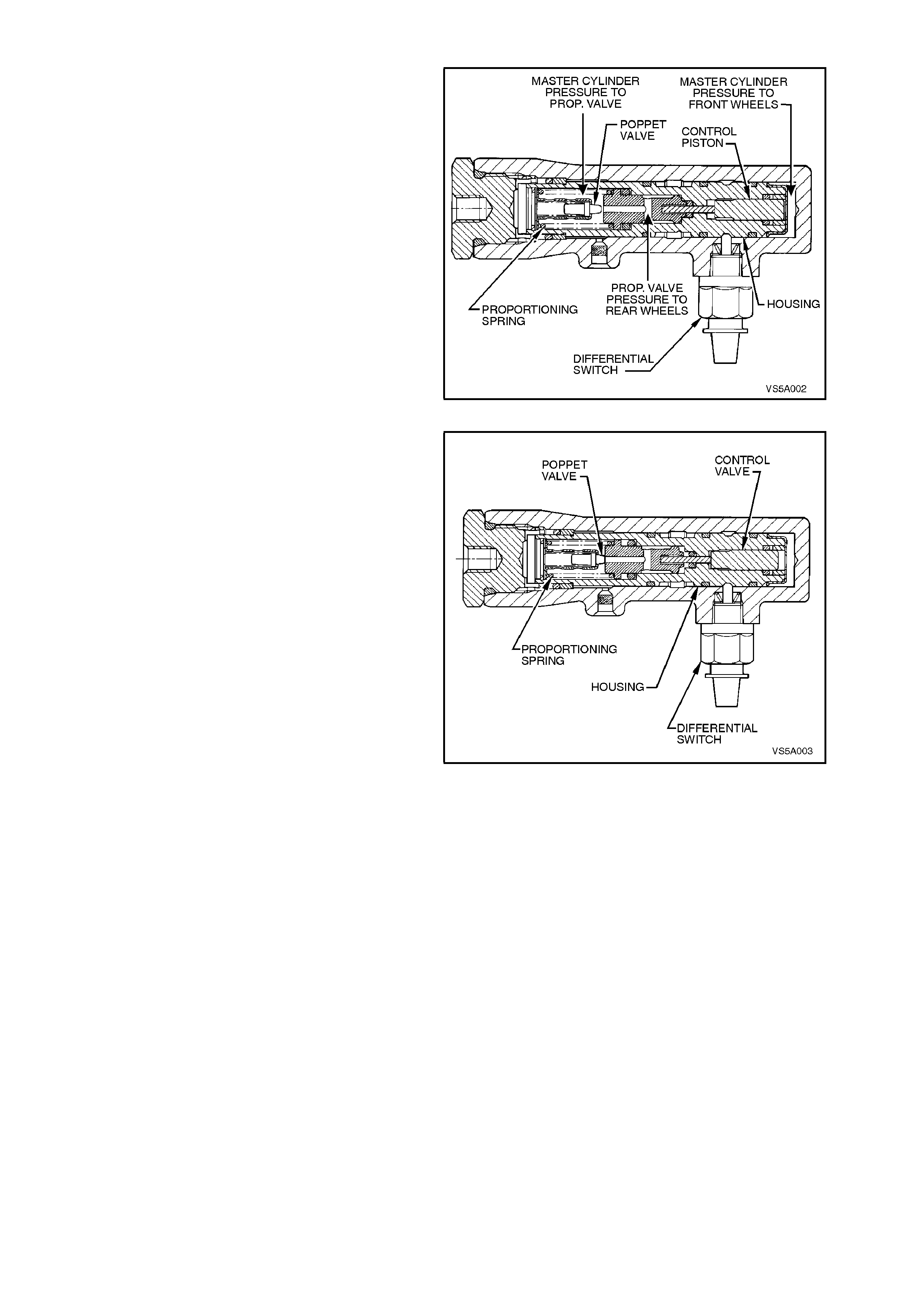
PROPORTIONING VALVE OPERATION
In the relaxed position (see Figure 5A-8), the
proportioning valve piston is held in the valve
housing by the large proportioning spring.
The poppet valve is held against the end of its
retainer by a light return spring and brake fluid is
free to pass from the master cylinder, through the
bore of the proportioning valve piston to the rear
brakes.
Figure 5A-8
W hen master cylinder pressure is increased to the
proportioning valve crack point (see Figure 5A-9),
brake fluid pressur e from the primary section of the
master cylinder acting on the control piston forces
the proportioning valve piston to move to the plug
end, overcom ing the large proportioning s pring and
seals against the poppet valve. This prevents any
further increase in press ure to the rear brakes until
master cylinder pressure is increased.
The proportioning valve piston, once seated, now
has a larger diameter than the control piston. As a
consequence of this differential area, the output to
the rear brakes af ter cr ac k point has been r eac hed,
is less than that applied to the front brakes.
As master cylinder pressure is further increased
above crack point, the piston oscillates against the
poppet valve and proportions the rear brake
pressure to a value lower than the front brakes.
Figure 5A-9
W hen the brake pedal is released (see Figure 5A-
8) and the fluid pressure from the master cylinder
drops, the pressure of the rear brake fluid unseats
the poppet valve, allowing the fluid to return to the
master cylinder. The large proportioning spring
then returns the proportioning valve piston and
control piston to their relaxed positions.
Should a loss of pressure occur in either the front
or rear brake system, when the brake pedal is
applied, the proportioning valve housing will move
within the master cylinder body, closing the switch
contacts on the differential switch and thus
illuminating the brake fail warning light on the
instrument panel.
After repairs have been made, application of a
reasonable force to the brake pedal will
automatically centralise the proportioning valve
housing, opening the differential switch contacts
and turning the brake warning light off.