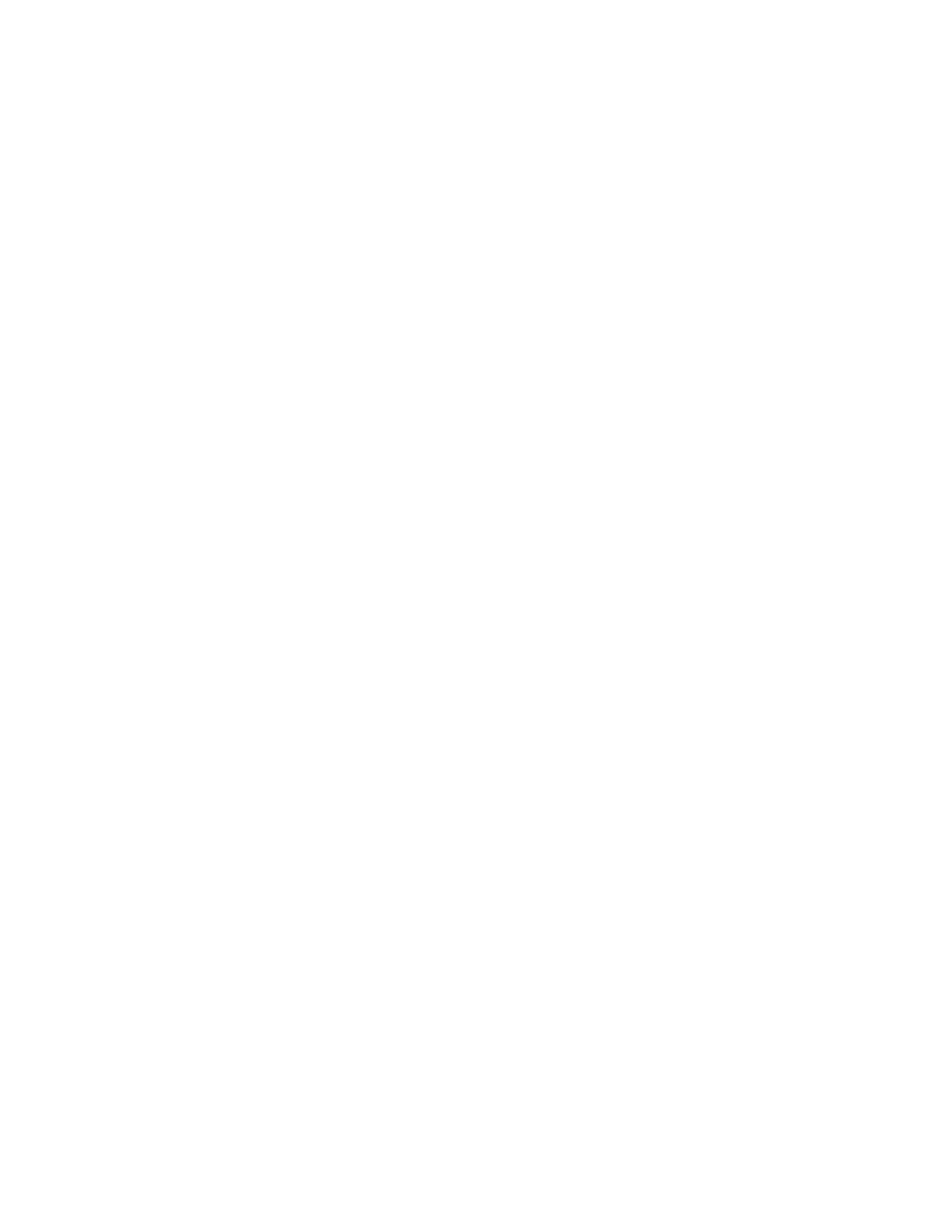
SECTION 7A2 - DIAGNOSIS (JR405E)
Basic Trouble Shooting
Check Trans Indicator & Self Diagnosis
Diagnosis With Tech 2
Tech 2 Operating Flow Chart (Start Up)
Miscellaneous Test
Intermittent Diagnosis
Snapshot Display With TIS 2000
Circuit Diagram
Part Location
Connector List
Diagnosis Trouble Code Table
Fail-Safe Function
DTC P0722 (Flash Code 11) Output Shaft Sensor
No Signal
DTC P0727 (Flash Code 13) Engine Revolution
Sensor No Signal
DTC P0717 (Flash Code 14) Turbine Speed Sensor
No Signal
DTC P0710 (Flash Code 15) Atf Temperature Sensor
Failure
DTC P0560 (Flash Code 16) System Voltage Failure
DTC P0705 (Flash Code 17) Inhibitor Switch Failure
DTC P1120 (Flash Code 22) Throttle Signal Failure
DTC P1875 (Flash Code 25) Gnd Return Circuit
Failure
DTC P0753 (Flash Code 31) Low & Reverse Brake
Duty Solenoid Failure
DTC P0758 (Flash Code 32) 2-4 Brake Duty
Solenoid Failure
DTC P0763 (Flash Code 33) High Clutch Duty
Solenoid Failure
DTC P0768 (Flash Code 34) Low Clutch Duty
Solenoid Failure
DTC P0748 (Flash Code 35) Line Pressure Solenoid
Failure
DTC P1860 (Flash Code 36) Lock-Up Duty Solenoid
Failure
DTC P1853 (Flash Code 26) Low & Reverse Brake
Pressure Switch Failure
DTC P1858 (Flash Code 27) 2-4 Brake Pressure
Switch Failure
DTC P1863 (Flash Code 28) High Clutch Pressure
Switch Failure
DTC P0731 (Flash Code 41) 1st Gear Ratio Error
DTC P0732 (Flash Code 42) 2nd Gear Ratio Error
DTC P0733 (Flash Code 43) 3rd Gear Ratio Error
DTC P0734 (Flash Code 44) 4th Gear Ratio Error
