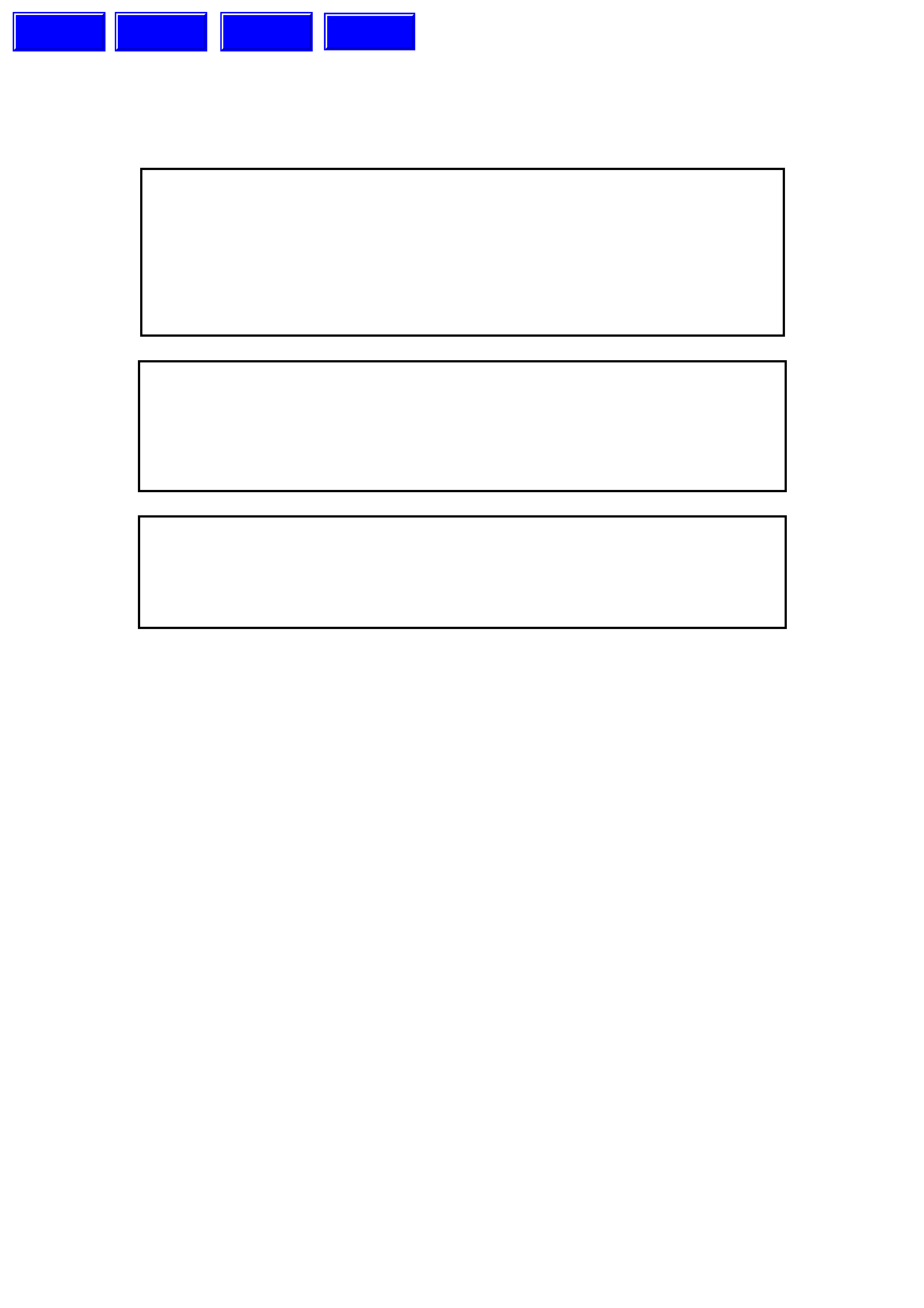
SECTION 2A - AIR CONDITIONING - DESCRIPTION
AND OPERATION
CAUTION:
This vehicle will be equipped with a Supplemental Restraint System (SRS). A SRS
will consist of either seat belt pre-tensioners and a driver’s side air bag, o r seat belt
pre-tensioners and a driver’s and front passenger’s side air bags. Refer to
CAUTIONS, Section 12M, before performing any service operation on or around SRS
components, the steering mechanism or wiring. Failure to follow the CAUTIONS
could result in SRS deployment, resulting in possible personal injury or unnecessary
SRS system repairs.
CAUTION:
This vehicle may be equipped with LPG (Liquefied Petroleum Gas). In the interests of
safety, the LPG fuel system should be isolated by turning 'OFF' the manual service
valve and then draining the LPG serv ice lines, before any service w ork is carried out
on the vehicle. Refer to the LPG leaflet included with the Owner's Handbook for
details or LPG Section 2 for more specific servicing information.
CAUTION:
Whenever any component that forms part of the ABS or ABS/ETC (if fitted), is
disturbed during Service Operations, it is vital that the complete ABS or ABS/ETC
system is checked, using the procedure as detailed in 4 DIAGNOSIS, ABS or
ABS/ETC FUNCTION CHECK, in Section 12L ABS & A BS/ETC.
1. GENERAL DESCRIPTI ON
An integrated air conditioning system is optional on the VT Commodore Executive. This integrated system
combines both the heating and cooling functions in a single unit. The A/C system is switched OFF or ON by the A/C
switch located in the centre dash facia.
The vehicles interior can be heated, cooled or vented (or a combination of these operations) depending on the
position of the two rotary mode switches.
Air enters the heating, ventilation and air conditioning system (HVAC) from under the plenum chamber cover. The
air then passes through the blower motor, evaporator and heater assemblies, to be cooled or heated as required. It
then exits through the centre, side, floor or demist outlets into the vehicle interior. The air outlets are dependant on
the position activated via the mode control.
The centre ventilator outlet can be ‘turned down’ to increase air flow to rear outlets once face comfort is achieved.
A four speed blower fan forces air from the plenum chamber through the evaporator and heater assembly, then out
through the various outlets into the vehicle interior.
NOTE:
The fan switch must be engaged to provide circulation of air over the evaporator coil.
Outside air is used in all mode positions except when recirculate is selected. This mode can be selected via the
mode control switch and is used to close off the vehicle interior from any outside air.
Recirculate mode is normally selected for:-
•Quick cool down of vehicle interior especially after the vehicle has been parked in direct sunlight for a length of
time.
•Improve heat up time as no cooler outside air can flow into the vehicle interior.
•Driving on unsealed roads to prevent dust entering the vehicle interior.