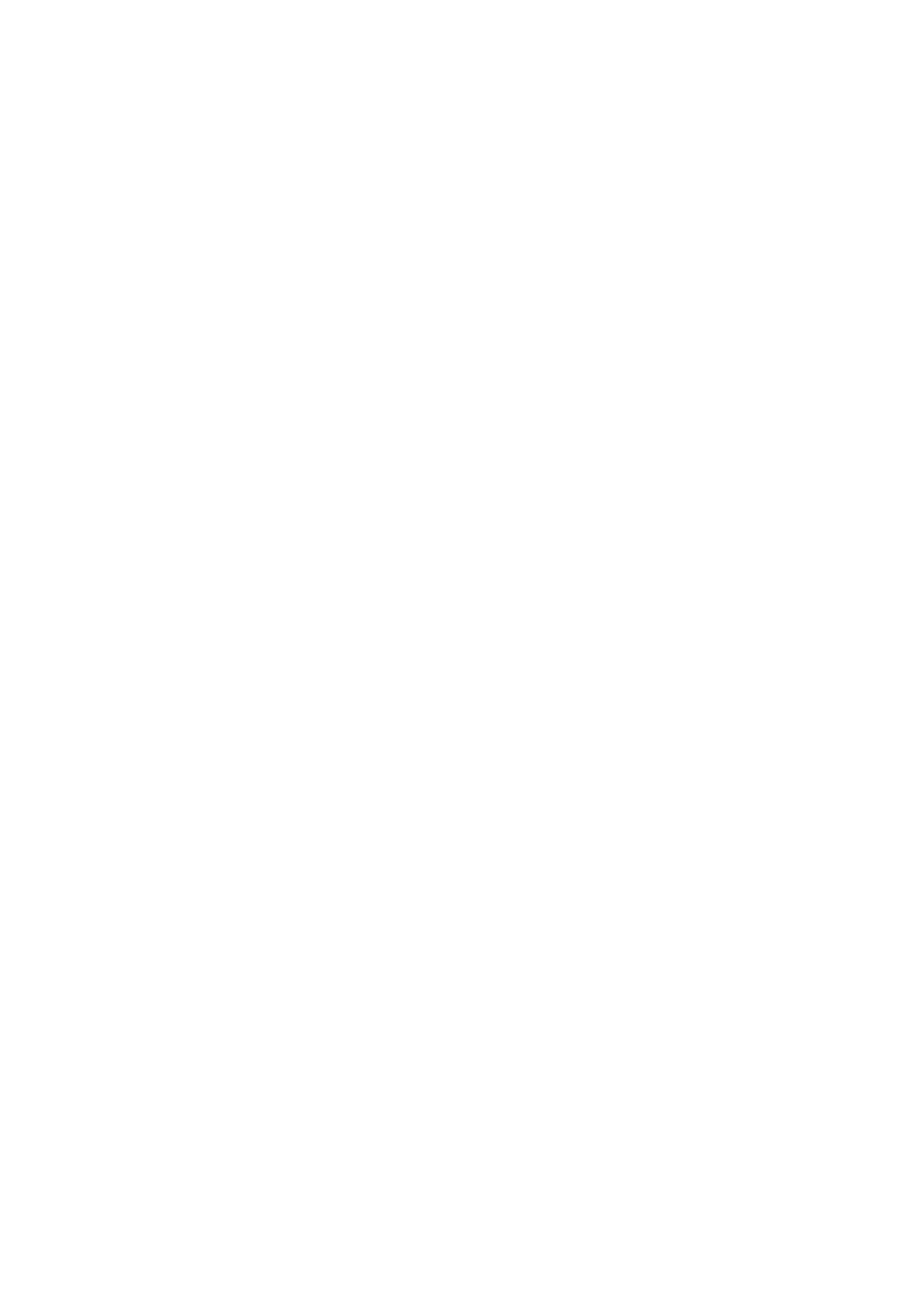
A/C Test (MI, LO): In this mode, Tech 2 commands the BCM to switch the A/C on/off switch LED on and off.
Low Fan (ALL): In this mode, Tech 2 commands the BCM to switch ON and then OFF, (will switch OFF
automatically after a short period provided the PCM is not commanding the low fan on) the engine cooling low
speed fan relay.
Data Bus Isolator (ALL): In this mode, the BCM data bus isolator switch can be opened or closed.
