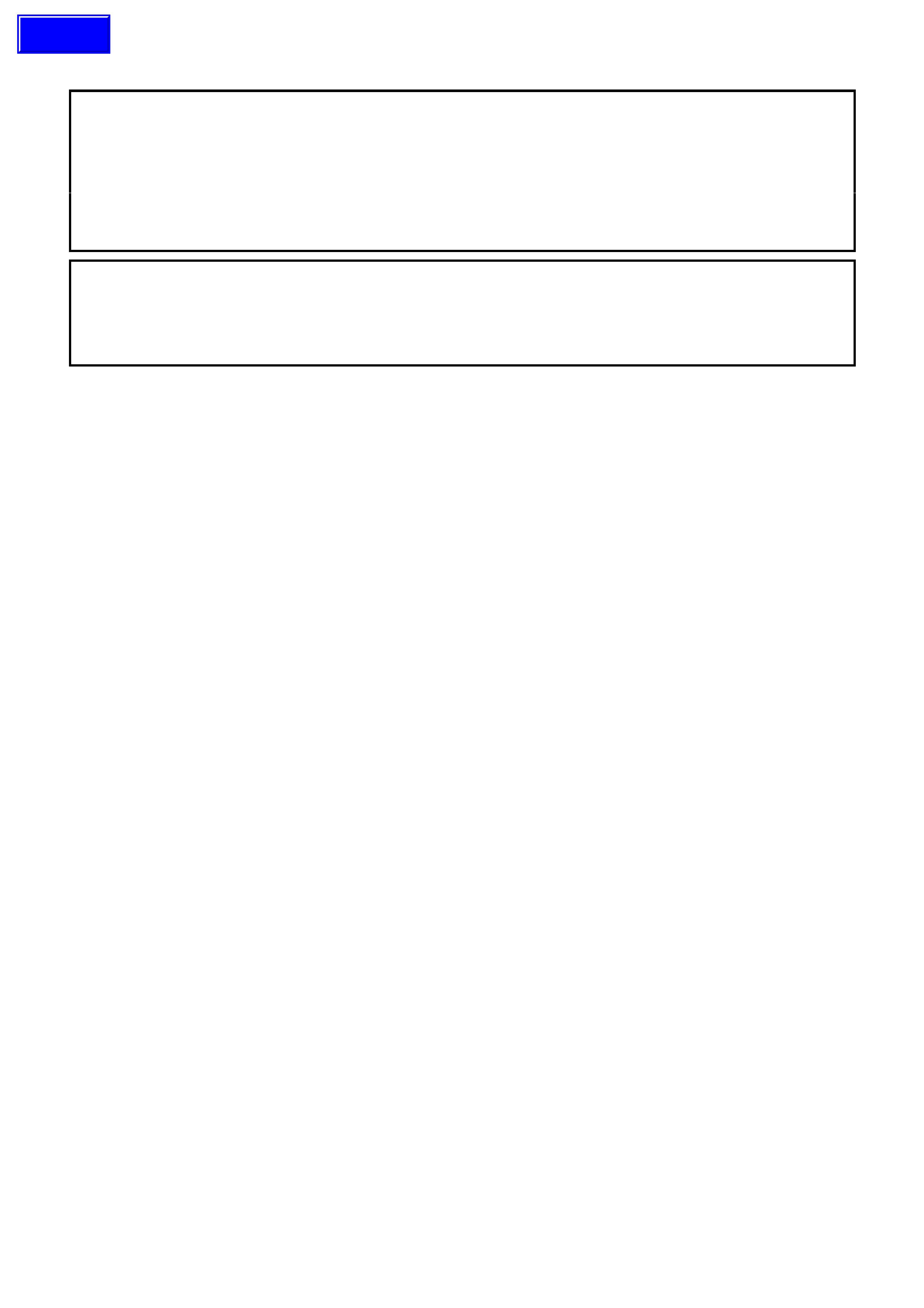
SECTION 8A - FUEL TANK
CAUTION:
This vehicle will be equipped with a Supplemental Restraint System (SRS). A SRS will consist of either
seat belt pre-tensioners and a driver's air bag, seat belt pre-tensioners and a driver's and front
passenger's air bags or seat belt pre-tensioners, driver’s and front passenger’s air bag and left and right
hand side air bags. Refer to SAFETY PRECAUTIONS, Section 12M, Supplemental Restraint System of
this Service Information CD before performing any service operation on, or around any SRS
components, the steering mechanism or wiring. Failure to follow the SAFETY PRECAUTIONS could
result in SRS deployment, resulting in possible personal injury or unnecessary SRS system repairs.
CAUTION:
Whenever any component that forms part of the ABS or ABS/ETC (if fitted), is disturbed during Service
Operations, it is vital that the complete ABS or ABS/ETC system is checked, using the procedure as
detailed in 4. DIAGNOSIS, ABS or ABS/ETC FUNCTION CHECK, in Section 12L ABS & ABS/ETC, in either
VT Series I Service Information (V6) or VT Series II Service Information (GEN III V8).
1. GENERAL INFORMATION
Apart from the deletion of the external vent pipe that occurred shortly after the start of production and the deletion of
the under-tank reinforcement plate, the fuel tank and related components for both V6 engines remains unchanged.
For service operations relating to the fuel tank on V6 engined, VT Series vehicles, refer to Section 8A FUEL TANK,
in the VT Series I Service Information. This Section then, will only detail the changes made to the fuel system as
they apply to the GEN III V8 engine.
The fuel system used with the GEN III V8 engine is a ‘single line’ system, which means that the previously used fuel
return line from the engine fuel rail, is no longer used.
A changed design, modular fuel sender assembly is located in the fuel tank, that incorporates a fuel pressure
regulator, a fuel reservoir, the fuel sender unit, roll-over valve and the fuel pump in the one modular unit.
Apart from the complete assembly, the only other serviced component in the modular fuel sender is the fuel sender
assembly.
Quick-connect fuel line fittings are used for all fuel line connections, including the modular fuel sender assembly,
fuel vapour canister, fuel filter, fuel feed line T-piece and at both the engine and fuel tank ends.
1.1 GEN III V8 ENGINE MODULAR FUEL SENDER OPERATION
The fuel control system used on the GEN III V8 is a “Returnless” or “Demand” system. The fuel system starts with
the fuel in the fuel tank. A single in-tank high pressure fuel pump with an integrated fuel pressure regulator (located
inside a modular fuel sender assembly) is used. From the high pressure pump, fuel flows through a fuel filter, then
back into the fuel tank via the fuel pressure regulator. Fuel is supplied to the fuel rail and injectors by a single feed
fuel line.
The high pressure in-tank single pump is capable of providing fuel at more than 410 kPa. A pressure regulator in
the modular fuel sender assembly maintains the fuel pressure at a regulated pressure of 410 kPa.
The fuel pump is energised by the PCM via the fuel pump relay The injectors, located in each runner of the intake
manifold just ahead of the inlet ports to the cylinder head, are controlled by the PCM.
System Components
The Fuel Control System is made up of the following components (refer Fig. 8A-1):
• PCM
• Fuel Tank
• Modular fuel sender assembly, containing;
• Fuel pump assembly
• Fuel pressure regulator
• Fuel filter
• Fuel pressure supply line
• Fuel pump relay
• Fuel rail
• Injectors