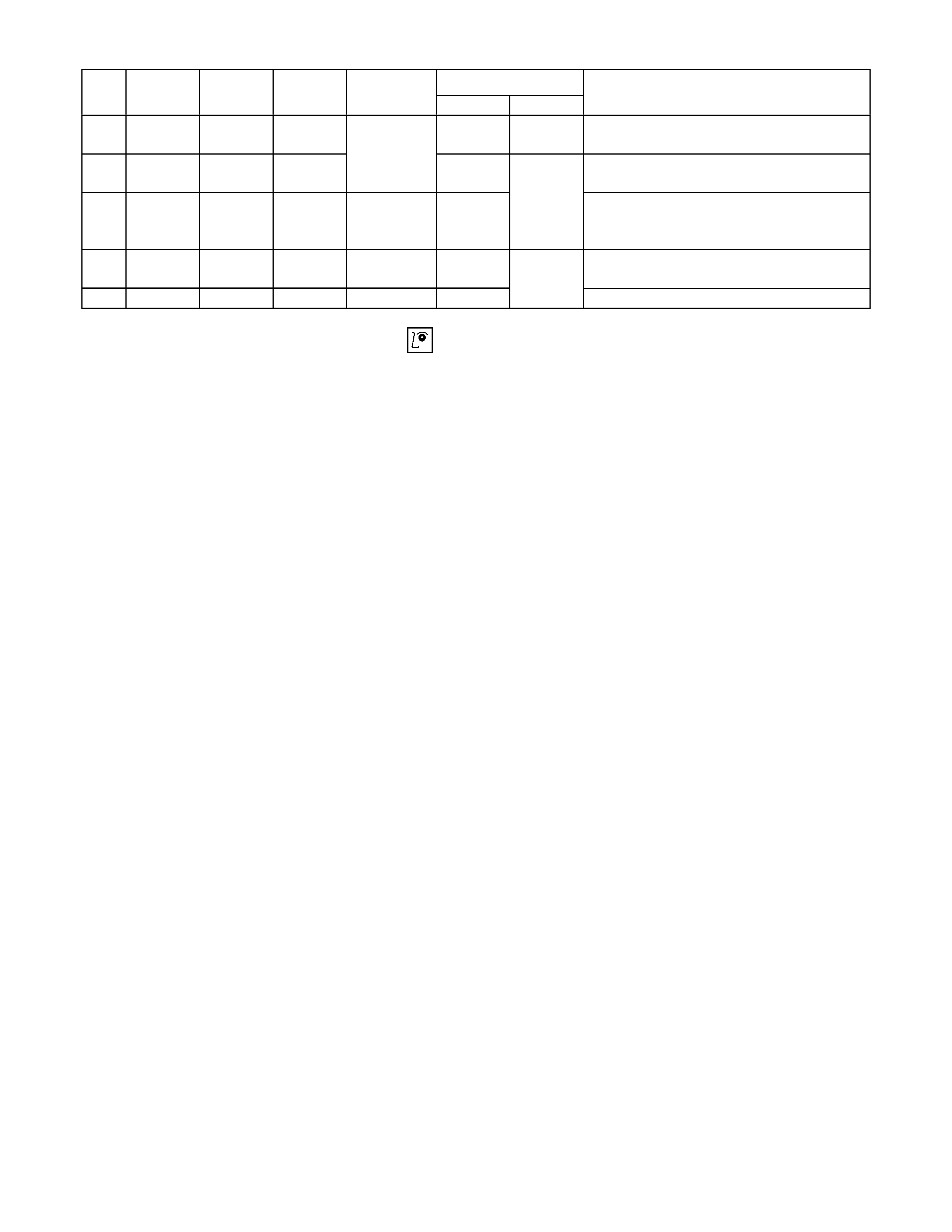
Judgment criteria
Lamp condition
No. Switch
1 Switch
2 Switch
3 Voltmeter
reading Lamp 1 Lamp 2 Remarks
1 ON OFF OFF On
(dim) ON Initial excitation check
2 ON ON OFF 12V On or
flashing Full excitation check
3 ON ON OFF 16V Off or
on (dim)
OFF Lamp 1 off or dimly lit when the
voltmeter shows less than 12 volts or
16 volts
4 OFF ON OFF 12V On or
flashing Stator and brush separation check
5 ON ON ON 18V On ON Excess voltage check
Oil seal
The oil seal must be replaced with a new one whenever
the alternator is disassembled.
Oil Seal Replacement
1. Push the old oil seal from the rear bracket outside
holes.
2. Use the insertion tool to press the new oil seal into
place. Follow the procedure shown in Figures A, B, C
and D.
Position the oil seal beneath the shaft and the
guide lip.
Position the cradle against the rear cover bosses
(3 points) so that the E1 and E2 surfaces fit into
the cradle. Take care not to damage the E1 and
E2 surfaces.
After completing the procedure, carefully check
the oil seal seating. Be absolutely sure that the
seal is evenly inserted (no warp) and level with the
surrounding surfaces.
CAUTION
• Be sure that no foreign material enters the
space between the oil seal and the rotor shaft
surfaces during the installation procedure.
• Take care not to damage the D surface.
• Under no circumstances may the original oil
seal be reused.
• The oil seal must be perfectly flat after being
pressed into place. If the oil seal is tilted, there
will be oil leakage.