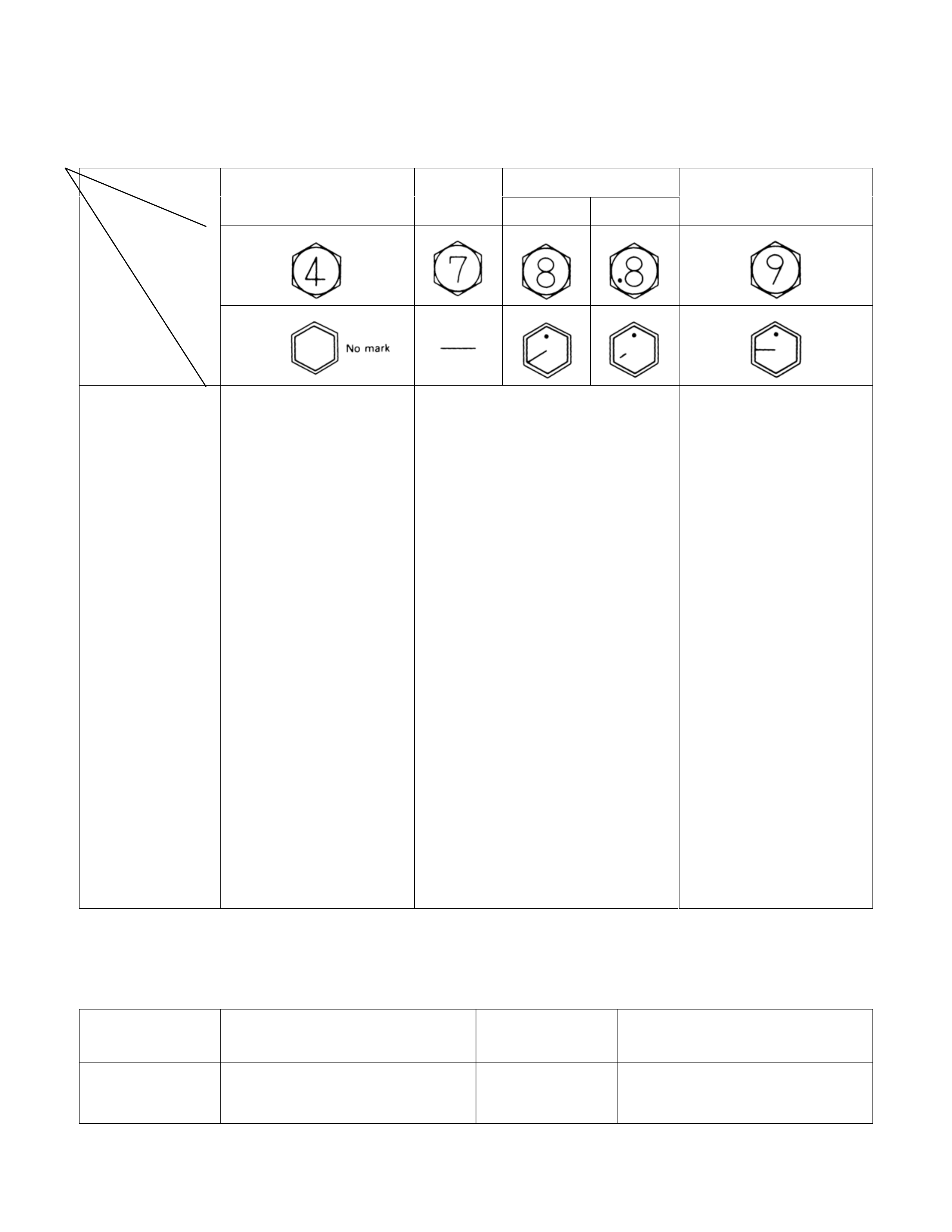
TORQUE SPECIFICATIONS
STANDARD BOLTS
The torque values given in the following table should be applied whenever a particular torque is not specified.
