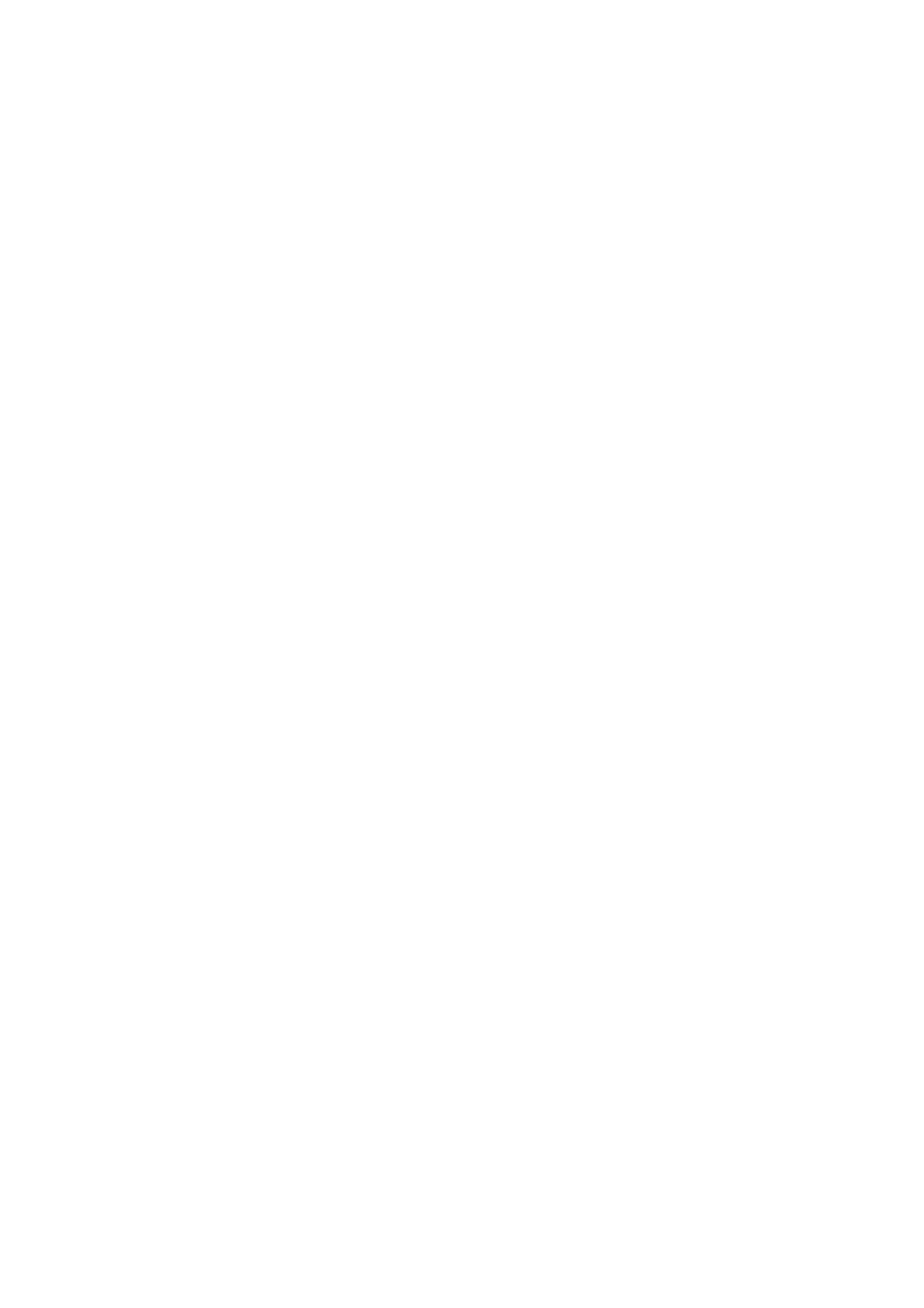
3. TRANSM ISSION DEFINITIONS AND ABBREVIATIONS
The following definitions and abbreviations are provided to establish a common language and assist the user in
describing transmission related conditions. The use of these terms and/or conditions can be found in the various
parts of the automatic transmission section, but more particularly, in 7C3 HYDRAULIC/MECHANICAL
DIAGNOSIS.
