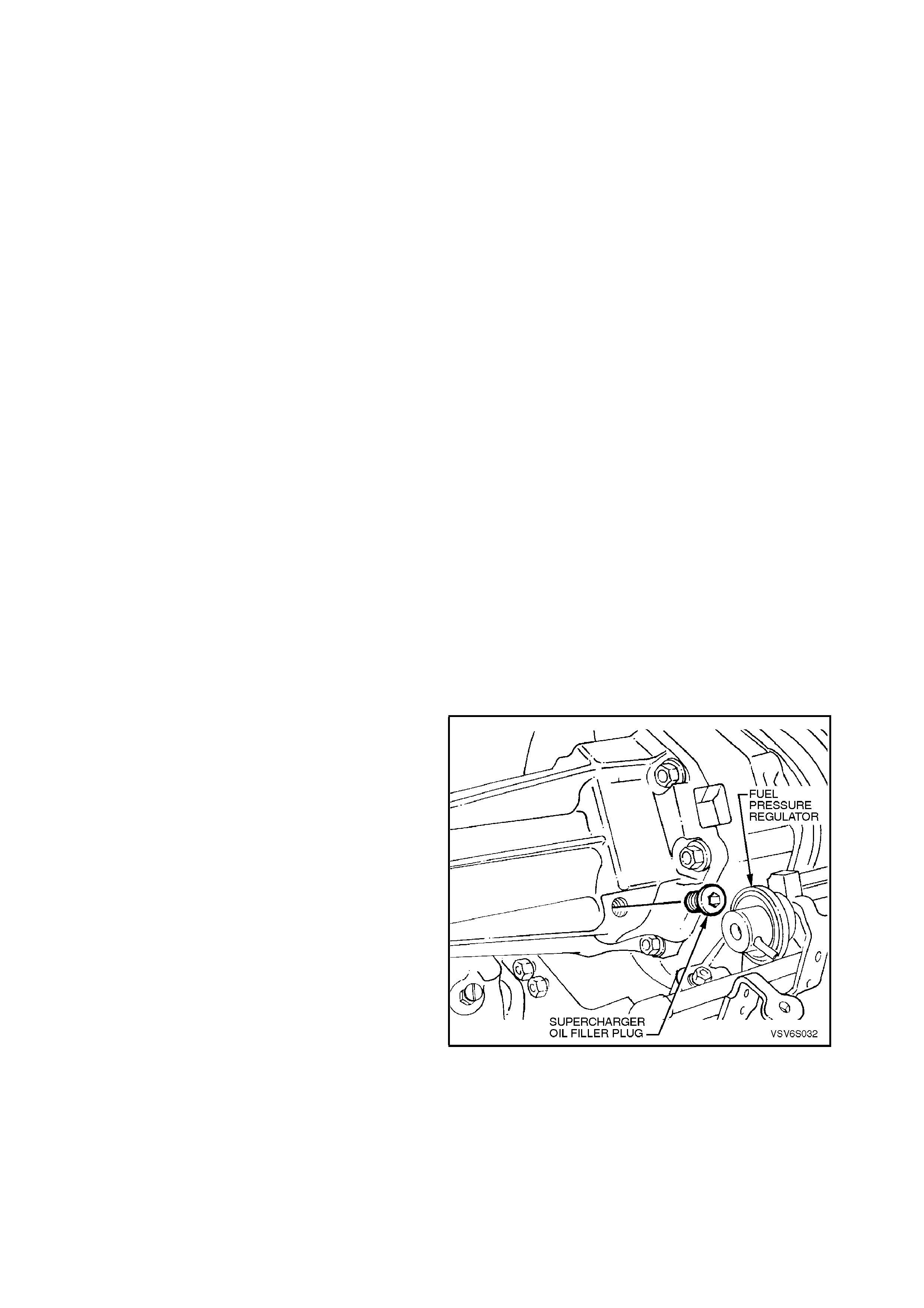
2. SERVICE OPERATIONS
2.1 SUPERCHARGER OIL LEVEL CHECK
NOTE:
A small amount of oil weepage through the front
seal, (behind the pulley) of the supercharger
assembly is normal. T his oil weepage is c aused by
minute traces of oil escaping around the seal. A
build up of airborne dust can adhere to the thin oil
film which causes oil weepage to appear worse
than it really is. The superc harger ass embly should
not be replaced due to weepage. If supercharger
oil is visually dripping or puddling from the
supercharger front seal, the supercharger
assembly will need to be replaced. Refer to
2.2 SUPERCHARGER AND GASKET in this
Section.
CAUTION:
Do not remove the oil plug when engine is
warm. Engine should be cool to the touch.
Approximately 2 -3 hours after running.
Removing oil plug at warm engine
temperatures can cause hot oil to overflow.
This could result in oil loss and possible
personal injury.
Lubricant level is to be checked at the specified
service intervals outlined in the VT Series Owner’s
Handbook.
REMOVE
1. Remove the four dome nuts securing the
engine dress cover assembly to the mounting
bracket studs, refer to Fig. 6A1-2-17, lift off
and remove the cover assembly.
NOTE:
To prevent contamination of the supercharger oil,
clean the area around the oil filler plug before
removing.
2. Using a 3/16 inch Allen key socket, remove
supercharger filler plug.
3. Check oil level.
NOTE:
The oil level should be maintained to a level at the
bottom of the threads in the oil filler plug inspection
hole in the supercharger housing.
IMPORTANT:
Do not use petroleum based oil. Use only GM p/no.
12345982 synthetic oil. Use of other oil may cause
supercharger failure.
Figure 6A1-17