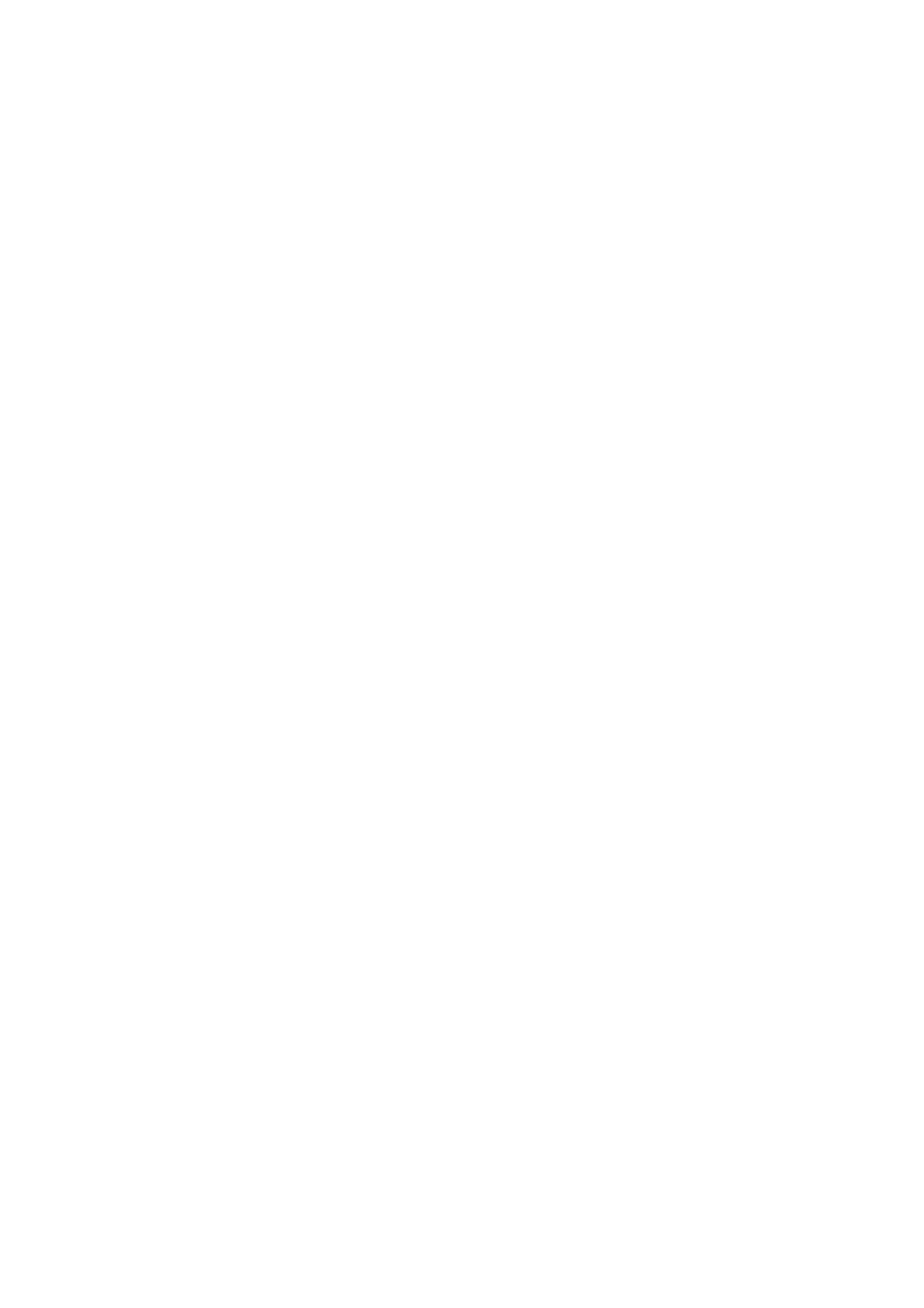
TECH 2 SCAN - TRANSM ISSION DATA DESCRIPTIONS
A list of explanations for each data message displayed on the Tech 2 scan tool begins as follows. This information
will assist in tracking down emission or driveability problems, since the displays can be viewed while the vehicle is
being driven. Refer to the "On-Board Diagnostic System Check" for additional informational.
ENGINE SPEED - Range 0-9999 RPM - Displays the PCM's interpretation of actual engine speed, as received from
the reference input signal. Displays in increments of 1 RPM. Often useful to detect if extra reference pulses are
suspected. A sudden high RPM indication while at a steady throttle would indicate electrical interference in the
reference input signal circuit. This interference is usually caused by PCM wires too close to ignition secondary wires
or an open reference earth circuit.
