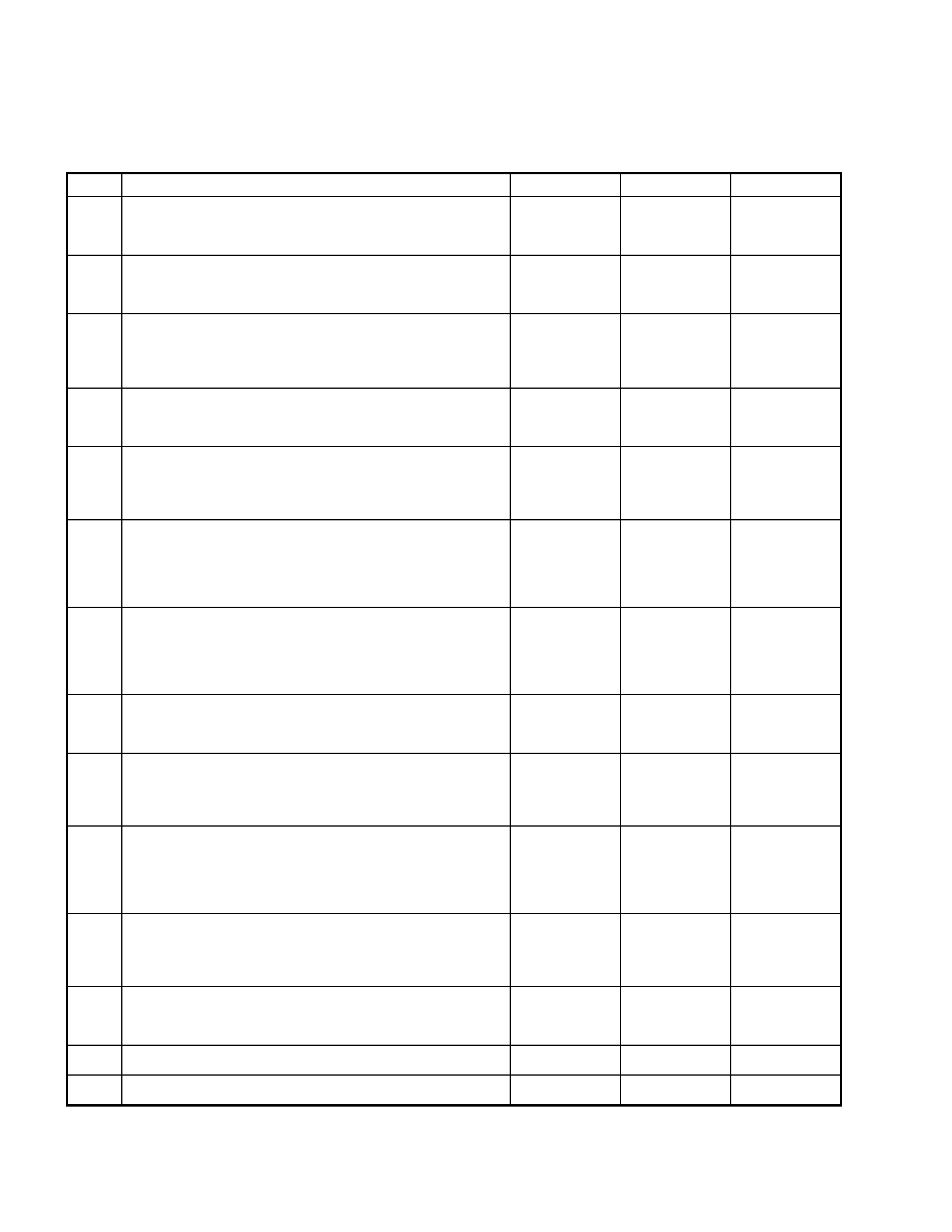
3. ENGINE COOLING SYSTEM DIAGNOSIS
3.1 ENGINE OVERHEATING
DEFINITION: Engine temperature lamp comes ON and stays ON, or the temperature gauge shows hot, or coolant
overflows from the surge tank onto the ground while the engine is running.
