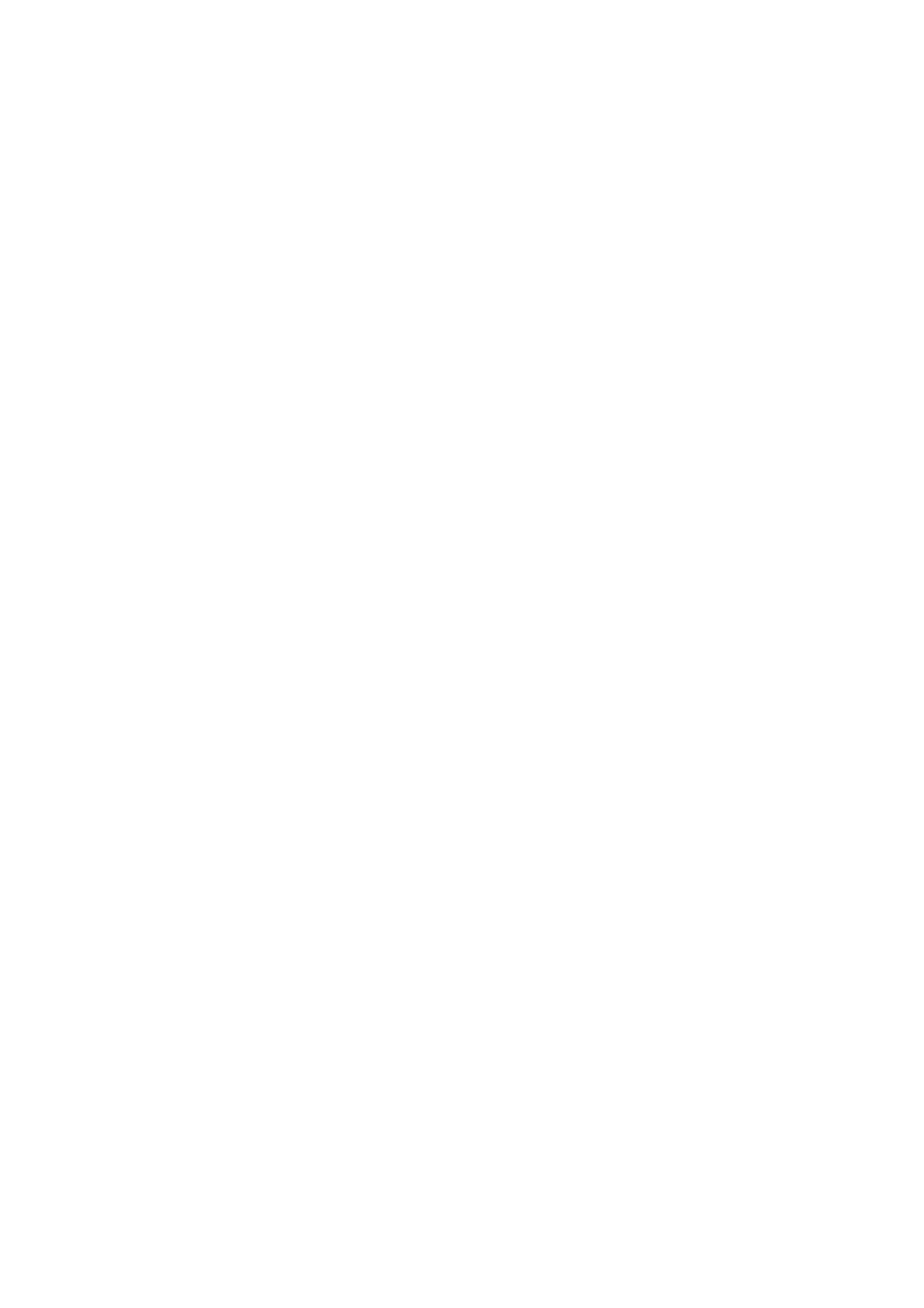
5.3 INSTRUME NT CLUS TER DIAGNOSTICS
The instrum ent cluster is equipped with a self-diagnos tic capability that can detec t and isolate instrum ent problems
or failures. W hen a fault is detected, the instrument cluster sets a Diagnostic Trouble Code (DTC) that represents
that particular problem or failure. W hen a DTC is set, an icon is shown in the left-hand instrument window on
high series vehicles, or the message SERV ERROR on low series. However, DTC 16 to DTC 20 do not set the
icon/message on the instrument cluster as these represent a fault condition logged by one of the various vehicle
control modules.