N·m (kg·m/lb·ft)
8.8
4.8 (4T) (7T) Refined Non-Refined 9.8 (9T)
Strength
Class
Bolt
Identification
Bolt
Diameter ×
Pitch (mm)
M 6 × 1.0
M 8 × 1.25
M 10 × 1.25
M 12 × 1.25
M 14 × 1.5
M 16 × 1.5
M 18 × 1.5
M 20 × 1.5
M 22 × 1.5
M 24 × 2.0
* M 10 × 1.5
* M 12 × 1.5
* M 14 × 2.0
* M 16 × 2.0
5.88 ± 1.96
(0.60 ± 0.20/4.33 ± 1.44)
12.74 ± 4.90
(1.30 ± 0.50/9.40 ± 3.62)
27.44 ± 6.86
(2.80 ± 0.70/20.25 ± 5.06)
61.25 ± 12.25
(6.25 ± 1.25/45.21 ± 9.04)
95.55 ± 19.11
(9.75 ±1.95/70.52 ± 14.10)
130.34 ± 26.46
(13.30 ± 2.70/96.20 ± 19.53)
188.16 ± 37.24
(19.20 ± 3.80/138.87 ± 27.49)
257.74 ± 51.94
(26.30 ± 5.30/190.23 ± 38.33)
332.22 ± 81.34
(33.90 ± 8.30/245.20 ± 60.03)
448.84 ± 90.16
(45.80 ± 9.20/331.27 ± 66.54)
26.46 ± 6.86
(2.70 ± 0.70/19.53 ± 5.06)
56.84 ± 11.76
(5.80 ± 1.20/41.95 ± 8.68)
89.18 ± 17.64
(9.10 ± 1.80/65.82 ± 13.02)
124.46 ± 24.50
(12.70 ± 2.50/91.86 ± 18.08)
7.35 ± 2.45
(0.75 ± 0.25/5.43 ± 1.80)
17.15 ± 5.39
(1.75 ± 0.55/12.66 ± 4.00)
36.75 ± 9.31
(3.75 ± 0.95/27.12 ± 6.87)
75.95 ± 15.19
(7.75 ± 1.55/56.06 ± 11.21)
116.13 ± 23.03
(11.85 ± 2.35/85.71 ± 17.00)
169.54 ± 34.30
(17.30 ± 3.50/125.13 ± 25.32)
244.02 ± 49.00
(24.90 ± 5.00/180.10 ± 36.17)
337.12 ± 67.62
(34.40 ± 6.90/248.82 ± 49.41)
453.25 ± 90.65
(46.25 ± 9.25/334.53 ± 66.91)
570.36 ± 140.14
(58.20 ± 14.30/420.96 ± 103.43)
36.26 ± 8.82
(3.70 ± 0.90/26.76 ± 6.50)
70.56 ± 13.72
(7.20 ± 1.40/52.08 ± 10.13)
109.76 ± 21.56
(11.20 ± 2.20/81.01 ± 15.91)
161.70 ± 32.34
(16.50 ± 3.30/119.34 ± 23.87)
-
23.52 ± 6.86
(2.40 ± 0.70/17.36 ± 5.06)
49.98 ± 12.74
(5.10 ± 1.30/36.89 ± 9.40)
94.57 ± 19.11
(9.65 ± 1.95/69.80 ± 14.10)
142.10 ± 28.42
(14.50 ± 2.90/104.88 ± 21.00)
199.92 ± 40.18
(20.40 ± 4.10/147.55 ± 29.66)
287.14 ± 57.82
(29.30 ± 5.90/211.93 ± 42.67)
395.92 ± 79.38
(40.40 ± 8.10/292.21 ± 58.59)
530.18 ± 105.84
(54.10 ± 10.80/391.30 ± 78.12)
691.88 ± 138.18
(70.60 ± 14.10/510.65 ± 101. 99)
48.02 ± 11.76
(4.90 ± 1.20/35.44 ±8.68)
89.18 ± 17.64
(9.10 ± 1.80/65.82 ± 13.02)
133.28 ± 26.46
(13.60 ± 2.70/98.37 ± 19.53)
191.10 ± 38.22
(19.50 ± 3.90/141.04 ± 28.21)
An asterisk (*) indicates that the bolts are used for female threaded parts that are made of soft materials such
as casting. Those shown in parentheses in the strength class indicate the classification by the old standard.
FLARE NUTS
N·m (kg·m/lb·ft)
Pipe diameter mm
(in) Torque Pipe diameter mm
(in) Torque
4.76 (0.187)
6.35 (0.250)
8.00 (0.315)
15.2 ± 2.45(1.55 ±0.25/11.2 ± 1.8)
26.48 ± 2.94(2.70 ± 0.30/19.5 ± 2.1)
44.14 ± 4.90(4.50 ± 0.50/32.5 ± 3.6)
10.00 (0.394)
12.00 (0.472)
15.00 (0.591)
53.95 ± 4.90(5.50 ± 0.5 /39.7 ± 3.6)
88.29 ± 9.80(9.00 ± 1.0/65.0 ± 7.2)
105.45 ± 12.26(10.75 ± 1.25/77.7 ± 9.0)