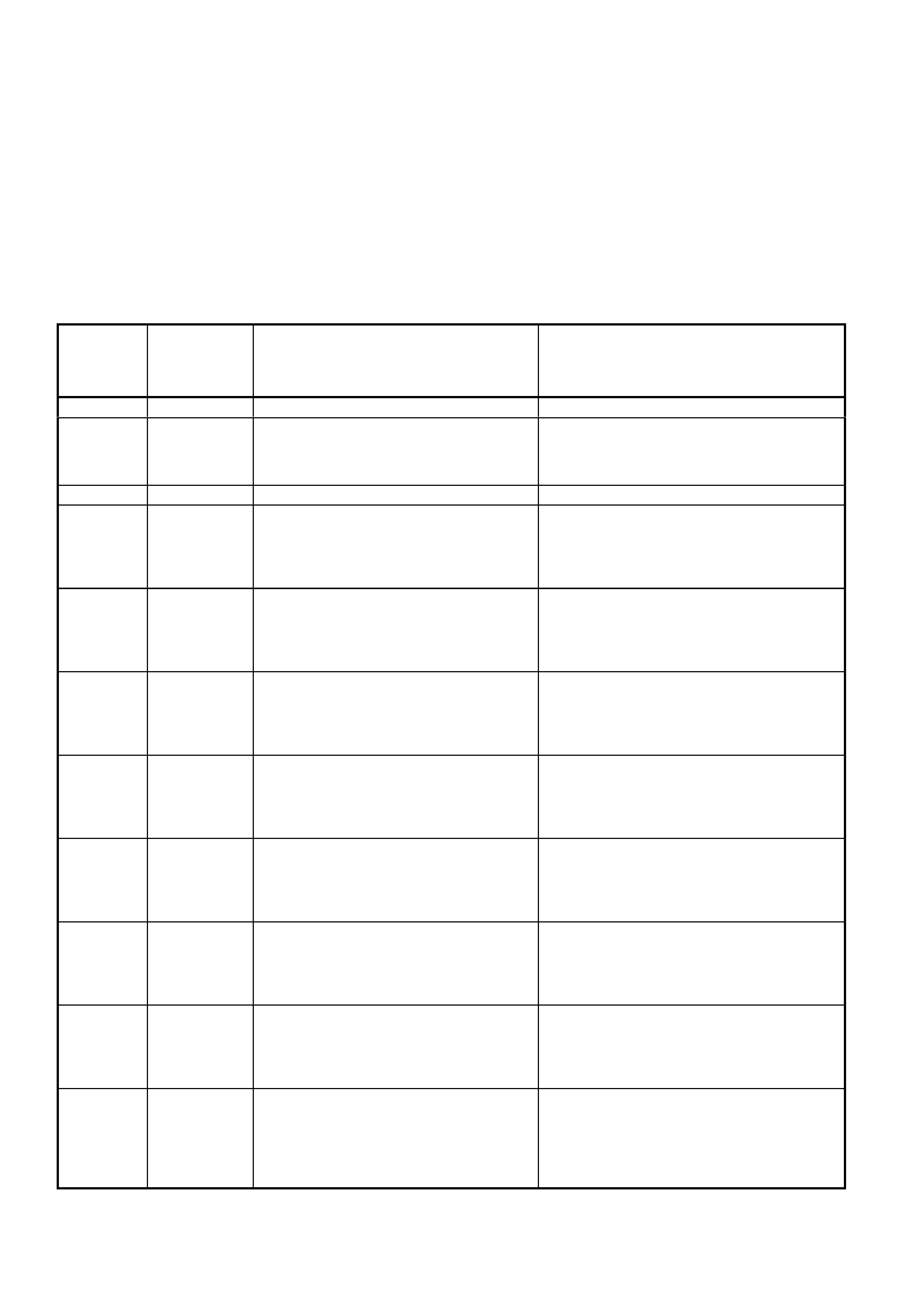
REQUESTING THE NEXT DIAGNOSTIC TEST CODE
The s eat will continue to issue the cur rent DT C until the operator r equests the nex t code. T o request the next code,
press and release the M2 button. On each new code to be flashed, the MSC module will issue a high chime. The
seat will continue in the diagnostic loop, f lashing out all the active c odes as requested by the operator until the final
test code (6–6) is f ound. At this point, pres sing the M2 button will caus e the seat to cycle back to the start and begin
flashing out the ac tive DT C. The DTCs ar e updated at the end of eac h test loop, i.e once c ode 6–6 is found and any
previously displayed DT C that has been r ectified or no longer exis ts will be deleted. Acc or dingly, an intermittent fault
may be detec ted on one test loop, but deleted on the next test loop. If there are no ac tive errors, the LED will stop
flashing out DT Cs and the LED will rem ain on. If there are no ac tive errors, then any new errors induced will not be
detected, the operator must therefore restart the DTC tests.
To exit the diagnostic mode, cycle the ignition to OFF.
DIAGNOSTIC TEST CODES – MEMORY TYPE SEAT
The first code issued at the beginning of the diagnostic test code loop identifies the type of seat under test.
HIGH
VALUE
(First flash
group)
LOW VALUE
(Second
flash group)
CODE DESCRIPTION CORRECTIVE ACTION
1 1 Ez-entry type seat None required.
1 4 No occupant sensing mat detected Faulty wiring or occupant sensing mat. Go to
the Occupant Sensing Mat Test, refer to
3.6 GENERAL DIAGNOSTIC CHARTS –
MEMORY TYPE SEAT in this Section.
1 5 Occupant sensing mat detected weight None required.
2 1 No priority 1 Assert a priority 1 code using the Priority
Key 1 and verify that the code clears. If not,
go to the Priority Signal Lines Test, refer to
3.6 GENERAL DIAGNOSTIC CHARTS –
MEMORY TYPE SEAT in this Section.
2 2 No priority 2 Assert a priority 2 code using the Priority
Key 2 and verify that the code clears. If not,
go to the Priority Signal Lines Test, refer to
3.6 GENERAL DIAGNOSTIC CHARTS –
MEMORY TYPE SEAT in this Section.
2 5 No ignition Ensure that the ignition is on and verify that
the code clears. If not, check for an open
circuit in the ignition signal line between the
ignition switch and the memory seat control
module.
3 1 No front lift motor sensor Faulty wiring or front lift motor sensor. Go to
Front Lift Motor Position Sensor Potentiometer
Test, refer to 3.6 GENERAL DIAGNOSTIC
CHARTS – MEMORY TYPE SEAT in this
Section.
3 2 No rear lift motor sensor Faulty wiring or rear lift motor sensor. Go to
Rear Lift Motor Position Sensor Potentiometer
Test, refer to 3.6 GENERAL DIAGNOSTIC
CHARTS – MEMORY TYPE SEAT in this
Section.
3 3 No track motor sensor Faulty wiring or track motor sensor. Go to
Track Motor Position Sensor Potentiometer
Test, refer to 3.6 GENERAL DIAGNOSTIC
CHARTS – MEMORY TYPE SEAT in this
Section.
3 4 No recliner motor sensor Faulty wiring or recliner motor sensor. Go to
Recliner Motor Position Sensor Potentiometer
Test, refer to 3.6 GENERAL DIAGNOSTIC
CHARTS – MEMORY TYPE SEAT in this
Section.
4 1 Forward lift motor stalled Move the forward lift switch in the opposing
direction. If the seat fails to move in either
direction, go to Seat Front Up and/or Down
Function Inoperative, refer to 3.6 GENERAL
DIAGNOSTIC CHARTS – MEMORY TYPE
SEAT in this Section.