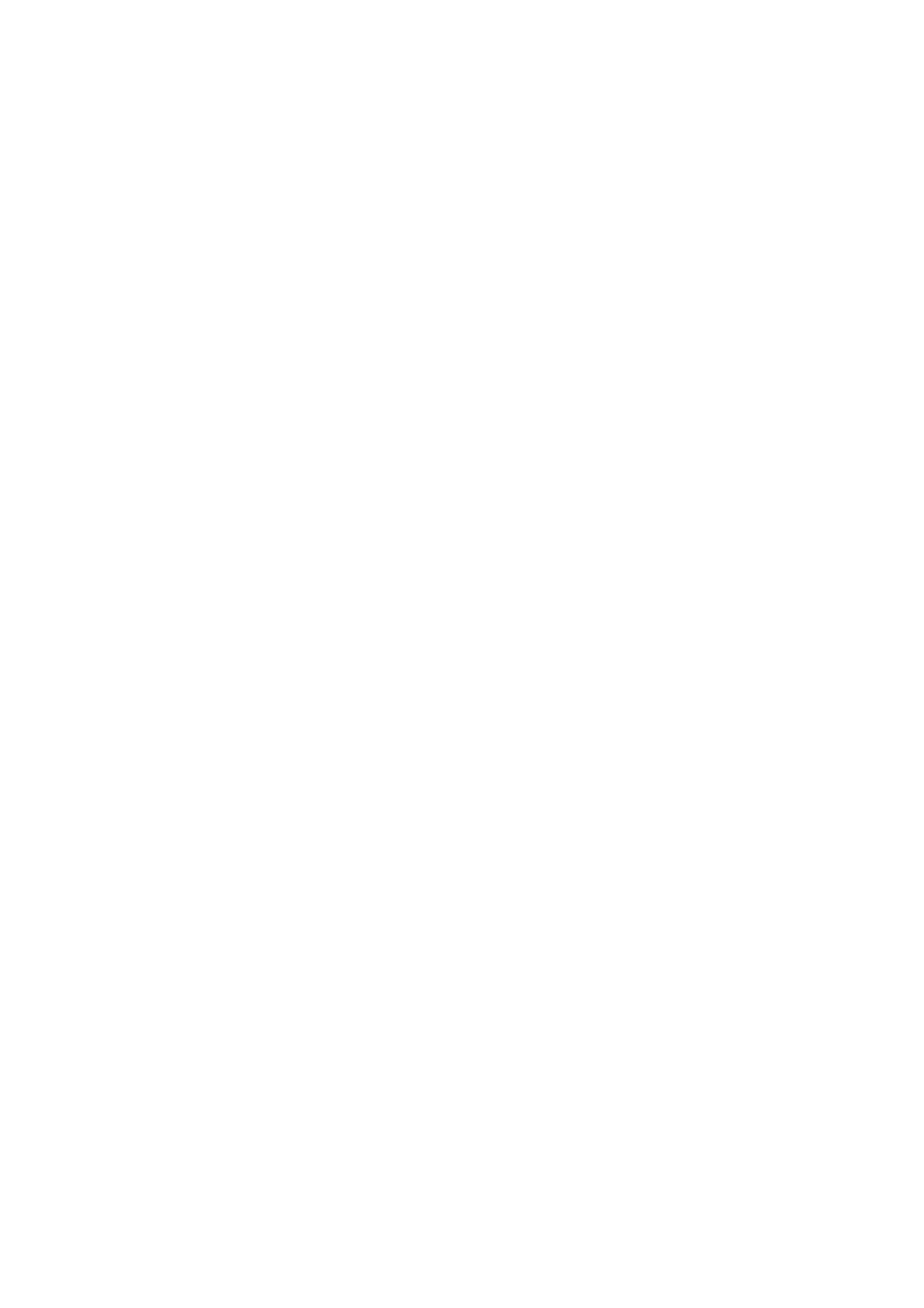
2.4 BODY STRUCTURE PANELS
UNDERBODY
Listed below are assemblies and individual panels
that are available for replacement.
The purpose of these illustrations is to provide the
repairer with a better understanding of available
replacement panels.
1. Panel assembly – floor side
2. Reinforcement assembly – inner seat
attaching.
3. Reinforcement – front seat outer attaching.
4. Floor assembly – front.
5. Bracket – footrest.
6. Mount assembly – power unit rear.
7. Extension assembly – floor panel front.
8. Brace – longitudinal to front floor.
9. Panel assembly – front fender skirt.
10. Bracket assembly – anti theft horn mounting,
LH.
11. Bracket assembly – hydraulic modulator.
12. Tray assembly – battery.
13. Panel assembly – front.
14. Panel assembly – front upper.
15. Panel assembly – front headlamp.
16. Bracket assembly – side panel front end.
17. Bracket assembly - fender.
18. Member assembly – front lower.
19. Longitudinal assembly - complete.
20. Bracket – radiator support side.
21. Support assembly – front panel side.
22. Bracket – front bumper beam mounting.
23. Console – front panel.
24. Crossmember assembly - centre.
25. Reinforcement – floor panel side.
26. Carrier plate assembly.
27. Hook assembly – tie down.
28. Bracket – rear brake hose.
29. Extension assembly – longitudinal rear.
30. Rear longitudinal – complete.
31. Crossmember assembly – rear.
32. Support – spare wheel lateral, LH.
33. Crossmember – rear floor, LH.
34. Support – spare wheel longitudinal.
35. Support – spare wheel longitudinal.
36. Member assembly – hoist longitudinal.
37. Support – spare wheel lateral, RH.
38. Crossmember – rear floor, RH.
39. Panel – rear end inner.
40. Reinforcement assembly – endgate hinge mounting.
41. Panel – rear end outer.
42. Reinforcement – tonneau floor to wheelhouse.
43. Floor assembly – tonneau rear.
44. Bracket assembly – fuel tank mounting.
45. Floor assembly – tonneau front.
46. Bracket assembly – fuel vapour canister mounting.
47. Panel assembly – floor rear.
48. Support – intermediate heat shield.
49. Reinforcement assembly – centre bearing.
50. Support – pressure hose.
51. Bracket assembly – fuel tank mounting.
52. Reinforcement – seatback panel lower.
53. Panel assembly – rear seatback lower.
NOTE: Where a side is specified, part is fitted to that side only