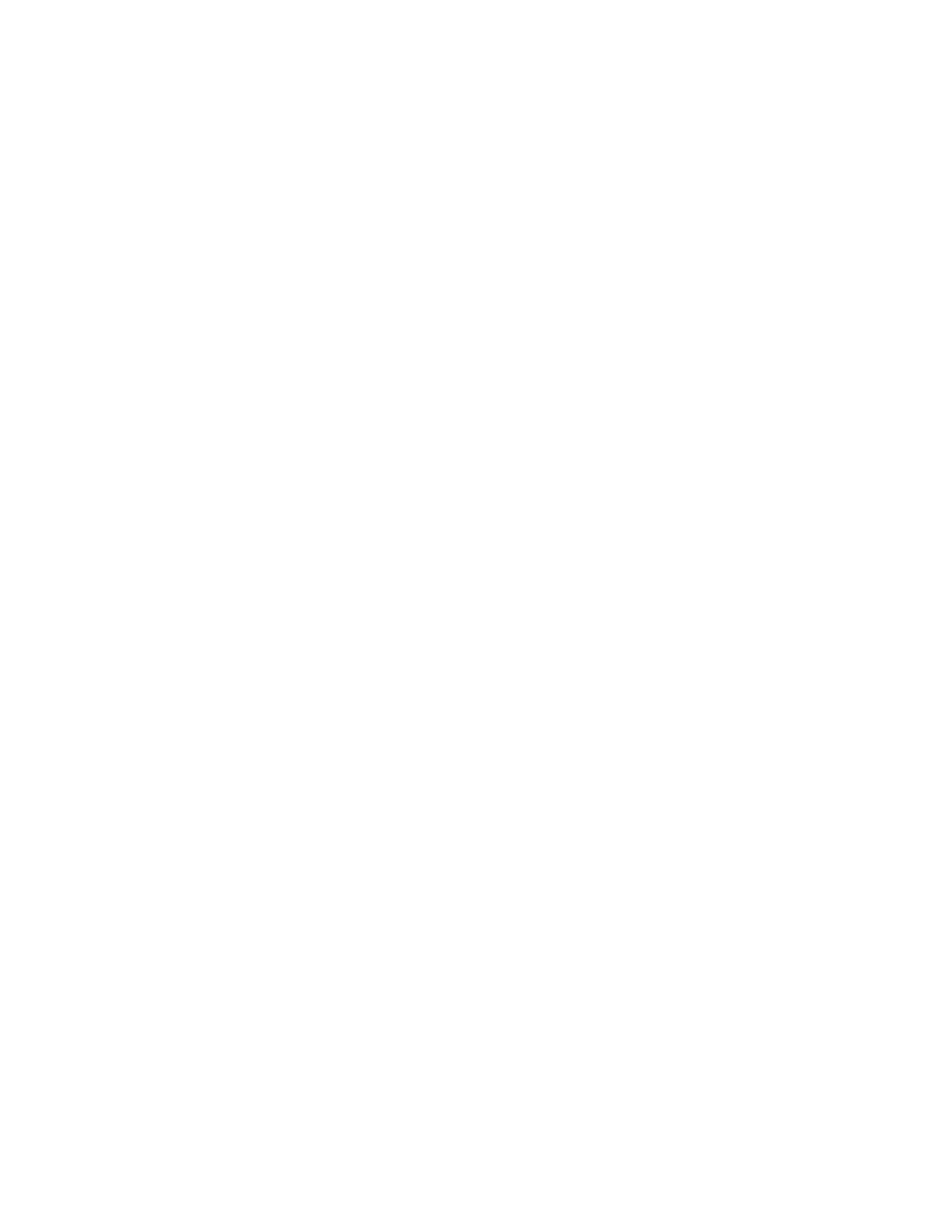
SECTION 6D - CHARGING SYSTEM (6VD1 MODELS)
Service Precaution
Charging System
General Description
General On-Vehicle Inspection
Generator
Removal
Inspection
Installation
Disassembled View
Disassembly
Inspection and Repair
Reassembly
Bench Test
Main Data and Specifications
Service Precaut ion
WARNING: THIS VEHICLE HAS A SUPPLEMENTAL
RESTRAINT SYSTEM (SRS). REFER TO THE SRS
COMPONENT AND WIRING LO CATION VIEW IN
ORDER TO DETERMINE WHETHER YOU ARE
PERFORMING SERVICE ON OR NEAR THE SRS
COMPONENTS OR THE SRS WIRING. WHEN YOU
ARE PERFORMING SERVICE ON OR NEAR THE SRS
COMPONENTS OR THE SRS WIRING, REFER TO
THE SRS SERVICE INFORMATION. FAILURE TO
FOLLOW WARNINGS COULD RESULT IN POSSIBLE
AIR BAG DEPLOYMENT, PERSONAL INJURY, OR
OTHERWISE UNNEEDED SRS SYSTEM REPAIRS.
CAUTION: Always use the correct fastener in the
proper location. When you replace a fastener , use
ONLY the exact part number for that application.
HOLDEN will call out those fasteners that require
replacement after removal HOLDEN will also call out
the fasteners that require thread lockers or thread
sealant. UNLESS OTHERWISE SPECIFIED, do not
use supplemental coatings (Pa ints, greases, or other
corrosion inhibitors) on threaded fasteners or
fastener join t interf ac es. Gen eral l y , such coating s
adversely affect the fastener torque and the joint
clamping force, and may damage the fastener . When
you install fasteners, use the correct tightening
sequence and specifications. Following these
instructions can help you avoid damage to parts and
systems.