To check if the data bus isolator is operating, while commanding the data bus isolator open with Tech 2, start
engine and monitor the trip com puters “ins tant fuel consum ption” display while varying the engine speed. W hen the
data bus isolator switch is opened, the trip computers instant fuel consumption display will not update.
NOTE: The data bus isolator will only be held open for five seconds.
Central Lock ing (ALL): In this mode, Tech 2 commands the BCM to operate all door lock actuators.
Heated Rear Window (MI, LO): In this m ode, the rear window dem ister can be tur ned on and off. W hen s witched
on, the heated rear window switch LED is illuminated and the relay can be heard to operate.
Wiper Tests (ALL): If Wipers are s elec ted, an additional applic ation menu will be displayed offer ing extra func tional
tests of the vehicles wiper system.
Front Wipers (ALL): In this mode, the front windshield wipers can be driven ON and OFF.
Rear Wipers (HI, LU, MI): In this mode, the rear screen wipers can be driven ON and OFF.
Window Down (HI, LU, MI): In this mode, the driver’s window can be driven down.
NOTE: Before entering and conducting this test, ensure that driver's side power window is fully up.
Antenna (HI, LU): In this mode, Tech 2 commands the BCM to raise or lower the antenna.
Horn (HI, LU): In this mode, the horn can be switched ON.
Power Steering (HI): In this test, Tech 2 commands the BCM to vary the current flow through the power steering
solenoid, thereby varying the amount of power steering assist.
Power Window Relay (HI, LU, MID): In this mode, Tech 2 commands the BCM to turn off the power window relay.
Illumination Drive Relay (ALL): In this mode, Tech 2 commands the illumination drive relay on or off.
Security System (ALL): If the security system mode is selected, an additional application menu will be displayed
offering additional functional tests of the vehicles security system.
Security LED (ALL): In this mode, Tech 2 commands the BCM to turn the theft deterrent alert indicator LED
ON and OFF.
Boot Release (ALL): In this mode, Tech 2 commands the BCM to activate the sedan rear compartment lock
actuator.
Theft Horn (HI): In this mode, the theft deterrent horns can be switched ON.
Key Priority (HI): In this m ode, the priority key status can be switched fr om priority one to pr iority two or priority
two to priority one.
Alarm Output (MI, LO, Not AL): In this m ode, the alarm st atus output can be s witched on or off (this feature is
for an after market alarm system).
Alarm Horn: (AL): In this mode, the theft deterrent horn can be switched ON.
F5: Program
In this test mode, T ec h 2 allows the progr amm ing of var ious f eatur es by turning the feature OFF or ON, or adjusting
settings (ie. twilight sentinel sensitivity).
In this test mode, T ec h 2 allows the progr amm ing of var ious f eatur es by turning the feature OFF or ON, or adjusting
settings to suit individual owner requests.
To operate any of the programming features, simply select the appropriate function to be changed from the
Program Application Menu and follow the instructions as per Tech 2.
When the Program option is selected, the following choices will become available.
Rear Wiper Control (HI, LU, M I): In this mode, the rear wiper intermittent c ontrol c an be dis abled. By disabling this
feature, it will prevent the rear wiper continuously sweeping the tailgate screen when the front intermittent wiper is
activated and reverse gear is selected.
Antenna Height Memory (HI, LU): In this mode, the antenna height m emory can be switched off, resulting in the
antenna mast fully extending each time the radio is switched on.
Two Stage Unlocking (ALL): In this mode, the two stage door unlock feature (one press of remote coded key
unlock button will unlock the driver’s door only, a second press will open all doors) can be disabled, thus enabling
single stage unlock (one press of remote coded key unlock button will unlock all doors).
Set Key to Priority 1 (HI): In this mode, the priority key in the ignition switch can be set to become priority one.
Tw ilight Sentinel (HI): In this mode, the s ensitivity of the twilight sentinel c an be adjusted from 0 to 7. All vehicles
will have the twilight sentinel set to a def ault value of 4. If the driver requests the lights to com e on latter (when it is
darker), the sensitivity of the twilight sentinel should be adjusted down (towards 0). If the driver requests the lights to
come on earlier (when it is lighter), the sensitivity of the twilight sentinel should be adjusted up (towards 7).
Battery Saver Shutdown Time (ALL): In this mode the battery saver shutdown mode time can be changed to
switch off after 2 minutes to 255 minutes.