DTC P1750 (Flash Code 51) Low & Reverse Brake
Fail-Safe Valve Failure
DTC P1755 (Flash Code 52) 2-4 Brake Fail-Safe
Valve Failure
DTC P0602 Programming Error
Symptom Diagnosis
No. A1: Vehicle Does Not Run In D, 3, 2, L And
Range
No. A2: Vehicle Does Not Run In R Range
No. A3: Vehicle Does Not Run In D, 3, 2 And Range
No. B1: Vehicle Runs In N Range
No. B2: Poor Acceleration At Starting
No. B3: Engine Race Up During Starting (Slip)
No. B4: Large Shock When Shift Lever Is Changed
To N To D Range Or N To R Range
No. B5: Engine Stalls When Selecting From N
Range To R, D, 3, 2 Or L Range
No. B6: Engine Starter Does Not Run In P Or N
Range
No. B7: Engine Starter Runs Except In P Or N
Range
No. B8: Extended Time Lag When Shift Lever Is
Changed To N To D
No. B9: Extended Time Lag When Shift Lever Is
Changed To N To R
No. B10: Brake Is Applied In R Range
No. B11: Insufficient Starting Or Shaking In D
Range
No. B12: Noise Or Vibration Is Generated At
Starting
No. C1: Engine Race Up (Slip) When Gear Is Shifted
Up To 1st To 2
nd
No. C2: Engine Race Up (Slip) When Gear Is
Shifted Up To 2nd To 3
rd
No. C3: Engine Race Up (Slip) When Gear Is
Shifted Up To 3rd To 4
th
No. C4: Engine Race Up (Slip) When Gear Is Shift
Down Or Kick-Down To 4th To 3
rd
No. C5: Engine Race Up (Slip) When Gear Is Shift
Down Or Kick-Down To 4th To 2
nd
No. C6: Engine Race Up (Slip) When Gear Is Shift
Down Or Kick-Down To 3rd To 2
nd
No. C7: Engine Race Up (Slip) When Gear Is Shift
Down To 4th Or 3
rd
To 1
st
No. C8: Engine Race Up (Slip) Others