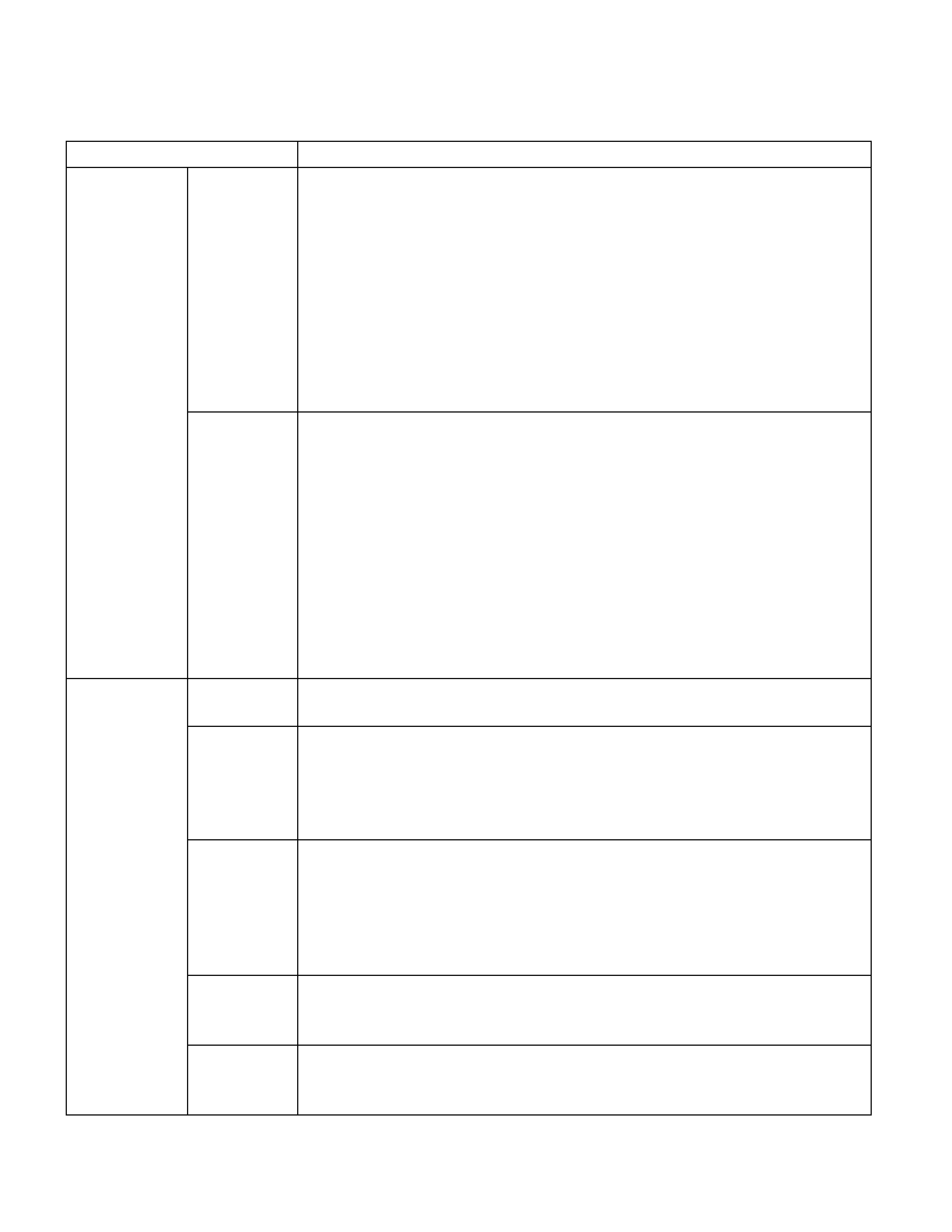
TROUBLESHOOTING
INSPECTION PRO CEDURES FOR STEERING SYSTEM
COMPONENT AND TEST PROCEDURE
HANDLE Check for
play and
slack
1. Place the steering wheel in the straight forward position. Gently move the
wheel to the right and to the left. About ten millimeters of play in either
direction should be present before the front tires begin to move.
If the vehicle is equipped with power steering, the engine should be running
when these tests are made.
2. Grasp the steering wheel firmly with both hands. Exert force in an up and
down direction on the steering column. There should be no play.
3. Move the steering wheel to the right and to the left. Check to see the
steering shaft.
Make sure that there is no slack in those areas where parts are joined
together.
Check the
operating
condition of
the system
1. Make the following checks while actually driving the vehicle.
a. Check the position of the steering wheel when the vehicle is traveling
straight ahead.
b. Make sure that the vehicle does not have a tendency to steer to the right
or the left.
c. There should be no excessive vibration present at the steering wheel.
d. Turn the vehicle as sharply as possible to both the right and the left.
When the steering wheel is turned fully in either direction, check for
abnormal noise.
Neither should the wheel feel overly heavy when it is fully turned to either
the left or the right. Loosen your grip on the steering wheel. It should
return to its center position.
GEAR BOX Check for
oil leakage 1. Check all parts of the steering unit (the oil seals of the front cover, side
cover, sector shaft, etc.) to make sure that there is no oil leakage.
Check for
looseness
in the
assembly
1. With the wheels of the vehicle on the ground (the vehicle should not be
jacked up), have an assistant or helper turn the steering wheel to the right
and to the left. As he does this, you should carefully check all areas where
the steering unit is attached to the frame for looseness and other possible
problems.
Check for
bearing
backlash
1. Check the condition of the connections between the steering shaft and the
bearings. Move the steering shaft in the direction of the axle and make sure
that there is no backlash present.
2. Rotate the steering shaft. There should be no abnormal noise. It should
rotate smoothly and there should be no feeling of roughness.
Check to make sure that there is no abnormal or excessive bearing wear.
Check for
gear
backlash
1. The front wheels should be facing straight ahead. Have an assistant or
helper grasp the drop arm so as to immobilize it. Now try to turn the steering
wheel. Backlash should not exceed one millimeter.
Inspect the
sector shaft
for c racks
1. Remove the steering unit from the vehicle and break it down into its
component parts. Carefully inspect the sector shaft for cracks or other
damage.