0898) 2.30 (0.0906) 2.32 (0.0913) 2.34 (0.0921) 2.36 (0.0929)
0.095 2.32 (0.0913) 2.34 (0.0921) 2.36 (0.0929)
0.096 2.34 (0.0921) 2.36 (0.0929)
0.097 2.36 (0.0929)
Note :
When ordering shims, find the part number in the Parts Catalog by using the thickness of the shims listed in
the above table. 4. Inner Bearing
Place the shim on the drive pinion with the chamfered side
turned toward the pinion head, then attach the inner bearing to
the pinion using an installer and a press.
Installer : 9-8522-1165-0
(J-6133-01)
NOTE :
Do not press on the roller cage.
Press only on the inner race.
5. Collapsible Spacer