DIAGNOSTIC TROUBLE CODES
There are two types of DTC, current and history.
• A Current DT C is active only for the period that the fault is pres ent and is indic ated by the icon/mes s age on the
instrument cluster. When the fault is cleared, the Current DTC and the icon/message are also cleared.
• The History DTC is set at the same time as the Current DTC, and is stored in memory within the instrument
cluster to pr ovide inform ation on vehicle system operation over a period of tim e. History DTC are c leared from
memory 100 ignition cycles after the last DTC of any type was set.
DIAGNOSTIC MODE OPERATION
To enter the instrument cluster diagnostic mode, press the trip computer switch MODE button down together with
the ▲
▲▲
▲ button while turning the ignition from off to on. Further pressing the MODE button will step through the various
instrument cluster information displays.
When the Diagnostic Mode Display is reached, pressing the ▲
▲▲
▲ button increments the DTC number and related
inform ation displayed, while the ▼
▼▼
▼ button can be used to decrement the DTC number and related information. To
exit the instrument cluster diagnostic mode, press both the ▲
▲▲
▲ button and the ▼
▼▼
▼ button together.
A DTC is shown on the Diagnostic Mode Display as ‘t NN XY’ , where:
t = diagnostic trouble code (DTC),
NN = the actual DTC number,
X = the history DTC status (H for active and – for inactive), and
Y = the current DTC status (C for active and – for inactive).
In instances where the DTC is disabled due to the particular model configuration the letters nu (not used) appear in
the XY position. For example, a vehicle which is not fitted with ABS or ABS/ETC will have DTC 8 shown as ‘t 08 nu’.
Similarly, DTC 4, DTC 5 and DTC 6 will appear as not used on a vehicle which is not fitted with LPG.
It is important to note that an open circuit fuel (petrol) gauge sender unit is recognised by the instrument cluster self-
diagnostics as ‘t 00 H C’, whereas the TECH 2 Diagnostic Tool will recognise the same fault as DTC 3.
A DTC may also be cleared from the instrument cluster using the trip computer switches while in the diagnostic
mode. With the DTC displayed in the instrument cluster window, press both the ▲
▲▲
▲ button and the ▼
▼▼
▼ button together
for more than 2 seconds. Pressing these buttons for less than 2 seconds will exit the instrument cluster diagnostic
mode.
Faults can be identified by using TECH 2 to test instruments and force values and conditions into the instrument
cluster. The results of these tests can be used to diagnose problems in the instrument cluster such as inoperative
bulbs and faulty gauges and switches.
Faults within other components can be identified after using TECH 2 to confirm correct operation of the instruments.
For example, if there was a reported fault with the speedometer gauge and TECH 2 diagnosed the gauge as
working correctly, then the fault would lie in the Powertrain Control Module (PCM) or in the harness from the speed
sensor to the PCM, both of which would then require further testing.
USE OF TECH 2 DIA GNOSTIC TOOL WITH INTERMITTENT FAULTS
The TECH 2 Diagnostic Tool allows manipulation of wiring harnesses, while observing the TECH 2 Diagnostic Tool
readout. If the problem seems to be related to certain parameters that can be checked on the TECH 2 Diagnostic
Tool, they should be checked while driving the vehicle. If there does not seem to be any connection between the
problem and any specific circuit, the TECH 2 Diagnostic Tool can be used to monitor each parameter, watching for
a period of time to see if there is any change in the readings that indicates intermittent operation.
The TECH 2 Diagnostic Tool saves time in diagnosis and helps to prevent the replacement of good parts. The key
to using the TECH 2 Diagnostic Tool successfully is the technicians ability to understand the system being
diagnosed, as well as understanding the TECH 2 Diagnostic Tool operation and limitations. The technician should
read the TECH 2 User’s Guide to become familiar with the TECH 2 Diagnostic Tool operation.
With an understanding of the data which the tool displays, and knowledge of the circuits involved, the tool can be
very useful in obtaining information which would be more difficult or impossible to obtain with other equipment.
The TECH 2 Diagnostic Tool does not make the use of diagnostic charts unnecessary, nor can it indicate exactly
where a problem is in a particular circuit. Diagnostic charts incorporate diagnostic procedures that require the use
of a TECH 2 Diagnostic Tool.