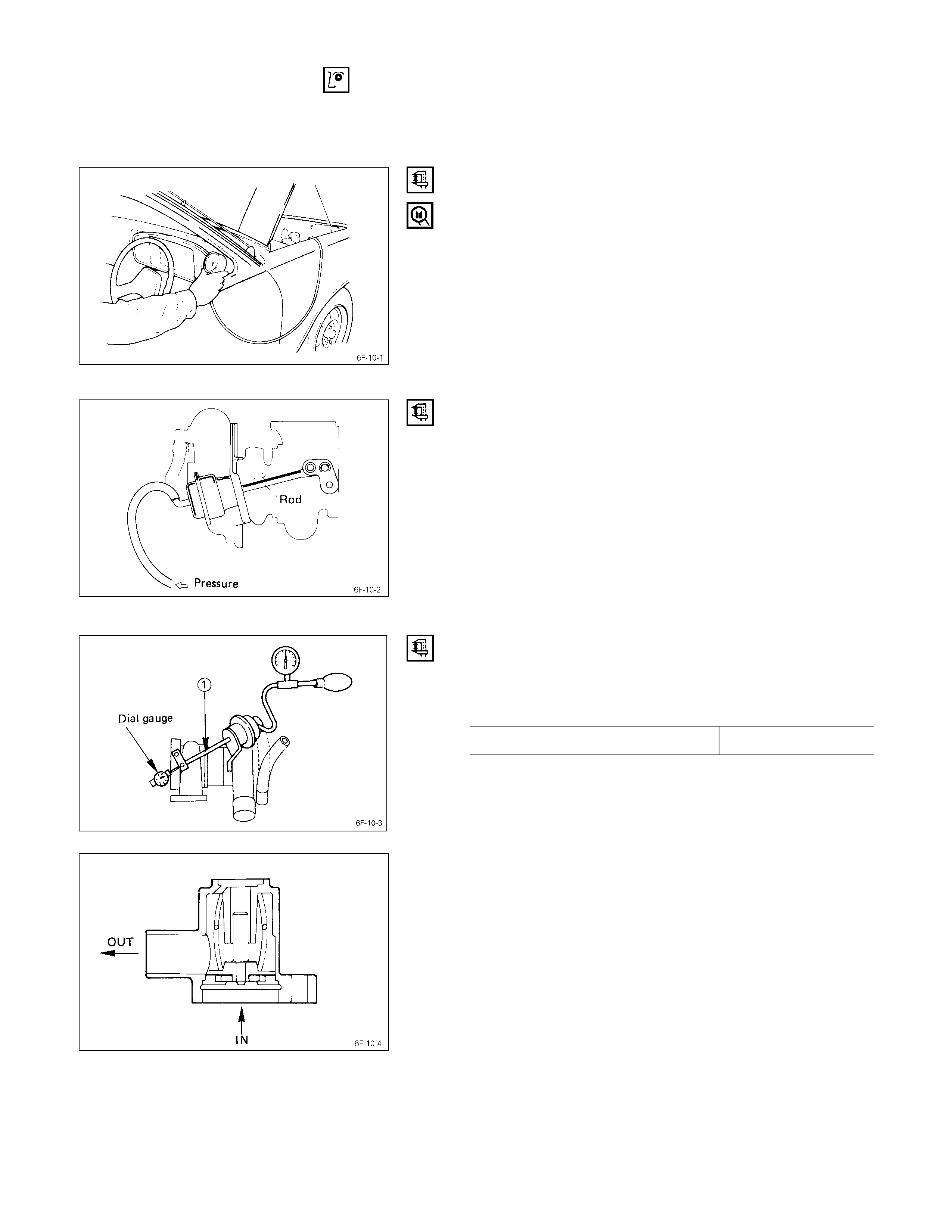
INSPECTION AND REPAIR
Make the necessary adjustments, repairs, and part replacements if excessive wear or damage is discovered during
inspection.
TURBOCHARGER PRESSURE CHECK
(1) Remove the pressure switch connecting hose from
intake duct.
(2) Connect the pressure gauge.
(3) Start the engine and gradually increase the engine
speed (the vehicle must be stationary with no load
applied to the engine).
(4) Check to see that turbocharger pressure rises to
approximately 300 mmHg.
Pressure Gauge : 5-8840-0075-0
WASTE GATE OPERATION CHECK
(1) Remove the hose between the waste gate and the
intake pipe.
(2) Connect the pressure gauge.
(3) Check to see that the rod begins to move when a
pressure of approximately 665 mmHg is applied to the
waste gate.
Note:
Do not apply a pressure greater than 1 kg/cm2 to the
wastegate during this check.
UNIT INSPECTION (REMOVE TURBO. FROM
ENGINE)
Check to see the pressure required to move the control
rod 2 mm is within the limits shown below.
Control Rod Operating Pressure Approx. 860 mmHg
SAFETY VALVE CHECK
Operate the valve with your hand to check its operation.
Check the valve seal are for excessive wear or damage.
Contact the “HOLDEN LIMITED” Dealer service
department or “IHI SERVICE FACILITY” for major repairs
and maintenance.
Important wheel shaft end play and bearing clearance
standards and limits are included below for your reference.