Step Action Value Yes No
1 1. Check for a loss of cool ant.
2. Ref er 2.2 COOLANT MAINTENANCE, Topping Up Cooling
System, in this Section.
Is there a l oss of coolant?
—
Refer 3.2 LOSS
OF COOLANT,
in this Section.
Go to Step 2
2 1. Check for weak engine coolant soluti on.
2. Ref er 2. 2 COOLANT MAINTENANCE, Testing Cool ant
Concentrat i on, i n this Section.
Does the engine still overheat?
—
Go to Step 3
System OK
3 Check for obst ructed radiator ai r flow or bent radiator fins.
2. I f necessary, rem ove or rel ocate added-on parts that block air
to the radiator. Clean away any insects, l eaves, or other
debris.
Does the engine still overheat?
—
Go to Step 4
System OK
4 1. Check for a loss of sys tem pres sure.
2. Conduc t a test on the pressure cap. Refer 2. 8 P RESSURE
TESTING, Screw-On Pressure Cap Testing, in thi s Section.
Does the engine still overheat?
—
Go to Step 5
System OK
5 1. Check for a faulty Engine Coolant Temperature (ECT) sensor.
Refer 6C3 POWERTRAI N MANAGEMENT - GEN III V 8
ENGINE, of the VT S e ri es II Servi ce Information.
2. Replace sensor as necessary.
Does the engine still overheat?
—
Go to Step 6
System OK
6 1. Check for a dam aged coolant surge tank.
2. Chec k for a leak i ng or kinked surge tank hose.
3. I f necess a ry, repl ace the surge t ank hose and/or repl ace the
coolant s urge tank. Ref er 2. 10 COOLANT SURGE TANK, in
this Section.
Does the engine still overheat?
—
Go to Step 7
System OK
7 1. Check the tens i on of the engine accessory dri ve belt.
Refer to 2.6 ENGINE ACCESSORY DRIVE BELT TENSION,
in this Section.
2. Replace the engine ac cessory dri ve belt as necessary. Ref er
to 2.7 ENGINE ACCESSORY DRIVE BELT, in this Section.
Does the engine still overheat?
—
Go to Step 8
System OK
8 1. Check for blocked cooling system passages.
2. Revers e flush the cooling system . Refer to 2.5 CLE A NING
THE COOLING SYSTEM, in this Section.
Does the engine still overheat?
—
Go to Step 9
System OK
9 1. Check for inco rrect or dam aged cooling fan blade(s).
2. Chec k for the correct f an bl ade(s) part num ber.
3. Replace fan/s as necessary. Refer 2.14 COOLING FANS AND
SHROUD ASSEMBLY, in this Section.
Does the engine still overheat?
—
Go to Step 10
System OK
10 1. Check for correct operation of cooling fans. Refer 6C3
POWERT RAIN MANAGEME NT - GE N III V 8 E NGINE,
of the VT Series II Service Inform ation.
2. Replace cooling fan/s and/ or motor, as necessary. Refer 2. 14
COOLING FANS AND SHROUD ASSEMBLY, in this Section.
Does the engine still overheat?
—
Go to Step 11
System OK
11 1. Check for correct thermostat operation. Ref e r 2. 9
THERMOSTAT, Test, in this Section.
2. Replace thermostat assem bl y as necessary. Refer 2.9
THERMOSTAT, in this Section.
Does the engine still overheat?
—
Go to Step 12
System OK
12 1. Check for correc t coolant pump operation.
2. Replace coolant pump ass embly as necessary. Refer 2.13
COOLANT PUMP, in this Section.
Does the engine still overheat?
—
Go to Step 13
System OK
13 1. Check the radiator cooling capacity.
Is the radi ator the correc t part for t he GE N III V 8 engi ne? —
System OK
Go to Step 14
14 1. Replace the radiator with t he correct part .
Is t he repai r complete? —
System OK —