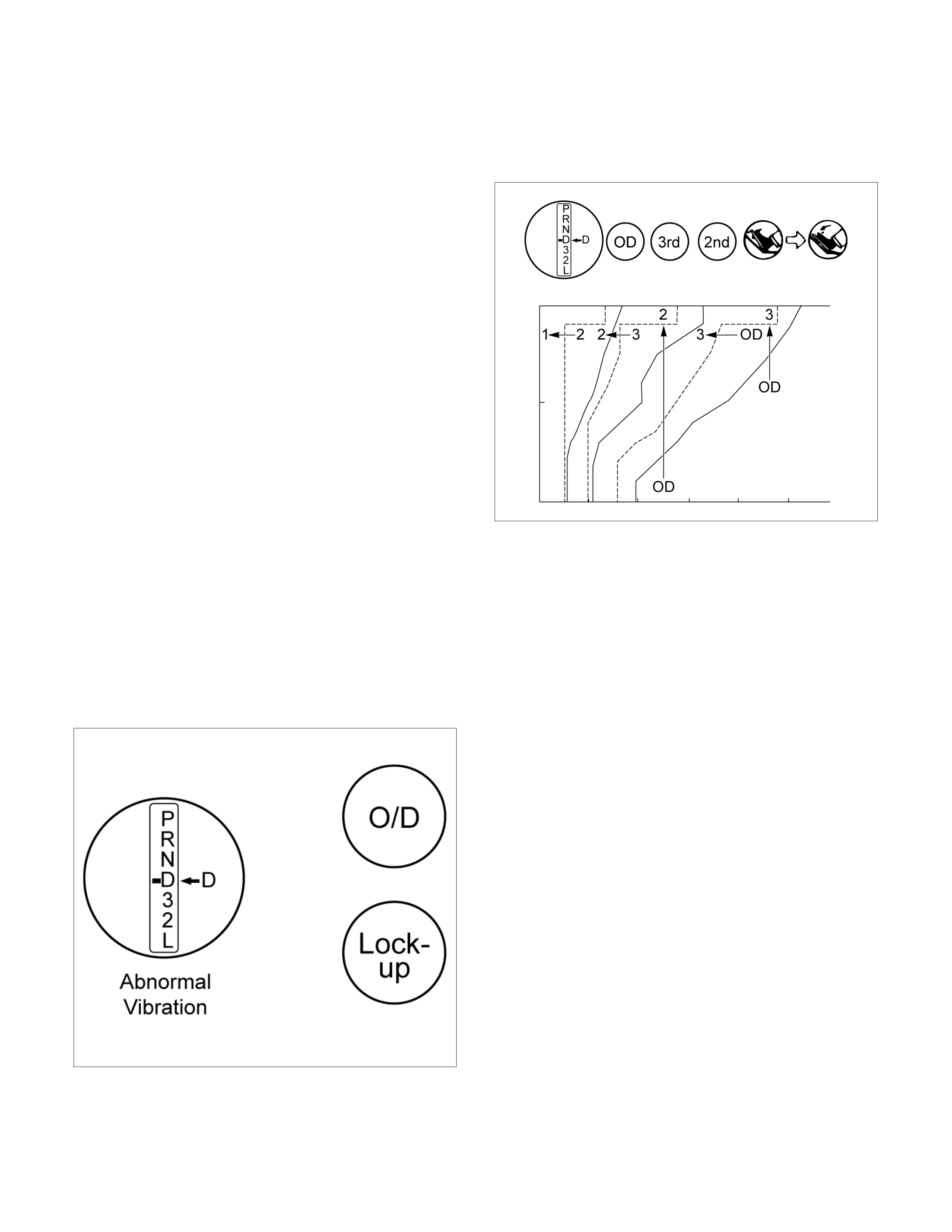
Evaluation
i. If there is no 1→2 up-shift:
• Solenoid S2 is stuck
• 1–2 shift valve is stuck
ii. If there is no 2→3 up-shift:
• Solenoid S1 is stuck
• 2–3 shift valve is stuck
iii. If there is no 3→OD up-shift (throttle valve opening
1/2):
• Solenoid S2 is stuck
• 3–OD shift valve is stuck
iv. If the shift point is defective:
Refer to TROUBLESHOOTING CHART in this
section.
v. If the lock-up is defective:
Refer to TROUBLESHOOTING CHART in this
section.
2. In the same manner, check the shock and slip at the
1→2, 2→3 and 3→OD up-shifts.
NOTE: Drive the vehicle on level ground.
Evaluation
If the shock is excessive:
Refer to TROUBLESHOOTING CHART in this section.
3. Run at “D" range lock-up or OD gear and check for
abnormal noise and vibration.
NOTE: The check for the cause of abnormal noise and
vibration must be made with extreme care as it could
also be due to loss of balance in the propeller shaft,
differential, the torque converter, etc. or insufficient
bending, rigidity , etc. in the power train.
RUW37ASH000201
4. While running in “D" range, 2nd, 3rd gears and OD,
check to see that the possible kick-down vehicle
speed limits for 2→1, 3→1, 3→2, OD→3 and
OD→2 kick-downs conform to those indicated on
the automatic shift diagram.
RUW37AMH000101
5. Check for abnormal shock and slip at kick-down.
6. While running in “D" range, OD gear or “lock-up",
shift to “2" and “L" ranges and check the engine
braking effect at each of these ranges.
7. Also check to see that downshift is made from 3→2
or from OD to 3 and then to 2 immediately and that
2→1 downshift point is within the limits shown in the
diagram when tested by releasing the accelerator
pedal and shifting into position of “L" while driving in
the third gear or in overdrive.