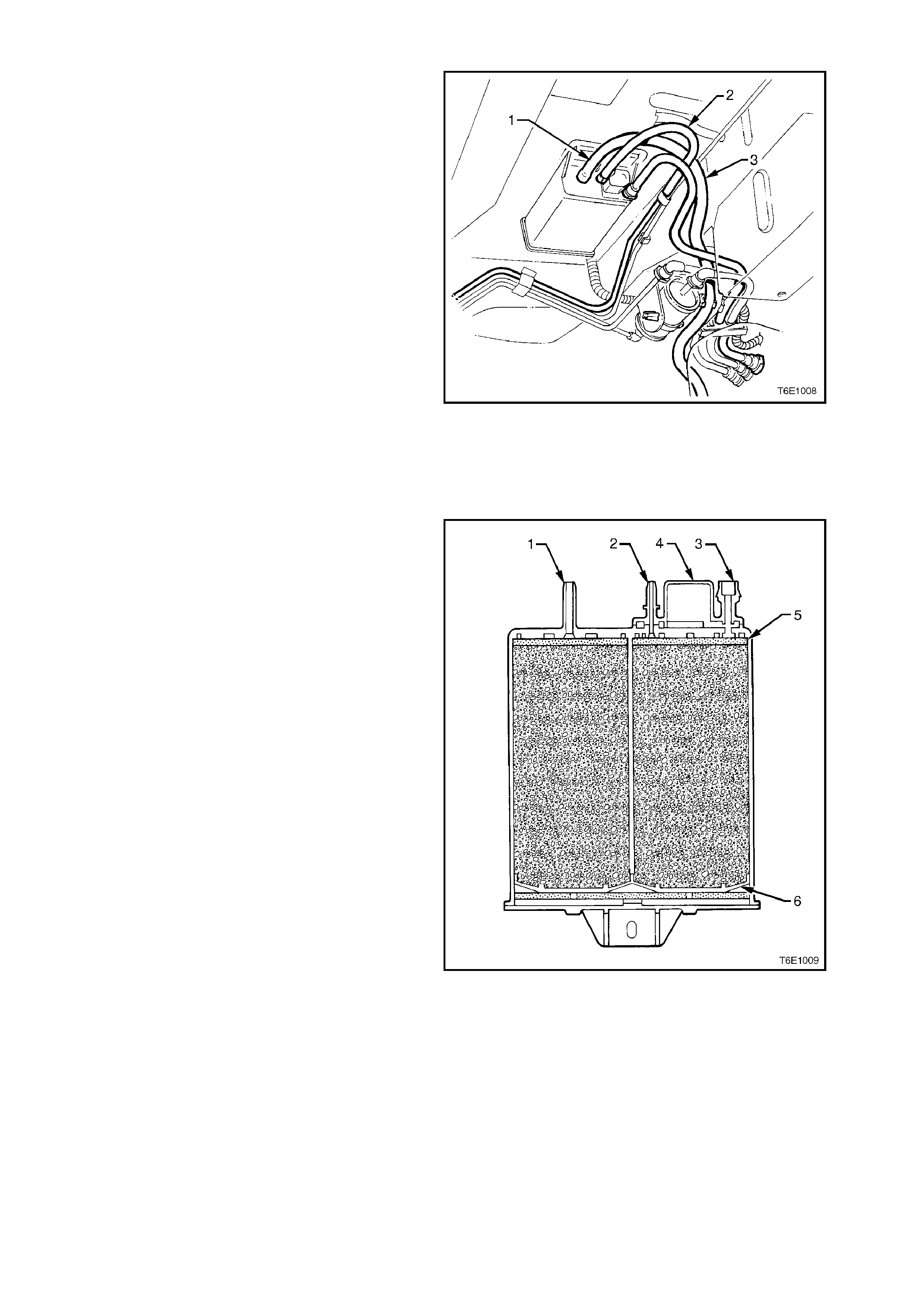
1.4 EVAPORATIVE EMISSION CONTROL
The Evaporative Emission Control System (EECS)
captures fuel vapours, which would normally
escape from the fuel tank and enables them to be
consumed in the combustion process. The EECS
used on VT Series Models is the charcoal canister
storage m ethod. This method transfers fuel vapour
from the fuel tank to an activated car bon (charcoal)
storage canister to hold vapours when the vehicle
is not operating. When the engine is running, the
fuel vapour is purged from the carbon element by
intake air flow and consumed in the normal
combustion process. The fuel tank cap is not
vented to atmosphere, but is fitted with a valve to
allow both pressure and vacuum relief. The
canister is a three port design:
1. Atmospheric port (fresh air inlet)
2. Purge Port
3. Vapour inlet port
The fuel vapour is absorbed by the charcoal in the
canister. When the engine is running, air is drawn
into the canister through the atmospheric port at
the top of the canis ter ass embly. The air mixes with
the vapour and the m ixture is drawn into the intake
manifold via the canister purge line.
Figure 6E1-8
The purge port (3) on the c anister is controlled by a
PCM activated purge solenoid valve. The solenoid
valve controls the manifold vac uum s ignal from the
throttle body. The vapour inlet port (1) allows fuel
vapour to enter the canis ter from the f uel tank . T he
atmospheric port (1) allows fresh air to be drawn
into the canister.
This system has a remote mounted canister purge
control solenoid valve. The PCM operates this
solenoid valve to control vacuum to the canister.
Under cold engine conditions, the solenoid valve is
turned OFF by the PCM, which blocks vacuum to
the canister and prevents purge.
The PCM turns ON the solenoid valve and allows
purge:
• When the engine coolant temperature is less
than 20° C, 3 minutes and 10 seconds after
engine start.
• W hen the engine c oolant temper ature is greater
than 80° C, 5 seconds after engine start.
• Engine is not in Dec el Fuel Cutof f Mode and the
throttle opening is less than 92%.
• Engine is in Closed Loop Fuel Mode.
The canister cannot be repaired, and is serviced
only as an assembly. Periodically check the
canister at the time or distance intervals specified
in the VT Series Owner's Handbook.
1. Atmospheric Port
2. Vapour Inlet Port
3. Purge Port
4. Liquid Trap
5. Volume Compensator and Filter
6. Diffuser
Figure 6E1-9