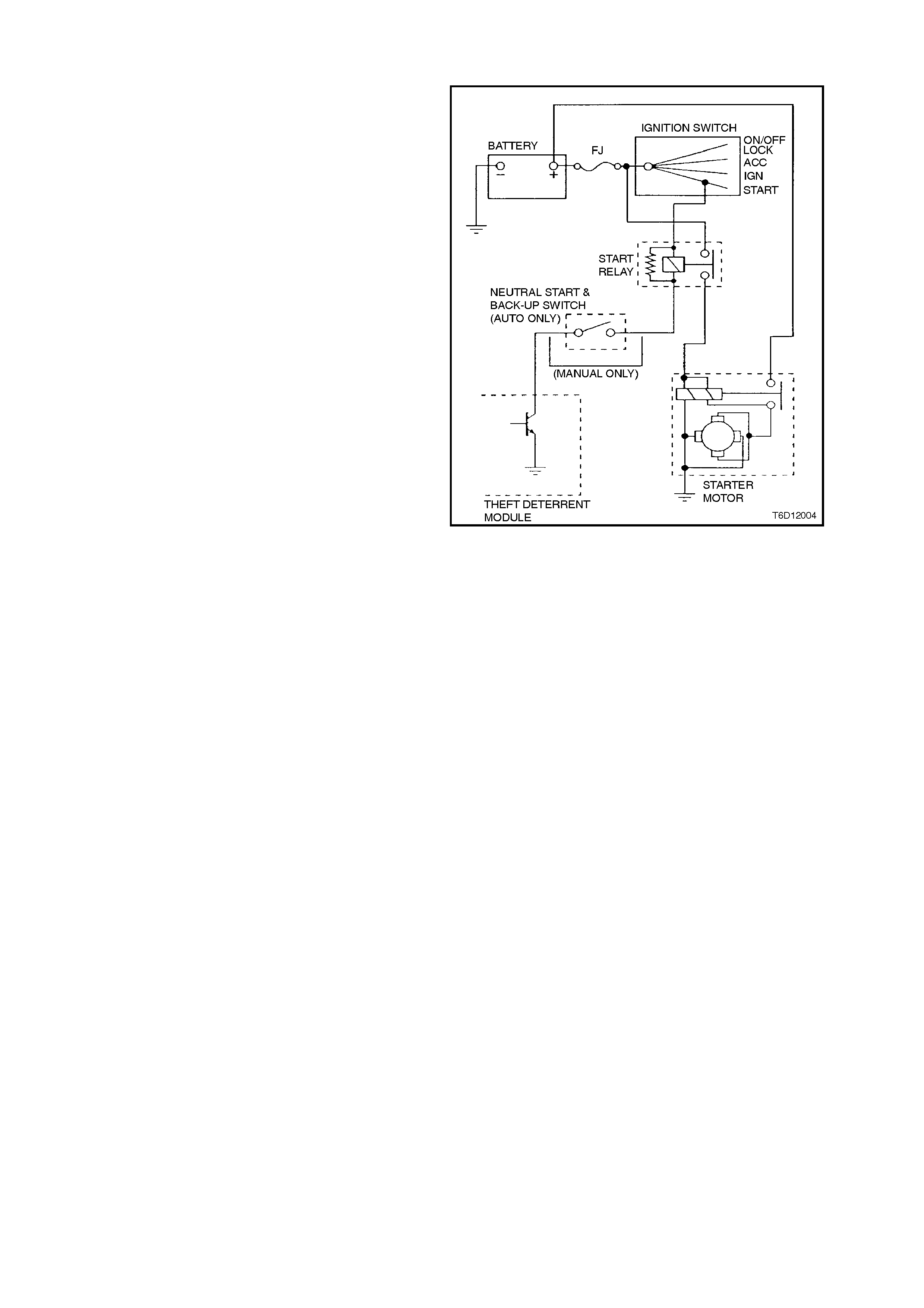
1.1 GENERAL DESCRIPTION
The starting system comprises the battery, starter
motor, ignition switch, neutral/back-up switch
(vehicles with automatic transmission), theft
deterrent engine crank inhibitor (function of theft
deterrent system) and related electrical wiring.
The starter motor is a series parallel wound, four
pole, four brush type with a planetary drive train.
The arm ature shaft is supported at each end by oil
absorbent sintered metal bushes pressed into the
commutator end cover and the inside of the
planetary drive shaft.
The planetary drive train comprises a ring gear
(made from a high-grade polyamide compound
with mineral additives) with gear teeth on the inside
diameter, three planetary gear wheels, a planetary
drive shaft and a cover plate. When assembled, the
planetary drive shaft, which is flanged at one end
with three shafts machined onto the flange, is
positioned on a sintered metal bus h in the ring gear
and secured by a washer and retaining clip. The
three gear wheels, each mounted on needle roller
bearings, are fitted onto the shafts on the flange of
the planetary drive shaft where they mesh with the
internal teeth of the ring gear. A lubricant
impregnated sintered metal bush is fitted into the
recess in the flanged end of the planetary drive
shaft to provide a mounting for the end of the
armature. The cover plate is positioned and
secured over the gear end of the assembly.
The drive assembly is installed onto the planetary
drive shaft, m eshed with the gear on the drive shaft
and secured to the shaft by a stop ring and ring
retainer. The combined assembly is installed into
position in the starter m otor drive end hous ing. The
planetary drive shaft is supported by a sintered
metal bush in the drive end housing, while the ring
gear is keyed to the drive end housing, providing
positive and sec ure m ounting of the dr ive s haft and
drive assembly.
When the starter motor is assembled, the teeth of
the gear on the armatur e shaft m esh with the teeth
on the three planetary gears wheels. When the
starter motor is operated, drive from the armature
causes the planetary gear wheels to rotate, caus ing
the gear wheels to revolve around the inner
diameter of the ring gear. This action causes the
planetary drive shaft to rotate and impart drive into
the drive assembly. During operation of the starter
motor the armature r otates the drive assem bly at a
reduced speed of approximately 3.36:1.
The s intered m etal bearings require lubric ation only
at the time of an overhaul.
Figure 6D1-2-2
The four brushes are supported by the brush holder which is retained to the commutator end cover by screws.
Two brushes ar e grounded to the f ield c oil hous ing, and two are insulated f r om the housing and c onnec ted to the
field coils. The field coils are held in place by the pole shoes which are attached to the f ield coil housing by large
diameter screws. The field coils are connected to an insulated terminal on the field coil housing through which
current is supplied to the starter motor from the solenoid switch.
On the drive end housing, a plas tic for k with plastic bearing bloc k is used to engage the drive as sembly with the
flexplate/ring gear.
The drive assembly transmits cranking torque to the flexplate/ring gear. To prevent the armature from being
driven at exces sive speed by the engine, an internal clutch allows the drive ass embly pinion gear to rotate f reely
in relation to the planetary shaft and armature when the engine begins to operate.