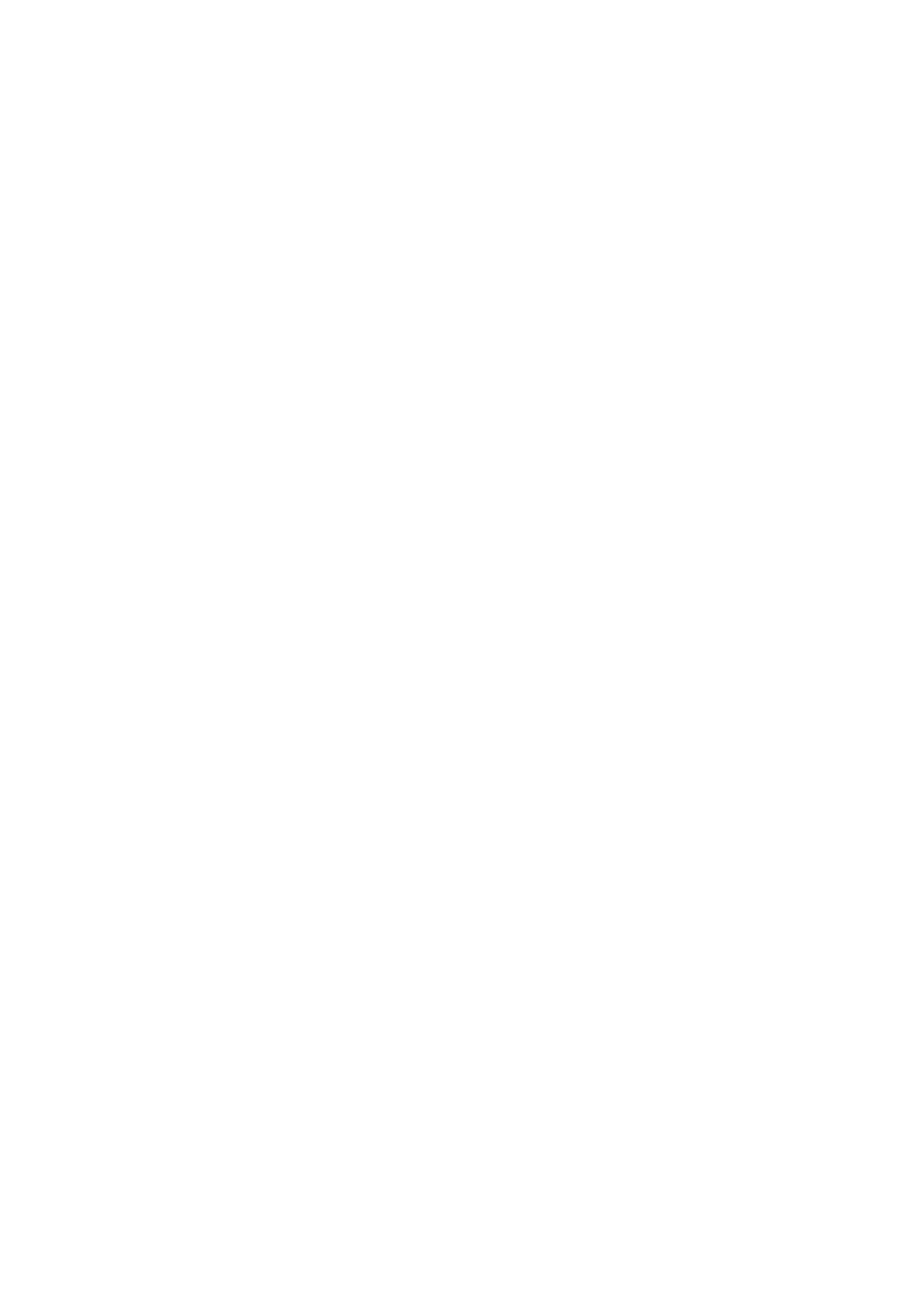
Diagnostic T rouble Code (DTC) P0115 (Symptom Code
1) (Flash Code 14) Engine Coolant Temperature
Sensor Circuit High Input
Diagnostic T rouble Code (DTC) P0115 (Symptom Code
2) Flash Code 14) Engine Coolant Temperature
Sensor Circ uit Low Input
Diagnostic T rouble Code (DTC) P0180 (Symptom Code
B) (Flash Code 15) Fuel Temperature Sensor Circuit
Range/performance
Diagnostic T rouble Code (DTC) P0215 (Symptom Code
A) (Flash Code 52) Fuel Cutoff Solenoid Valve
Malfunction
Diagnostic T rouble Code (DTC) P0215 (Symptom Code
B) (Flash Code 52) Fuel Cutoff Solenoid Valve Circuit
High Input
Diagnostic T rouble Code (DTC) P0215 (Symptom Code
C) (Flash Code 52) Fuel Cutoff Solenoid V alve Always
Active
Diagnostic T rouble Code (DTC) P0215 (Symptom Code
D) (Flash Code 52) Fuel Cutoff Solenoid Valve
Malfunction
Diagnostic T rouble Code (DTC) P0216 (Symptom Code
A) (Flash Code 54) Injection Timing Control Circuit
Malfunction (Timer Deviation)
Diagnostic T rouble Code (DTC) P0216 (Symptom Code
B) (Flash Code 54) Injection Timing Control Circuit
Malfunction (Timer Fluctuation )
Diagnostic T rouble Code (DTC) P0251 (Symptom Code
6) (Flash Code 53) Injection Pump Malfunction
Diagnostic T rouble Code (DTC) P0251 (Symptom Code
7) (Flash Code 53) Injection Pump Malfunction
Diagnostic T rouble Code (DTC) P0251 (Symptom Code
9) (Flash Code 53) Injection Pump Malfunction
Diagnostic T rouble Code (DTC) P0251 (Symptom Code
A) (Flash Code 53) Injection Pump Malfunction
Diagnostic T rouble Code (DTC) P0251 (Symptom Code
B) (Flash Code 53) Injection Pump Malfunction
Diagnostic T rouble Code (DTC) P0251 (Symptom Code
D) (Flash Code 53) Injection Pump Malfunction
Diagnostic T rouble Code (DTC) P0251 (Symptom Code
E) (Flash Code 53) Injection Pump Malfunction
Diagnostic T rouble Code (DTC) P0335 (Symptom Code
B) (Flash Code 43)crankshaft Position Sensor Circuit
Malfunction
Diagnostic T rouble Code (DTC) P0335 (Symptom Code
D) (Flash Code 43) Crankshaft Position Sensor
Malfunction
Diagnostic T rouble Code (DTC) P0335 (Symptom Code
E) (Flash Code 43) Engine S peed Input Circuit Range/
performance
Diagnostic T rouble Code (DTC) P0380 (Symptom Code
4) (Flash Code 66) Glow Relay Circuit Voltage Low
Diagnostic T rouble Code (DTC) P0380 (Symptom Code
8) Flash Code 66) Glow Relay Circuit Voltage High
Diagnostic Trouble Code (DTC) P0381 (Sub Code 4)
(Flash Code 67) Glow Plug Indicator Circuit Voltage
Low
Diagnostic Trouble Code (DTC) P0381 (Sub Code 8)
