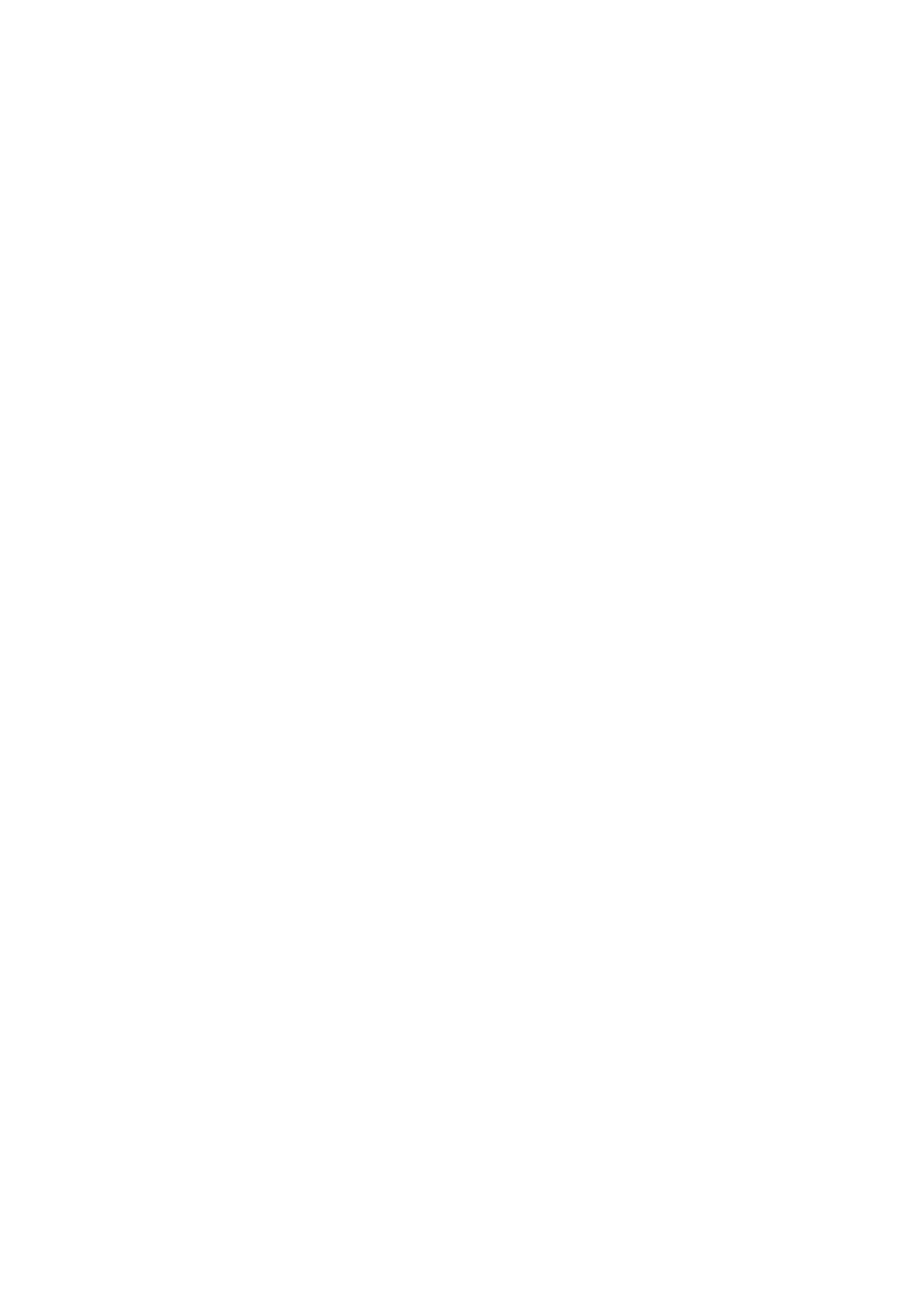
1.1 OPERATION
With the ignition switch turned to the ON position, current is supplied via the warning lamp to the ‘L’ terminal of the
regulator. Base current from the regulator hybrid circuit is fed to the transistor T15 which turns ON. Current then
flows from the B+ terminal through the rotor winding via the regulator brushes and the collector emitter junction of
transistor T15 to earth, completing the circuit.
The current in the rotor causes a magnetic field between adjacent poles to be created, this field is rotated and cuts
the windings of the stator at right angles inducing a voltage into them. As the speed is increased, this induced
voltage increases and results in current being rectified in the 3 phase diode bridge and supplied as DC to the B+
output and hence to the battery. When the voltage at the B+ terminal to the battery reaches approximately 14.2
volts, the ‘S’ terminal which is monitoring this voltage, turns the regulator hybrid circuit base current to the transistor
T15 off, removing rotor current. This results in a decrease in output voltage to below the regulating voltage,
transistor T15 base current is turned back on and the whole cycle is repeated very rapidly. Diode D38 protects the
transistor T15 and the regulator against the back voltage developed across the rotor winding when transistor T15
tu rns off.
Should a situation arise where the main B+ cable or battery sense wire (terminal S) become disconnected or have a
high resistance, the regulator will limit the output voltage to a safe level (backup mode), approximately 1-3 volts
above the regulators normal setting.
When the ignition switch is turned on and the engine is not running, the current to the rotor is reduced by switching it
on and off at a 50% duty cycle (active standby mode), the frequency is approximately 4kHz and may be audible at
times (this is normal). Once the engine is started, normal regulation commences.
Should the warning lamp fail, the generator will self excite by deriving a small current from the phase connection
allowing the voltage to build up to regulating level.
NOTE:
No rotor winding current will flow when the engine is cranking.
The regulator incorporates internal diagnostics which will illuminate the warning lamp as a result of fault conditions
in the generator and/or external circuitry.
These conditions include:
1. An open circuit in the regulator battery sensing wire (S terminal).
2. An open circuit or excessive voltage drop in the B+ cable.
3. An open circuit in the generator phase connection.
4. Overcharging of the battery.
5. Regulator output stage short circuit.
6. Open circuit in the rotor winding.
The regulator compares the voltage at the B+ terminal with the voltage sensed at the S terminal connected to the
battery positive. If the voltage differential exceeds a predetermined threshold, the regulator will operate in backup
mode to limit the output voltage to a safe level. The warning lamp will remain illuminated as long as the fault
conditions prevail.
Sources of high resistance which will trigger the warning lamp are:
1. Poor contact in the wiring harness connectors.
2. Poor contact between the rectifier and the regulator.
3. High resistance in the fusible link assembly or battery terminals and cables.