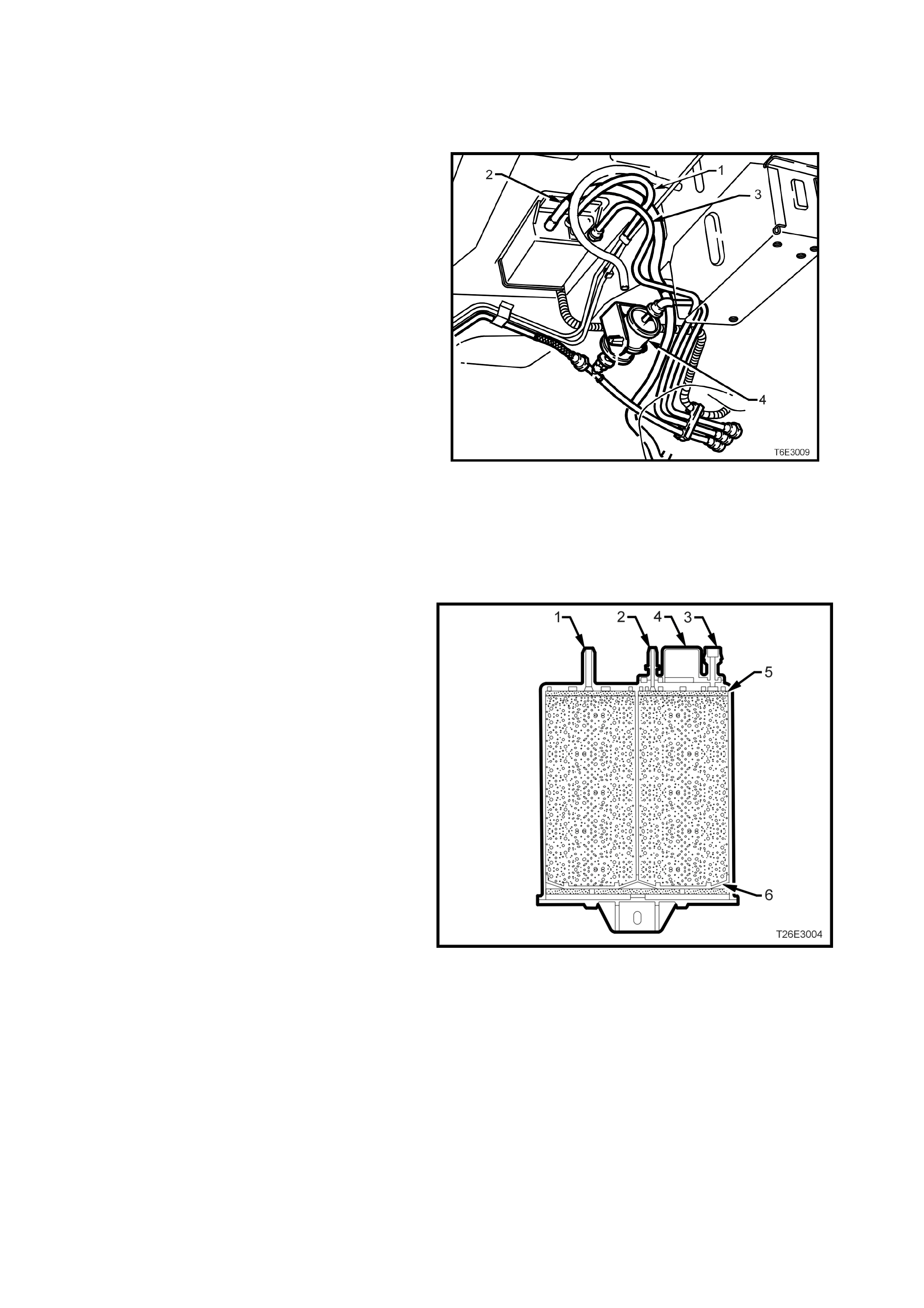
The c anister (loca ted under th e rear of the veh icle)
cannot be repaired, and is serviced only as an
assembly. Periodically check the canister at the
time or distance intervals specified in the vehicle
Series Owners Handbook.
The fuel vapour canister is mounted in a bracket
underneath the vehicle, near the fuel filter (4).
This canister is a three port design. The fuel
vapour is absorbed by the charcoal within the
canister. When the engine is running at idle speed
and above idle, air is drawn into the canister
through the air vent line (2) (atmospheric port) at
the top of the canister assembly.
The air m ixes with the fuel vapour and the mixture
is drawn into the intake manifold via the canister
purge line (1). Pur g in g of the ca nis ter v ia t his l in e is
controlled by a PCM controlled EVAP canister
purge valve. The EVAP canister purge valve
controls the manifold vacuum signal from the
throttle b ody. The remaining l in e i nto t he c a nis ter is
the vapour inlet f rom the f uel tank (3). T he f resh air
inlet port (2) (air vent port) on the canister is open
to the atmosphere via a hose that vents under the
vehicle. Figure 6E3-9
Legend
1. Canister Purge Port
2. Air Vent Por t
3. Vapour from Fuel Tank Port
4. External Fuel Filter
RESULTS OF INCORRECT OPERATION
Poor idle, stalling and poor driveability can be
caused by:
• Inoperative EVAP canister purge valve.
• Damaged canister.
• Hoses split, cracked and/or not connected to
the
correct locations.
• Throttle body and canister hoses interchanged
on the EVAP canister purge valve connections.
NOTE: The canister connection is marked with
"CAN".
Evidence of fuel loss or fuel vapour odour can be
caused by:
• Liquid fuel leaking from fuel lines.
• Cracked or damaged canister.
• Disconnected, misrouted, kinked, deteriorated
or damaged vapour hoses, or control hoses.
If the EVAP canister purge valve is stuck open, or
the control circuit is shorted to earth the canister
will purge to the intake manifold all the time. This
can allow extra fuel at idle or during warm-up,
which can cause rough or unstable idle or a rich
fuel operation.
If the canister purge solenoid is always closed, the
canister can become over loaded, with noticeable
fuel odour being evident.
Figure 6E3-10
Legend
1. Air Vent Por t
2. Canister Purge Port
3. Vapour from Fuel Tank Port
4. Evaporative Canister
5. Volume Compensator
6. Charcoal Bed