(Flash Code 67) Glow Plug Indicator Circuit Voltage
High
Diagnostic T rouble Code (DTC) P0500 (Symptom Code
1) (Flash Code 24) V ehicle Speed Sensor Circuit High
Input
Diagnostic T rouble Code (DTC) P0500 (Symptom Code
A) (Flash Code 24) V ehicle Speed Sensor Input Signal
Frequency Too High
Diagnostic T rouble Code (DTC) P0500 (Symptom Code
B) (Flash Code 24) Vehicle Speed Sensor Incorrect
Signal
Diagnostic T rouble Code (DTC) P0560 (Symptom Code
1) (Flash Code 35) System Voltage Too High
Diagnostic T rouble Code (DTC) P0560 (Symptom Code
2) (Flash Code 35) System Voltage Too Low
Diagnostic T rouble Code (DTC) P0560 (Symptom Code
A) (Flash Code 35) System V oltage Malfunction (PSG)
Diagnostic T rouble Code (DTC) P0561 (Symptom Code
A) (Flash Code 18) System V oltage Circuit Malfunction
Diagnostic T rouble Code (DTC) P0561 (Symptom Code
B) (Flash Code 18) System V oltage Circuit Malfunction
Diagnostic Trouble Code (DTC) P0602 ECU
Programming Error
Diagnostic T rouble Code (DTC) P0606 (Symptom Code
A) (Flash Code 28) ECU Malfunction
Diagnostic T rouble Code (DTC) P0606 (Symptom Code
B) (Flash Code 28) ECU Malfunction
Diagnostic T rouble Code (DTC) P0645 (Symptom Code
4) (Flash Code 46) A/C Compressor Relay Circuit
Voltage Low
Diagnostic T rouble Code (DTC) P0645 (Symptom Code
8) (Flash Code 46) A/C Compressor Relay Circuit
Voltage High
Diagnostic T rouble Code (DTC) P0703 (Symptom Code
A) (Flash Code 25) Brake Switch Malfunction
Diagnostic T rouble Code (DTC) P0703 (Symptom Code
B) (Flash Code 25) Brake Switch Malfunction
Diagnostic T rouble Code (DTC) P0704 (Symptom Code
6) (Flash Code 57) Clutch Switch Circuit Malfunction
Diagnostic Trouble Code (DTC) P1105 (Symptom Code
1) (Flash Code 86) Barometric Pressure Sensor Circuit
High Input
Diagnostic Trouble Code (DTC) P1105 (Symptom Code
2) (Flash Code 86) Barometric Pressure Sensor Circuit
Low Input
Diagnostic Trouble Code (DTC) P1120 (Symptom Code
1) (Flash Code 21) Pedal/throttle Position Sensor
Circuit High Input
Diagnostic Trouble Code (DTC) P1120 (Symptom Code
7) (Flash Code 21) Pedal/throttle Position Sensor
Voltage Supply Circuit High Input
Diagnostic Trouble Code (DTC) P1120 (Symptom Code
9) (Flash Code 21) Pedal/throttle Position Sensor
Voltage Supply Circuit Low Input
Diagnostic Trouble Code (DTC) P1120 (Symptom Code
D) (Flash Code 21) Pedal/throttle Position Sensor
Brake Switch Error
Diagnostic Trouble Code (DTC) P1120 (Symptom Code
E) (Flash Code 21) Pedal/throttle Position Sensor Idle
Position Switch Error