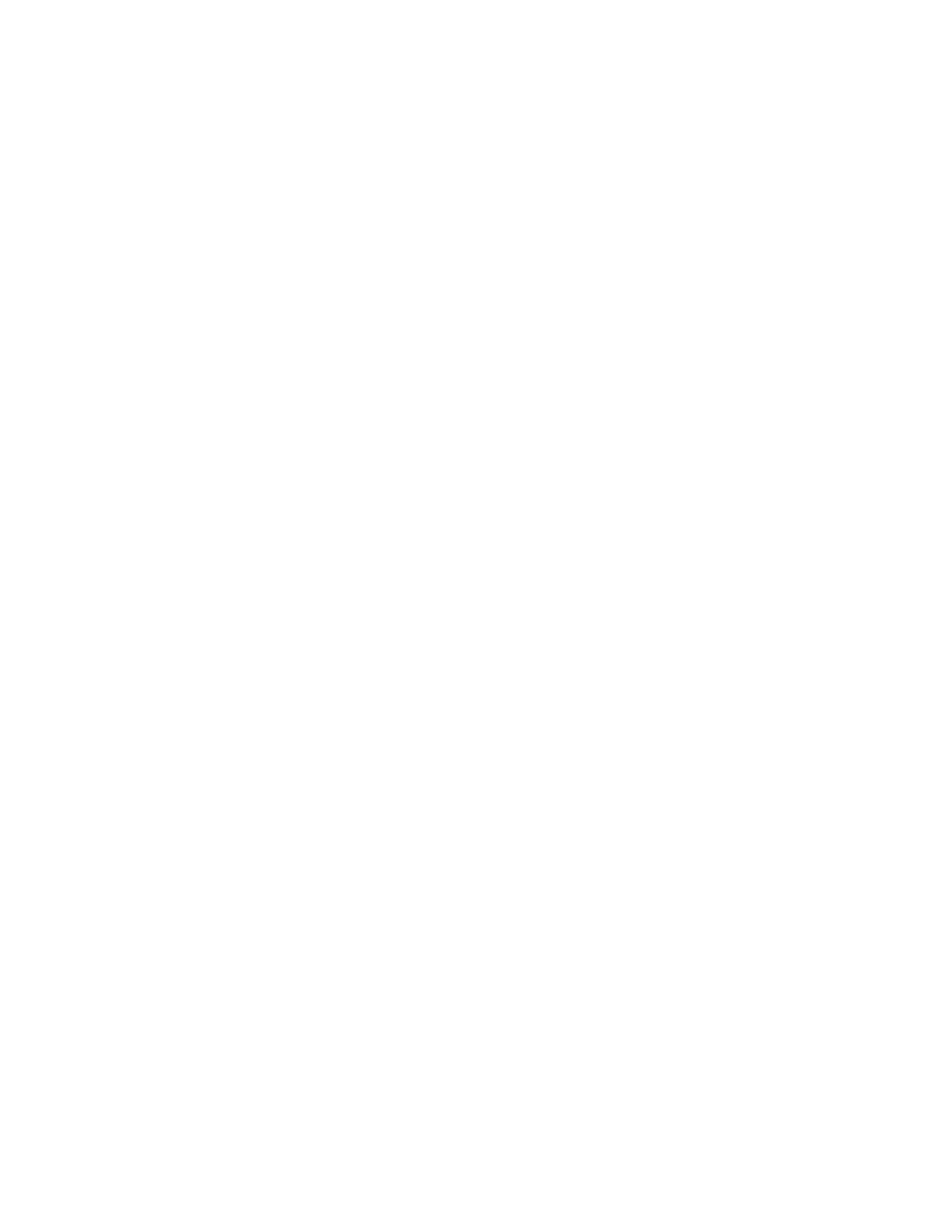
Clear DTC
NOTE: If you clear the DTC (Diagnostic Trouble
Codes) you will not be able to read any codes recorded
during the last occurrence.
NOTE: To use the DTC again to identify a problem,
you will need to reproduce the fault or the problem.
This may require a new test drive or just turning the
ignition on (this depends on the nature of the fault).
1. IF you have a Tech 2:
1. Connect the Tech 2 if it is still not connected go
through Tech 2 OBD CONNECTION.
2. Push “F1: Clear DTC Information" in the
Application Menu and answer “Yes" to the
question “Do you want to clear DTC's?"
a. When a malfunction still exists and the Tech
2 displays “AW30-40 CODES NOT
CLEARED". This means that the problem is
still there or that the recovery was not done.
Please go to DTC CHECK.
b. When a malfunction has been repaired and
the recovery is done the Tech 2 displays
“AW30-40LE CODES CLEARED".
2.When you have no Tech 2, the stored trouble codes
can be cleared by shorting the terminals No.11 and
No.4 or 5 (ground) of data link connector with a lead
wire for 1 6 seconds.
DTC Check
1. Diagnostic Trouble Codes (DTC) have been
identified by Tech 2.
2. You have written the list of the DTCs. The order of
the malfunctions has no meanings for this TCM.
Usually only one or two malfunctions should be set
for a given problem.
3. Check directly the DTCs you identified. The DTCs
are sorted by number. Refer to Diagnostic Trouble
Code (DTC) Identification in this section.
TCM Precaution
The TCM can be damaged by:
1. The electrostatic discharge
2. The short circuit of some terminals to voltage or to
ground.
Electrostatic Discharge Damage Description:
1. Electronic components used to control systems
are often designed to carry very low voltage, and
are very susceptible to damage caused b
electrostatic discharge. It is possible for less than
100 volts of static electricity to cause damage to
some electronic components. By comparison, it
takes as much as 4,000 volts for a pers on to even
feel the zap of a static discharge.
2. There are several ways for a person to become
statically charged. The most common methods o
charging are by friction and induction. An exam ple
of charging by friction is a person sliding across a
car seat, in which a charge of as much as 25,000
volts can build up. Charging by induction occurs
when a person with well insulated shoes stands
near a highly charged object and momentaril
touches ground. Charges f or the sam e polarity are
drained of f, leaving the person highly charged with
the opposite polarity. Static charges of either type
can cause damage, therefore, it is important to use
care when handling and testing electronic
components.
NOTE: To prevent possible electrostatic discharge
damage:
1. Do not touch the TCM connector pins or soldered
components on the TCM circuit board.
2. Be sure to follow the guidelines listed below if
servicing any of these electronic components:
3. Do not open the replacement part package until it is
time to install the part.
4. Avoid touching electrical terminals of the part.
5. Before removing the part from its package, ground
the package to a known good ground on the
vehicle.
6.
lways touch a known good ground before handling
the part. This step should be repeated before
installing the part if the part has been handled while
sliding across the seat, while sitting down from a
standing position or while walking some distance.
Information On TCM
1. The Transmission Control Module (TCM) is located
in the place of a clutch pedal and is the control
centre of the electronic transmission control system.
2. The TCM must be maintained at a temperature
below 85°C (185°F) at all times. This is most
essential if the vehicle is put through a paint baking
process. The TCM will become inoperative if its
temperature exceeds 85°C (185°F). Therefore, it is
recommended that the TCM be removed or that
temporary insulation be placed around the TCM
during the time the vehicle is in a paint oven or other
high temperature process.
3. The TCM is designed to process the various inputs
and then respond by sending the appropriate
electrical signals to control transmission upshift,
downshift, shift feel and torque converter clutch
engagement.
4. The TCM constantly interprets information from the
various sensors, and controls the systems that
affect transmission and vehicle performance. By
analysing operational problems, the TCM is able to
perform a diagnostic function by displaying DTC(s)
and aid the technician in making repairs.