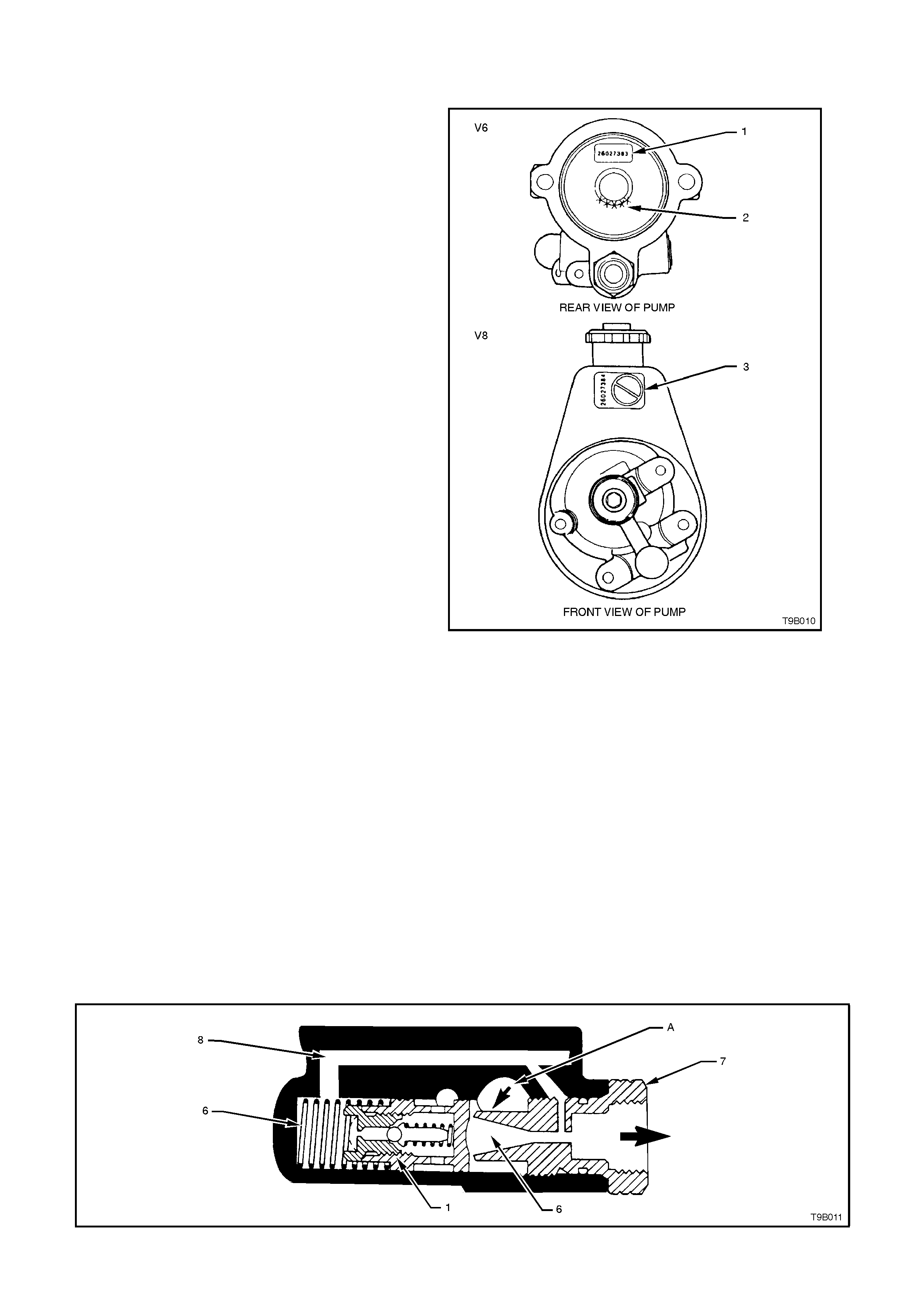
1.3 POWER STEERING PUMPS
GENERAL DESCRIPTION
The power steering pumps fitted to vehicles with
speed sensitive power steering are of the constant
flow type. However, servicing procedures are
essentially the same as those for the droop flow
design, fully detailed in Section 9A STEERING.
The only exception is the outlet fitting, which does
not feature a m etering needle valve as in the dr oop
flow design.
If a power steering pump r equires r eplacement, it is
essential that the correct type is selected. Refer to
the following table and the diagram shown, for
identification details of the available power steering
pumps for the complete range of VT Series
vehicles, regardless whether the system is the
standard or speed sensitive design.
The location of the part number (1 or 3) is as
shown, while the last 5 digits (2) of the V6 pump is
also provided.
PUMP APPLICATION PART NUMBER
V6 ENGINE:
STANDARD 26056053
SPEED SENSITIVE 26056054
V8 ENGINE
STANDARD 26056055
SPEED SENSITIVE 26056056
Because the pumps used for the speed sensitive
power steering, have a constant flow outlet fitting,
the operation is slightly different to the droop flow
design. Figure 9B-10
CONSTANT FLOW CONTROL VALVE OPERATION
Slow Cornering
Pump speeds during slow cornering or parking are normally low, as are demands for fluid flow volume, due to
slower steering manoeuvres.
With reasonably high relative movem ent of the inner valve and outer sleeve in the s teering rac k control valve at this
time, the fluid is pressurised to approximately 3,400 kPa to 4,800 kPa and directed to the high pressure cavity
behind the pressure plate. Discharge ports direct this fluid to the outlet fitting (7) and then on to the steering gear.
The discharge fluid pressure from the outlet fitting, is slightly lower in pressure than the internal high pressure (A),
coming from the pump ring.
This drop in pressure, due to venturi action, occurs as the fluid flows through the orifice (6) in the outlet fitting (7).
This lower pres sur e is trans mitted to the spr ing (6) end of the c ontr ol valve (1) by a fluid pas s age (8) c onnec ting the
control valve (1) to the outlet fitting (7).
This results in a pressure unbalance at each end of the control valve (1), causing it to move away from the outlet
fitting (7). Owing to the force of the control valve spring (6), the valve (1) remains closed to the fluid by-pass hole.
Because suf ficient fluid is allowed to circulate through the system, fluid pressure does not build up high enough to
cause the pressure relief ball check in the valve (1).
Figure 9B-11