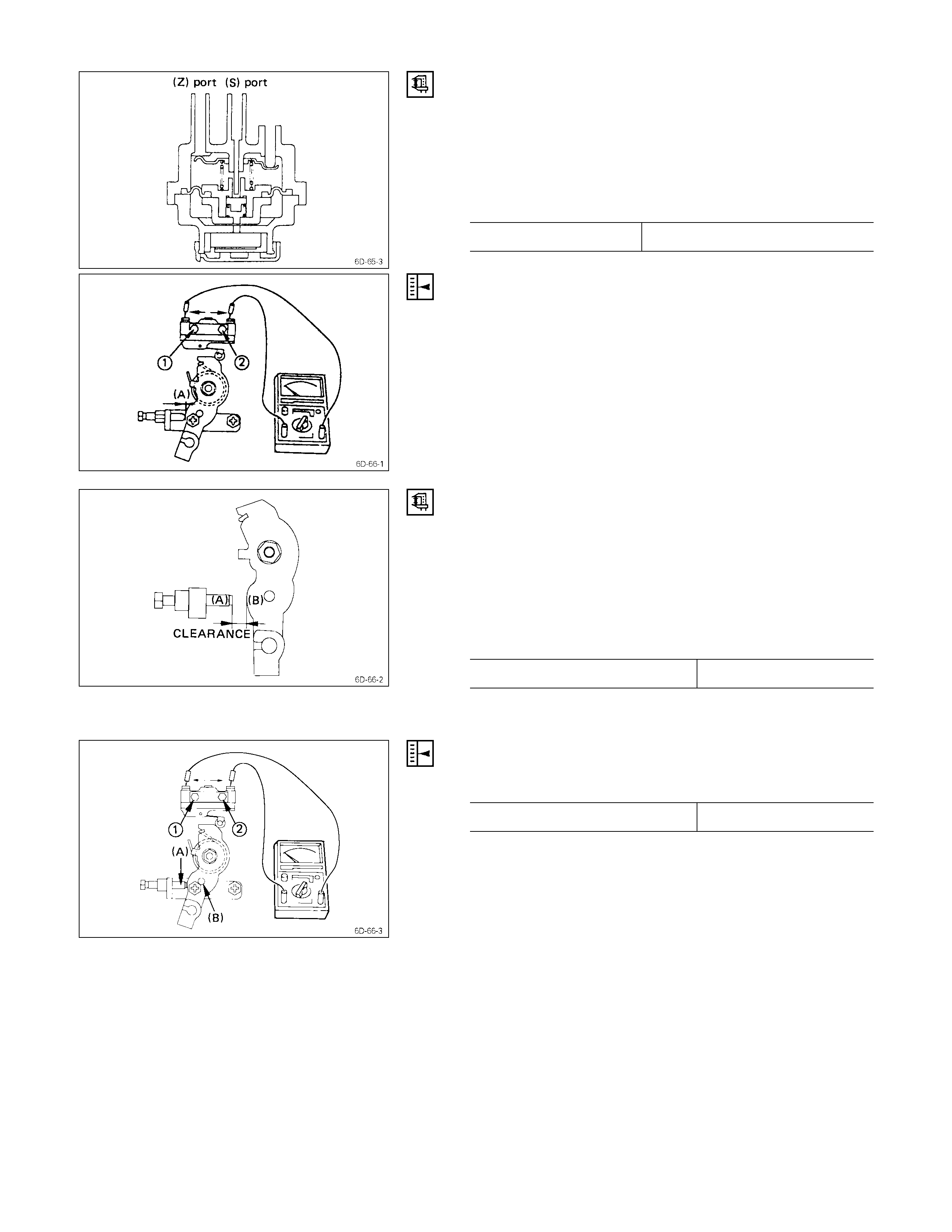
VACUUM REG ULATOR VALVE
Check the vacuum regulator valve operating pressure.
1. Apply a pressure of − 450 mmHg (− 17.7 Hg) to port
(S).
Measure the regulator pressure at port (Z).
Regulator Operating Pressure mmHg (Hg)
Standard reading − 235 to − 265 (− 9.3 to − 10.4)
HALF ACCEL. SW ITCH ADJUSTMENT (ONLY 4JA1T)
1. Insert a feeler gauge of 6 mm thickness between the
idle adjust screw end and control lever (A).
2. Loosen each bolts ( & ).
3. Set the circuit tester to micro-switch harness.
4. Find out the just continuity from OFF to ON position
with moving the micro-switch in the direction of the
arrow.
5. Tigten each bolts ( & ).
HALF ACCEL. SWITCH (ON THE VEHICLE)
Inspection
1. Connect a circuit tester to the half accel. switch
connector terminals.
2. Operate control lever slowly to a point where continuity
is switched over from “ON” to “OFF”. Then measure
the clearance between the idle stopper bolt (A) and
control lever (B).
Standard clearance mm (in) 5.0 - 7.8 (0.2 - 0.3)
If the clearance is out of the range, the switch must be
adjusted.
Adjustment
1. Insert a feeler gauge of specified thickness between
the idle stopper bolt (A) and control lever (B).
Adjustment clearance mm (in) 5.0 (0.2)
2. Loosen two switch bolts.
3. Connect a circuit tester to the switch connector
terminals.
4. Moving the switch in directions indicated by arrows.
Check to make sure of the point where continuity is
cut.
5. Tighten the two bolts & .