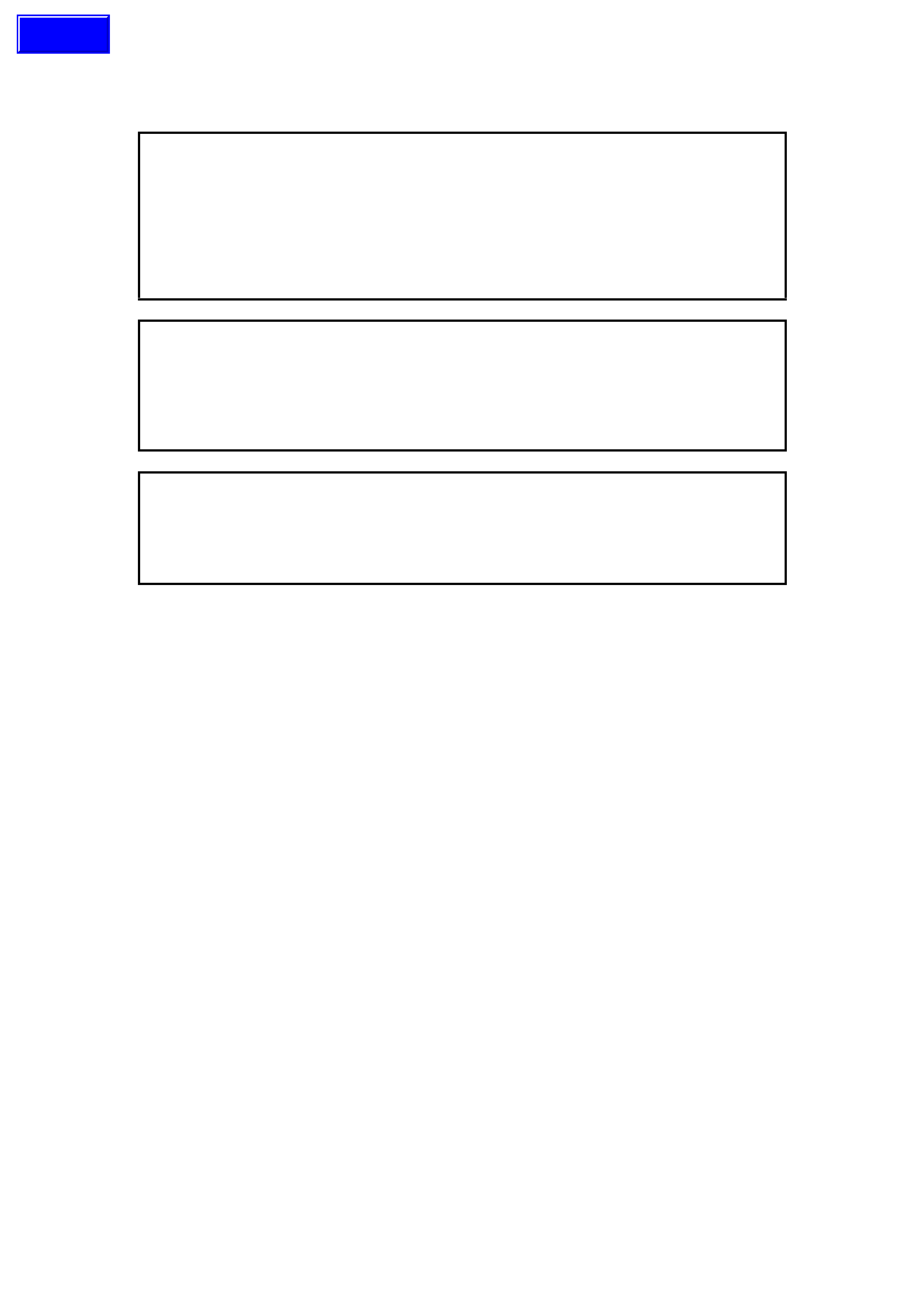
SECTION 8A - FUEL TANK
CAUTION:
This vehicle will be equipped with a Supplemental Restraint System (SRS). An SRS
will consist of either seat belt pre-tensioners and a driver's side air bag, or seat belt
pre-tensioners and a driver's and front passenger's side air bags. Refer to
CAUTIONS, Section 12M, before performing any service operation on or around any
SRS components, the steering mechanism or wiring. Failure to follow the CAUTIONS
could result in SRS deplo yment, resulting in possible p ersonal injury or unnecessary
SRS system repairs.
CAUTION:
This vehicle may be equipped with LPG (Liquefied Petroleum Gas. In the interests of
safety, the LPG fuel system should be isolated by turning ‘OFF’ the manual service
valve and then draining the LPG serv ice lines, before any service w ork is carried out
on the vehicle. Refer to the LPG leaflet included with the Owner's Handbook for
details or LPG Section 2 for more specific servicing information.
CAUTION:
Whenever any component that forms part of the ABS or ABS/ETC (if fitted), is
disturbed during Service Operations, it is vital that the complete ABS or ABS/ETC
system is checked, using the procedure as detailed in 4. DIAGNOSIS, ABS or
ABS/ETC FUNCTION CHECK, in Section 12L ABS & A BS/ETC.
1. GENERAL INFORMATION
The 75 litre fuel tank fitted to all VT Series models is a multi-layer polycarbonate construction with an integral fuel
filler neck. The fuel tank is not serviceable and if damaged, must be replaced as an assembly.
The fuel tank is supported by three mounting straps and a seal is fitted around the fuel filler neck where it protrudes
through the vehicle body.
An in-tank, modular fuel sender assembly is used, that incorporates a fuel reservoir, the fuel sender unit and the
fuel pump in the one unit.
Apart from the complete assembly, serviced components for the modular fuel sender, are the fuel pump, pick-up
strainer and fuel sender assembly.
Servicing details for these and other fuel tank/line related items are covered in this Section.
Quick-connect fuel line fittings are used for all fuel line connections, including, the modular fuel sender assembly,
fuel vapour canister, fuel filter, fuel feed and return lines, both at the fuel tank and engine ends.
1.1 MODULAR FUEL SENDER ASSEMBLY
The modular fuel sender assembly is designed to maintain an optimum fuel level in the reservoir. This ensures a
continuous fuel flow under all fuel level conditions and vehicle attitudes. As there are two different construction fuel
pumps used, two fuel flow descriptions are required.
The first details fuel flow through the turbine fuel pump that is used with both the V6 and V8 engines.
Turbine Fuel Pump (View A, in Figure 8A-1)
Fuel is drawn into the reservoir from the fuel tank, through the external strainer (3) and into the fuel pump’s first
stage impeller, via the primary fuel pump inlet. First stage fuel is then directed to the reservoir, filling the reservoir
bucket..
Fuel levels in the reservoir are also maintained by return engine fuel, via the return line. Reservoir fuel flow
proceeds through the fuel pump strainer, bypassing the first stage impeller. Fuel proceeds to the second impeller
and the high pressure third stage of the impeller pump.
High pressure fuel then flows through the end cap, the lower connector and the fuel pump flex pipe. From the flex
pipe, fuel then exits the modular fuel sender assembly through the fuel feed fitting and flows on to the externally
mounted fuel filter.