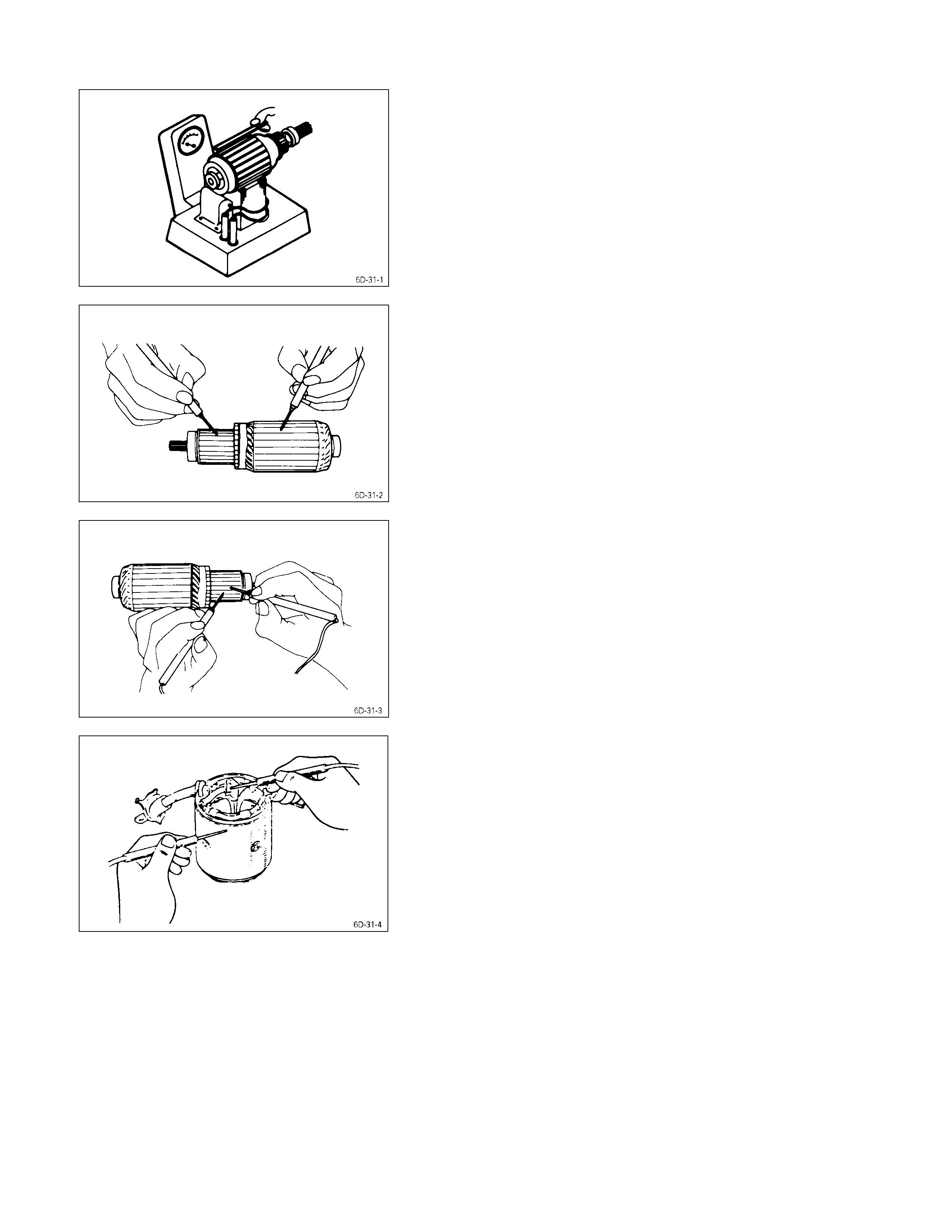
5. Test the armature for short circuiting.
a. Place the armature in a growler tester.
b. Hold a hacksaw blade against the armature core.
If the armature has a short circuit, the hacksaw blade
will vibrate.
Replace the armature if there is a short circuit.
6. Use a circuit tester to check the armature for
grounding.
1) Hold one probe of the circuit tester against the
commutator segment.
2) Hold the other circuit tester probe against the
armature core.
If the circuit tester indicates continuity, the armature is
grounded.
The armature must be replaced.
7. Use the circuit tester to check the armature for
continuity.
1) Hold the circuit tester probes against two armature
core segments.
2) Repear Step 1 at different segments of the
armature core.
There should be continuity between all segments of
the armature core.
If there is not, the armature must be replaced.
Yoke
1. Use a circuit tester to check the field winding ground.
1) Hold one circuit tester probe against the field
winding end or brush.
2) Hold the other circuit tester probe against the bare
surface of the yoke body.
There should be no continuity.
If there is continuity, the field coil is grounded.
The yoke must be replaced.