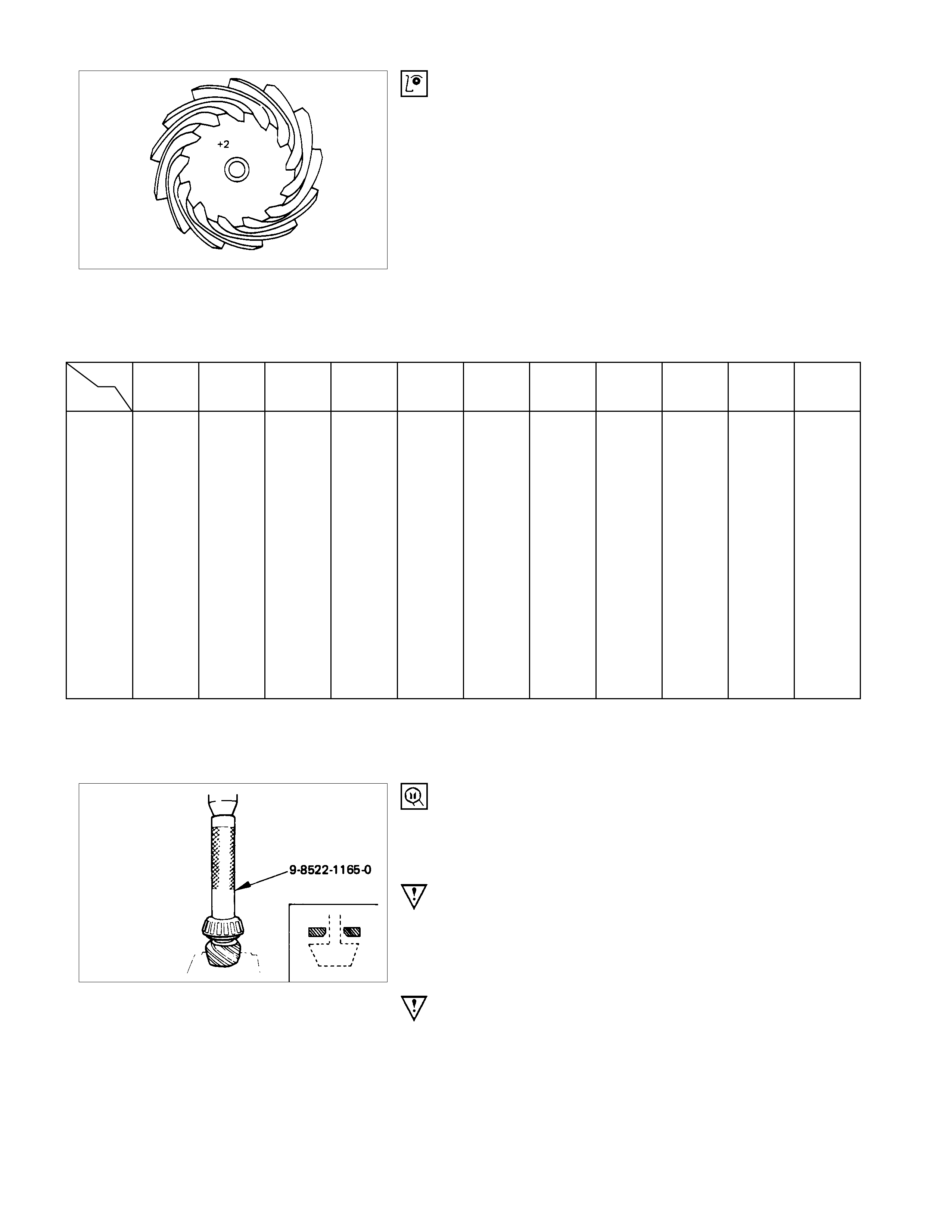
(6) Record the pinion depth code on the head of the drive
pinion.
The number indicates a necessary change in the pinion
mounting distanc e. A plus number indic ates the need for a
greater mounting distance (which can be achieved b
decreasing the s him thick ness). A m inus num ber indicates
the need for a smaller mounting distance (which can be
achieved by increasing the shim thickness). If examination
reveals pinion depth code “0”, the pinion is “nominal”.
