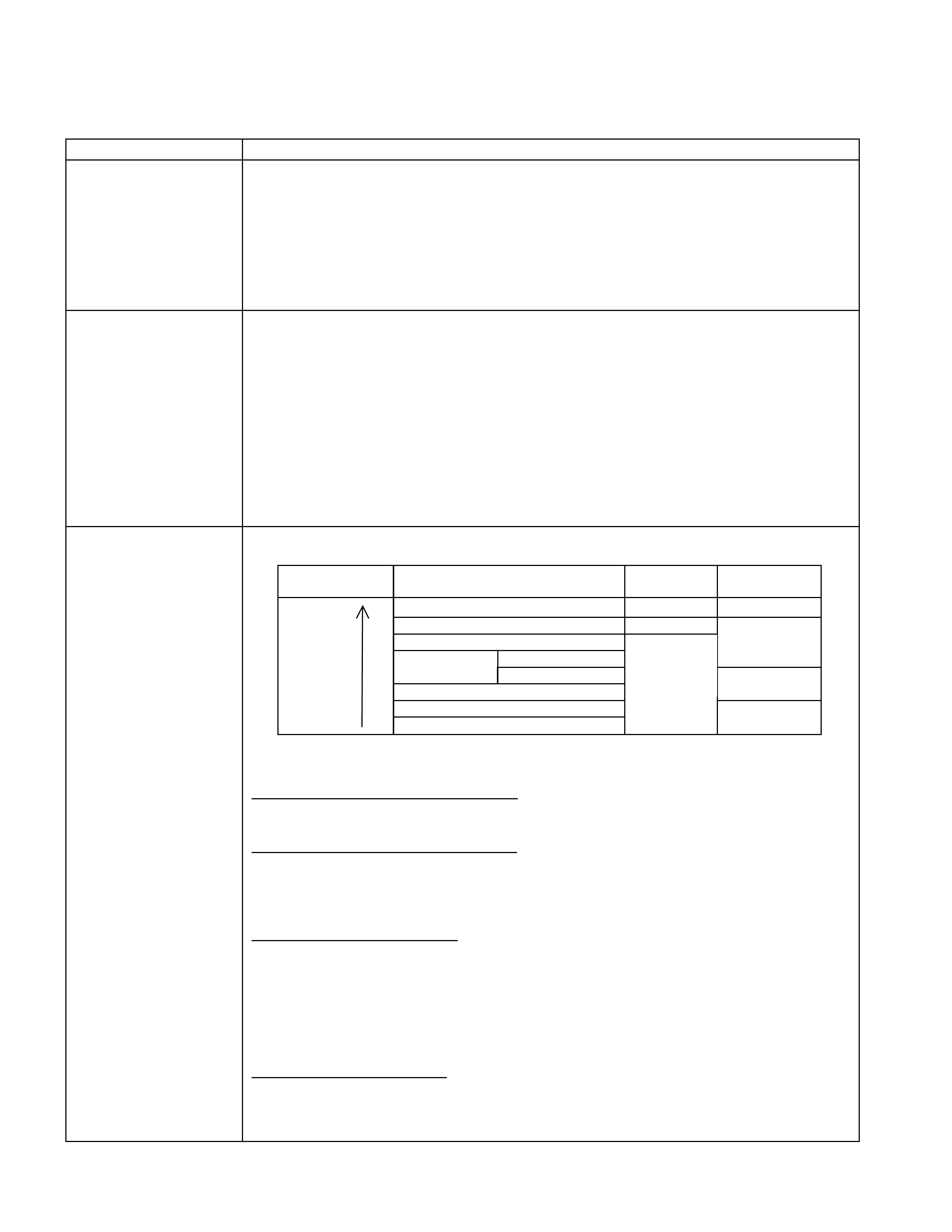
Control Mechanism
Content Of Function And Control
Item Description
Line pressure control TCM issues a signal according to the vehicle traveling, engine load and other conditions to
TCM and the ON/OFF type line pressure solenoid is driven to switch the line pressure to
high or low pressure.
The line pressure solenoid is switc hed to the low pressure s ide when the solenoid is turned
ON (power supplied) and to the high pressure side when turned OFF (no power supplied).
In the forward travel range (D, 3, 2, L range), the line pres sure dec reases lower than that in
the P, N, and R range through the oil pressure circuit for the forward travel range.
Gear shift control The TCM issues a shift solenoid drive signal based on the traveling mode switch, inhibitor
switch, vehicle speed, throttle opening and other input signal to control the optimum gear
position automatically.
Speed change features have been set up to the TCM; the normal mode is suited to usual
traveling and the power mode is appropriate when the vehicle is loaded or acc elerates the
speed.
In addition, speed change features used only for high oil temperature, hill climbing, and
down have been set up to the TCM, which are automatically switched depending on the
traveling conditions.
When the oil temperature is low (below 10°C), speed change from the third to the fourth
speed is prohibited by the gear shift control.
Shift pattern selection
control According to a vehicle condition, the TCM selects the following shift pattern.
Selection
Priority Shift Pattern 3rd Start
Lamp Power Drive
Lamp
High High Temperature OFF OFF
3rd Start ON
4L
Power SW Off
OFF
Down Slop Power SW On
Power ON
Up Slope
Low Normal
OFF
OFF
- High temperature mode -
High temperature mode setting condition
ATF temperature: More than 123°C
Above condition is met for more than 10 seconds.
High temperature mode cancel condition
ATF temperature: Less than 116°C
Above condition is met for more than 10 seconds.
- 3rd start mode -
3rd start mode setting condition
3rd start switch: On → Off (Pushed)
Vehicle speed: Less than 11km/h
ATF temperature: Less than 115°C
Throttle position: Less than 8%
Select lever position: D range
Above conditions are met at the same time.
3rd start mode reset condition
3rd start switch: On → Off again(Pushed again)
Vehicle speed: More than 34km/h
Select lever position: Other than D range