3.1 DEFINITIONS
The following definitions have been arranged in alphabetical order and are intended to assist the user with an
explanation of their meaning, in order to gain the maximum benefit from those Sections that deal with the
Hydra-matic 4L60-E, automatic transmission. There are additional, unique definitions in
Section 7C3 HYDRAULIC/M ECHANICAL DIAGNOSIS that should also be r eferred to when using that particular
information.
Accumulator - A component of the transmission that absorbs hydraulic pressure during the apply of a clutch or
band. Accumulators are designed to control the quality of a shift from one gear range to anther. within
Adaptive Learning - Programming within the PCM that automatically adjusts hydraulic pressures in order to
compensate for changes in the transmission (i.e. component wear).
Applied - An 'Apply Component' that is holding another component to which it is splined or assembled to. Also
referred to as "engaged".
Apply Components - Hydraulically operated clutches, servo’s, bands and mechanical one-way roller or sprag
clutches that drive or hold members of a planetary gear set.
Apply Plate - A steel clutch plate in a clutch pack, located next to the (apply) piston.
Backing Plate - A steel plate in a clutch pack that is usually the last plate in that clutch assembly (furthest from
the clutch piston).
Band - An apply component that consists of a flexible strip of steel and friction material that wraps around a drum.
When applied, it tightens around the drum and prevents the drum from rotating.
Brake Switch - An electrical device that provides signals to the Powertrain Control Module (PCM), based on the
position of the brake pedal. The PCM uses this information to apply or release the torque converter clutch (TCC).
Centrifugal Force - A force that is imparted on an object (due to rotation) that increases as that object moves
further away from a centre-point of rotation.
Checkball - A spherical, hydraulically controlled component (usually of steel) that either seals or opens fluid
circuits. It is also referred to as a check valve.
Clutch Pack - An assembly of components generally consisting of clutch plates, an apply plate and a backing
plate.
Clutch Plate - An hydraulically activated component that has two basic designs: (1) all steel, or (2) a steel core
with friction material bonded to one or two sides of the plate.
Control Valve Body - A machined metal casting that contains valve trains and other hydraulically controlled
components that shift the transmission.
Coupling Speed - The speed at which a vehicle is travelling and no longer requires torque multiplication through
the torque converter. At this point, the stator 'free wheels' to allow fluid leaving the turbine to flow directly to the
pump. (Also see Torque Converter).
De-energise(d) - To interrupt the electrical current that flows to an electronically controlled device, making it
electrically inoperable.
Direct Drive - A condition in a gears set where the input speed and input torque equals the output speed and
output torque. The gear ratio through the gear set is 1:1.
Downshift - A change in a gear ratio where both input speed and torque increases.
Duty Cycle - In reference to an electronically controlled solenoid, it is the amount of time (expressed as a
percentage) that current flows through the solenoid coil.
Energise(d) - To supply a current to an electronically controlled device, enabling it to perform its designed
function.
Engine Compression Braking - A condition where compression from the engine is used with the transmission to
decrease vehicle speed.
Exhaust - The release of fluid pressure from a hydraulic circuit. (The words 'exhausts' and 'exhausting' are also
used and have the same intended meaning.)
Fail-Safe Mode - A condition whereby a component (i.e. engine or transmission) will partially function even if its
electrical circuit is disabled.
Fluid - In this Section, 'fluid' refers primarily to Automatic Transmission Fluid (or ATF) and, for the Hydra-matic
4L60-E transmission, the only recommended fluid is Dexron III®.
Fluid Pressure - A pressure that is consistent throughout a given fluid circuit.
Force - A measurable effort that is exerted on an object (component).
Freewheeling - A condition where power is lost through a driving or holding device (i.e. roller or sprag clutches).
Friction Material - A heat and wear resistant fibrous material, bonded to clutch plates and bands.
Gear - A round, toothed device that is used for transmitting torque through other components.