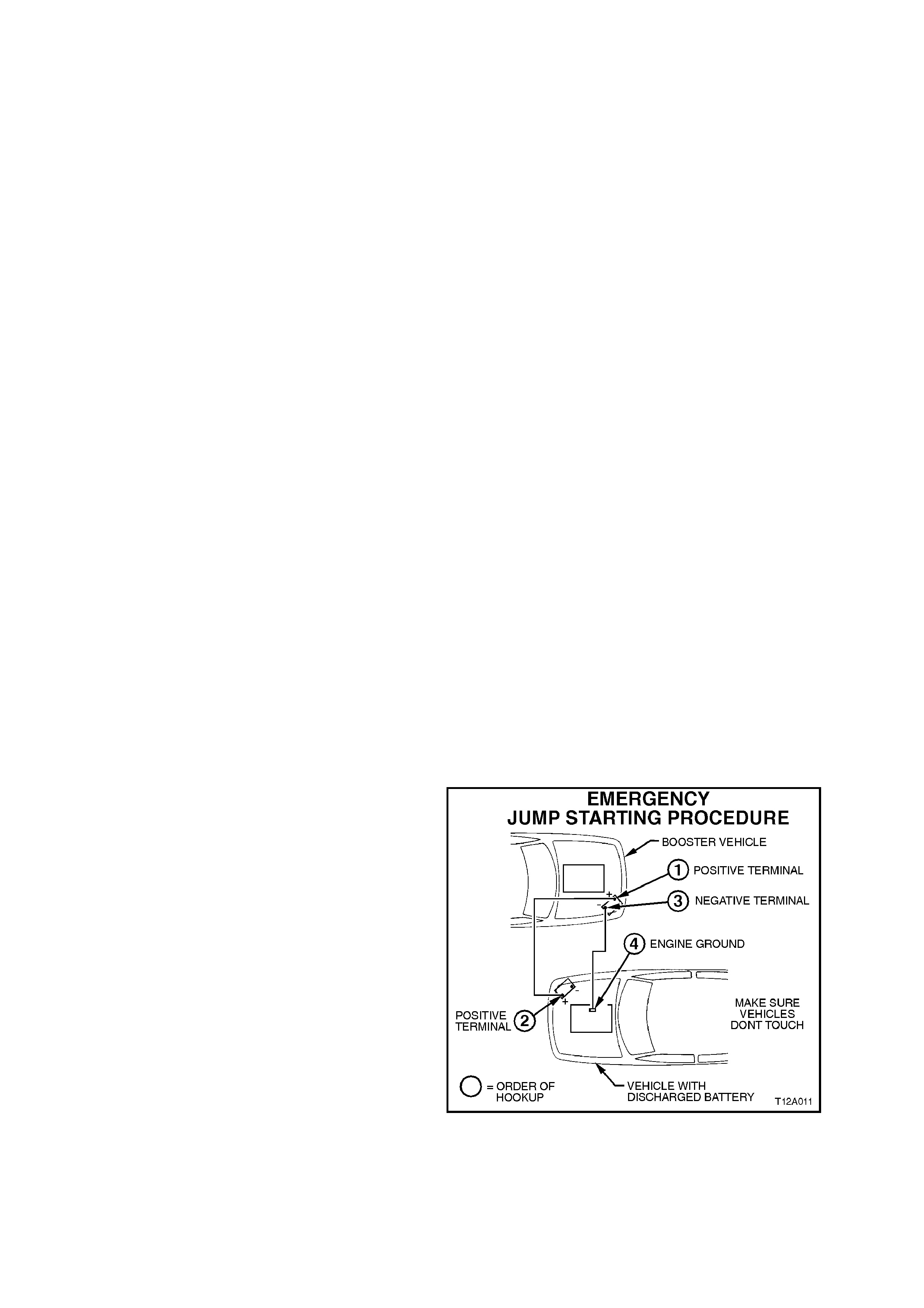
2.9 EMERGENCY JUMP STARTING PROCEDURE
NOTE:
DO NOT attempt to pus h or tow the vehicle to start
it. Damage to the catalytic converter could result if
unburnt fuel were to reach the converter and
ignited.
Do not use a fast charger f or attem pting to s tart the
vehicle.
Both booster (auxiliary) and discharged battery
should be treated carefully when using jumper
cables.
W hen using the f ollowing procedur e, be careful not
to cause any sparks.
CAUTION:
Departure from these conditions or the
following procedure could r esult in:
1. Serious personal injury (particularly to
eyes) or property damage from such
causes as battery explosion, battery acid
or electr ical burns, and/or
2. Damage to electronic components of either
vehicle.
Never expose the battery to open flame or
electric spark as batteries generate hydrogen
gas which is explosive.
Remove rings, watches or other jew ellery. Wear
approved eye protection.
Do not allow battery fluid to contact eyes, skin,
fabrics, or painted surfaces as the fluid is a
corrosive acid. Flush any contacted area with
water immediately and thoroughly, and get
medical attention.
Take care so as to ensure metal too ls or jumper
cables do not contact the positive battery
terminal (or metal in contact with it) and any
other metal on the vehicle, because a short
circuit could occur.
1. Position the two vehicles so that they are NOT
touching and apply the park brak es. Autom atic
transmission are to be placed in PARK and
manual transmissions placed in NEUTRAL.
Turn off the ignition, lights and all other
electrical loads.
NOTE:
Ensure that booster vehicle’s battery has a 12 volt
rating and has negative earth connection, otherwise
serious injury or damage to electrical equipment
may result .
2. On both batteries, check that vent caps are
tight. Place a wet cloth (if available) over vents
caps of each battery.
3. Attach one end of one jumper cable (red) to
the positive terminal of the booster battery and
the other end of the s am e cable to the positive
terminal of the discharged battery.
4. Attach one end of the second jumper cable
(black) to the negative terminal of the booster
battery and the other end to a solid stationary,
me tallic point on the engine of the vehicle with
the discharged battery. DO NOT CONNECT
DIRECTLY TO NEGATIVE POST OF
DISCHARGED BATTERY.
Figure 12A-13