VEHICLE SPEED - Range 0-255 KM/H - Displays the PCM's interpretation of vehicle speed as received from the
PCM. If this position indicates no vehicle speed (zero), but the speedometer shows otherwise, then a Diagnostic
Trouble Code 24 will eventually set. Also useful for checking speedometer accuracy.
TPS VOLTAGE - Range 0-5.10 VOLTS - This position shows the Throttle Position sensor signal input to the PCM.
Values read will be in voltage and will interpret the throttle opening to the PCM. The voltage should between 0.25 -
1.25 volts with the throttle closed and go up to approximately 4.5 volts at Wide Open Throttle (WOT).
TPS ANGLE - Range 0-100% - This display is the PCM's interpretation of the percentage of throttle opening. TPS
angle should display zero (0%) with the throttle closed and 100% at Wide Open Throttle (WOT).
ECT SENSOR VOLTS/ENG COOLANT TEMP - Range -40 degrees to 151 degrees C/ 0 - 5.10 Volts - The
Engine Coolant Temperature (ECT) sensor is mounted in the inlet manifold and sends engine temperature
information to the PCM applies 5 volts to the coolant temperature sensor circuit. The sensor circuit. The sensor is a
thermistor which changes internal resistance as temperature changes. When the sensor is cold (internal resistance
high), the PCM monitors a high signal voltage which it interprets as a cold engine. As the sensor warms (internal
resistance decreases), the voltage signal will increase, the voltage signal will decrease and the PCM will interpret
the lower voltage as a warm engine.
TFT SENSOR VOLTS/TRANS FLUID TEMP - Range -40 degrees C to 151 degrees C/ 0 - 5.10 VOLTS - This
position will display the PCM's interpretation of temperature in the transmission. The Transmission Fluid
Temperature (TFT) sensor is mounted in the valve body and is wired to the PCM. The PCM monitors the difference
in voltage between two terminals, and the TECH 1 scan tool will display TFT in voltage and a temperature shown in
degrees Celsius. The TFT sensor reading should read close to the air temperature when the transmission is cold,
and increases as the transmission fluid temperature increases. After the engine is started the temperature should
rise steadily to about 82 degrees C- 94 degrees C then stabilise.
TFP SWITCH A/B/C VOLTS - Range 0 Volts or 12 VOLTS - These values represent the three fluid pressure
switch assembly signals. These lines are normally high and are taken low as the fluid pressure switch interprets the
manual valve position. The sequence of these signals is decoded by the PCM to determine the appropriate gear
range. O volts indicates closed, and 12 volts indicates open.
TFP GEAR - Tech 2 Displays P/N-R,D,3,2,1 - This value represents the decoded sequence of the Transmission
Fluid Pressure Manual Valve Position Switch Assembly (TFP). The TFP is used to determine the manual valve
position. The manual valve position is an input to the PCM used to control line pressure, TCC, and shift solenoid
operation.
PRNDL SWITCH - Tech 2 Displays Invalid or P, R, N, D, 3, 2, 1 - This displays if the vehicle is not equipped with
a PRNDL switch ( Invaded), or if equipped, indicates what gear the driver has selected.
1-2 SHIFT SOLENOID, 2-3 SHIFT SOLENOID - The 2 Displays "ON" or "OFF" - This displays the "ON" or "OFF"
state of the two shift solenoids. The shift solenoids are turned "OFF" or "ON" to change gears.
1-2 AND 2-3 SHIFT SOLENOID FEEDBACK - The 2 Displays ON/OFF - The 2 Displays "ON" or "OFF" - These
values represent the true electrical state of the solenoids. The PCM uses this information to set malfunction DTC's.
1-2 SHIFT TIME -Tech 2 Displays Time - This value represents the time taken to shift from first gear to second
gear. This information is only accurate if the shift was adaptable.
2-3 SHIFT TIME - Tech 2 Displays Time - This value represents the time taken to shift from second gear to third
gear. This information is only accurate if the shift was adaptable.
COMMANDED PCS - Tech 2 Range 0 to 1000 Millamps - This value represents the commanded pressure control
solenoid current. The commanded current is determined from the manual valve position, transmission fluid
temperature, transmission output speed, shift solenoid state, TCC, A/C status, engine speed, TCC slip and the
throttle position sensor. The commanded pressure control solenoid current is then used to control the transmission
line pressure.
ACTUAL PCS - Tech 2 Range 0 to 1000 Millamps - This value represents the actual pressure control solenoid
current. This value should always be very similar to the desired pressure control solenoid current. If the actual
deviates from the desired by 0.16 amps, a DTC will set.
PCS DUTY CYCLE - The 2 Range 0 to 100 % - This value represents the pressure control solenoid duty cycle.
This value is determined by the desired pressure control solenoid current.