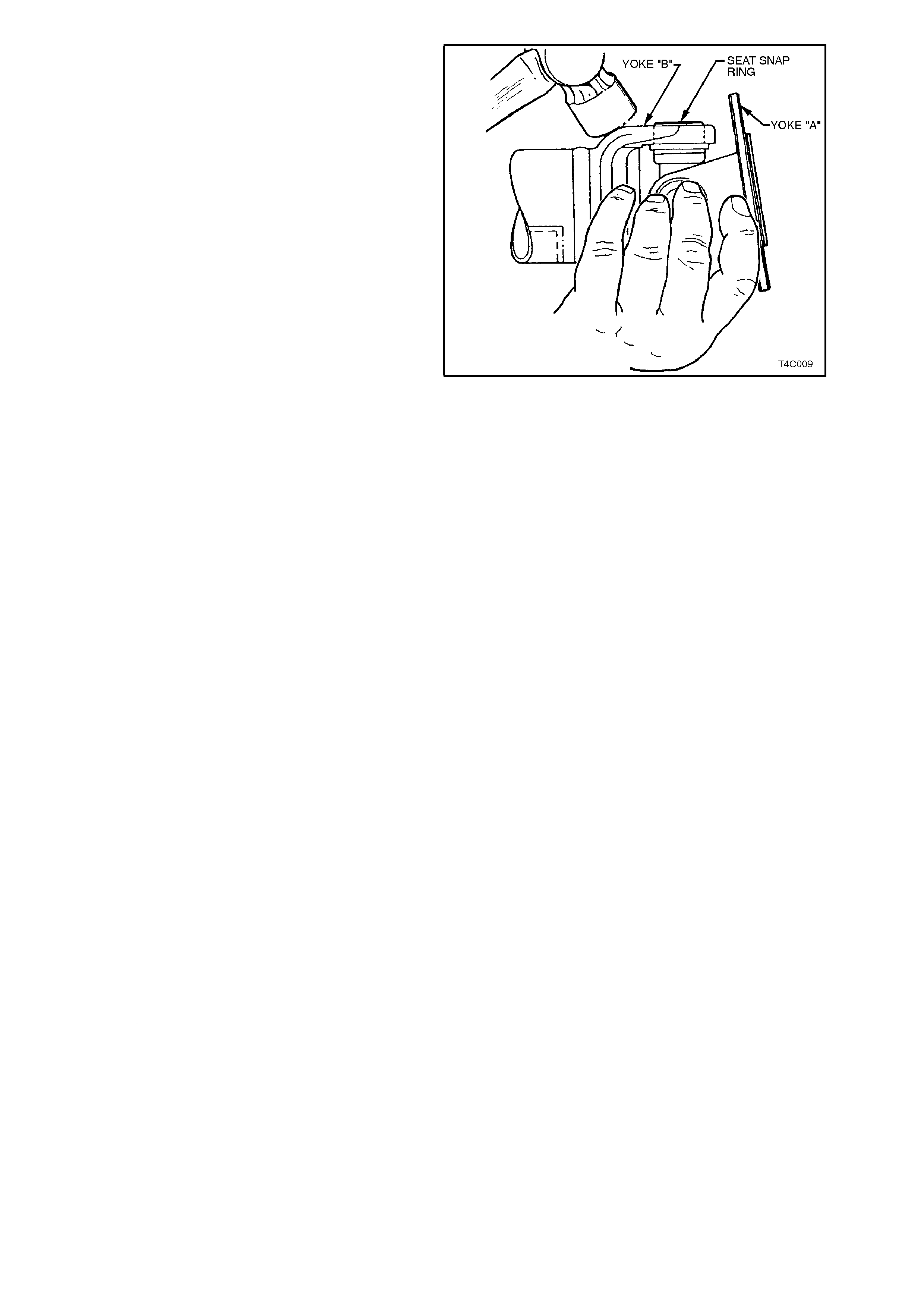
3. Support yoke 'A' in the palm of one hand, to
minimise the possibility of the needle rollers
being brinelled.
NOTE:
Yoke 'A' in the rear universal joint is the pinion
flange com ponent, while in the front universal joint,
yoke 'A' will be the slip joint.
4. Strike the forged part of yoke 'B' with a
hammer, to ensure that the snap ring is fully
seated. Take care not to strike the propeller
shaft tubing or any machined surfaces during
this process. With V8 and manual
transmission, take particular care that the
speed sensor toothed ring is not damaged in
any way during this process.
5. Repeat seating procedure with the opposite
cup.
6. Reverse the position of yokes 'A' and 'B' and
repeat the seating process described in steps
2 and 3.
7. Check that the rotational torque required for
each of the two pivot axes is now similar.
8. Should a check of the other universal joint
indicate that uneven rotation torque is evident,
then the procedure just described should also
be applied to the cups in that universal joint.
Figure 4C-55
9. Reinstall the propeller shaft assembly, as
described in 2.1 PROPELLER SHAFT, then
road test the vehicle to ensure that the
vibration condition has now been corrected.
Driveline Angles Outside Specification
NOTE:
The maximum allowable tolerance from
specification is ± 0.5°.
If driveline angles are not to specification, start by
raising or lowering the c entre bear ing r elative to the
underbody by adding, repositioning or subtracting
spacers between the centre bearing carrier and
underbody or between the centre bearing carrier
and centre bearing.
Raising the centre bearing by 7 mm will increase
Angle "A" (or make more positive) by +0.7°, and
increase Angle "C" (or make more positive) by
+0.6°.
NOTE:
Achievement of correct angle "B" (at constant
velocity joint) is not as critical as Angles "A" and
"C" for minimising noise and vibration.
W hen driveline angles are to specification, rem ove
inclinometer and reinstall the exhaust system.
Refer to Section 8B EXHAUST SYSTEM for
details.