(7) Select the shim using the chart;
mm(in)
Pinion
marking
+10 +8 +6 +4 +2 0 -2 -4 -6 -8 -10
Dial indica tor
reading (inches)
0.081 2.18 (0.0858)
0.082 2.18 (0.0858) 2.20 (0.0866)
0.083 2.18 (0.0858) 2.20 (0.0866) 2.24 (0.0882)
0.084 2.18 (0.0858) 2.20 (0.0866) 2.24 (0.0882) 2.26 (0.0890)
0.085 2.18 (0.0858) 2.20 (0.0866) 2.24 (0.0882) 2.26 (0.0890) 2.28 (0.0898)
0.086 2.18 (0.0858) 2.20 (0.0866) 2.24 (0.0882) 2.26 (0.0890) 2.28 (0.0898) 2.32 (0.0914)
0.087 2.18 (0.0858) 2.20 (0.0866) 2.24 (0.0882) 2.26 (0.0890) 2.28 (0.0898) 2.32 (0.0914) 2.34 (0.0921)
0.088 2.18 (0.0858) 2.20 (0.0866) 2.24 (0.0882) 2.26 (0.0890) 2.28 (0.0898) 2.32 (0.0914) 2.34 (0.0921) 2.36 (0.0929)
0.089 2.18 (0.0858) 2.20 (0.0866) 2.24 (0.0882) 2.26 (0.0890) 2.28 (0.0898) 2.32 (0.0914) 2.34 (0.0921) 2.36 (0.0929) 2.38 (0.0937)
0.090 2.18 (0.0858) 2.20 (0.0866) 2.24 (0.0882) 2.26 (0.0890) 2.28 (0.0898) 2.32 (0.0914) 2.34 (0.0921) 2.36 (0.0929) 2.38 (0.0937) 2.42 (0.0953)
0.091 2.18 (0.0858) 2.20 (0.0866) 2.24 (0.0882) 2.26 (0.0890) 2.28 (0.0898) 2.32 (0.0914) 2.34 (0.0921) 2.36 (0.0929) 2.38 (0.0937) 2.42 (0.0953) 2.44 (0.0961)
0.092 2.20 (0.0866) 2.24 (0.0882) 2.26 (0.0890) 2.28 (0.0898) 2.32 (0.0914) 2.34 (0.0921) 2.36 (0.0929) 2.38 (0.0937) 2.42 (0.0953) 2.44 (0.0961) 2.46 (0.0969)
0.093 2.24 (0.0882) 2.26 (0.0890) 2.28 (0.0898) 2.32 (0.0914) 2.34 (0.0921) 2.36 (0.0929) 2.38 (0.0937) 2.42 (0.0953) 2.44 (0.0961) 2.46 (0.0969) 2.48 (0.0977)
0.094 2.26 (0.0890) 2.28 (0.0898) 2.32 (0.0914) 2.34 (0.0921) 2.36 (0.0929) 2.38 (0.0937) 2.42 (0.0953) 2.44 (0.0961) 2.46 (0.0969) 2.48 (0.0977) 2.52 (0.0992)
0.095 2.28 (0.0898) 2.32 (0.0914) 2.34 (0.0921) 2.36 (0.0929) 2.38 (0.0937) 2.42 (0.0953) 2.44 (0.0961) 2.46 (0.0969) 2.48 (0.0977) 2.52 (0.0992) 2.54 (0.1000)
0.096 2.32 (0.0914) 2.34 (0.0921) 2.36 (0.0929) 2.38 (0.0937) 2.42 (0.0953) 2.44 (0.0961) 2.46 (0.0969) 2.48 (0.0977) 2.52 (0.0992) 2.54 (0.1000) 2.56 (0.1008)
0.097 2.34 (0.0921) 2.36 (0.0929) 2.38 (0.0937) 2.42 (0.0953) 2.44 (0.0961) 2.46 (0.0969) 2.48 (0.0977) 2.52 (0.0992) 2.54 (0.1000) 2.56 (0.1008)
0.098 2.36 (0.0929) 2.38 (0.0937) 2.42 (0.0953) 2.44 (0.0961) 2.46 (0.0969) 2.48 (0.0977) 2.52 (0.0992) 2.54 (0.1000) 2.56 (0.1008)
0.099 2.38 (0.0937) 2.42 (0.0953) 2.44 (0.0961) 2.46 (0.0969) 2.48 (0.0977) 2.52 (0.0992) 2.54 (0.1000) 2.56 (0.1008)
0 2.42 (0.0953) 2.44 (0.0961) 2.46 (0.0969) 2.48 (0.0977) 2.52 (0.0992) 2.54 (0.1000) 2.56 (0.1008)
0.001 2.44 (0.0961) 2.46 (0.0969) 2.48 (0.0977) 2.52 (0.0992) 2.54 (0.1000) 2.56 (0.1008)
0.002 2.46 (0.0969) 2.48 (0.0977) 2.52 (0.0992) 2.54 (0.1000) 2.56 (0.1008)
0.003 2.48 (0.0977) 2.52 (0.0992) 2.54 (0.1000) 2.56 (0.1008)
0.004 2.52 (0.0992) 2.54 (0.1000) 2.56 (0.1008)
0.005 2.54 (0.1000) 2.56 (0.1008)
0.006 2.56 (0.1008)
Note:
When ordering shims, find the part number in the Parts Catalog by using the thickness of the shims listed in
the above table.
5. Inner Bearing
Place the shim on the drive pinion, with the chamfered side
turned towards the pinion head then install the inner bearing on
to the pinion using an installer and a press.
Installer : 9-8522-1165-0 (J-6133-01)
Note:
Do not apply pressure to the roller cage.
Apply pressure only to the inner race.
6. Collapsible Spacer
Discard the used collapsible spacer and install a new one.