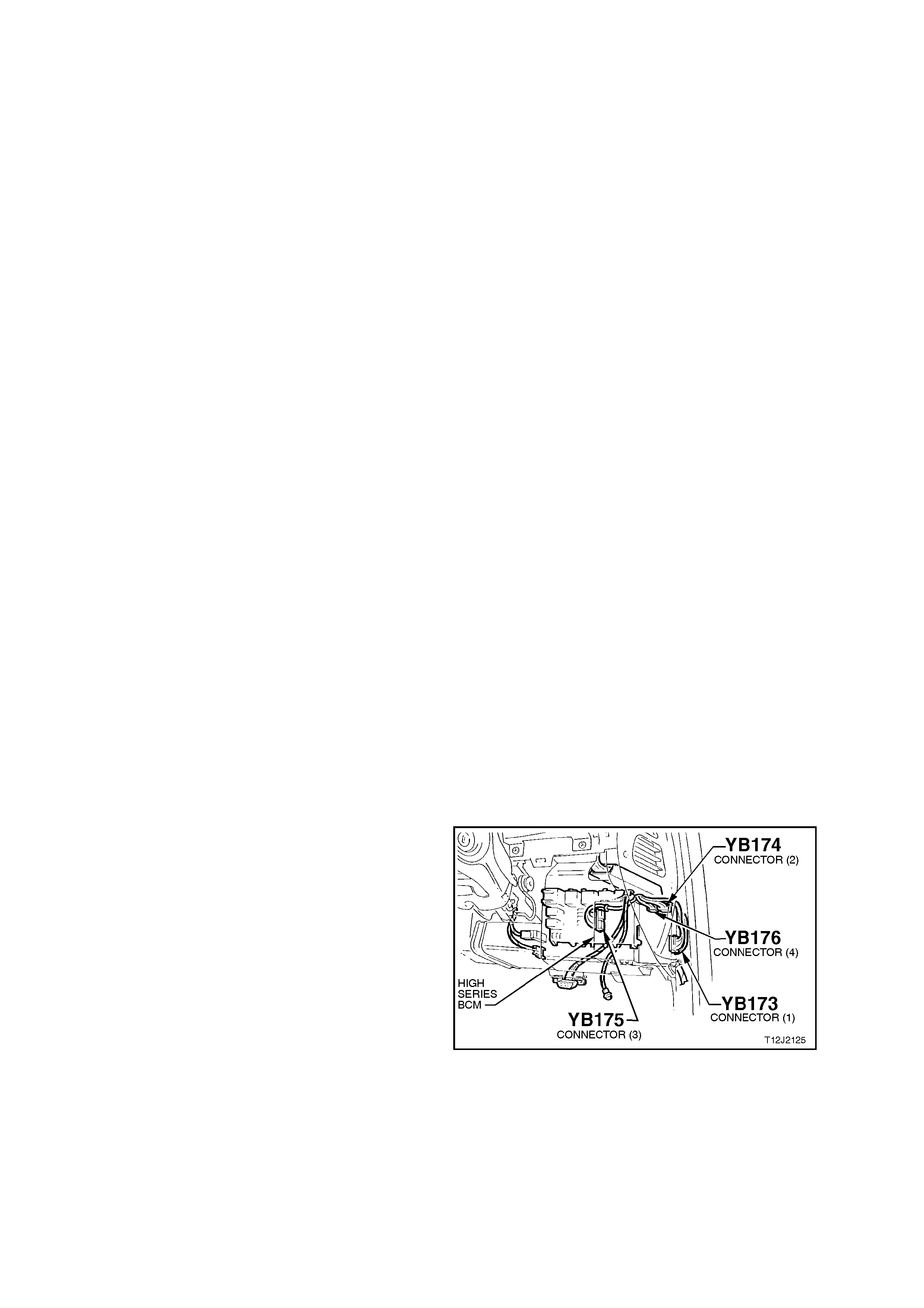
CIRCUIT DESCRIPTION
Automatic lights ON and OFF (High Series BCM
only)
The automatic light c ontr ol, lights on and of f featur e
with twilight sentinel, turns the vehicle headlights on
and off, depending on the outside light level. This
feature will only work while the headlamp switch is
in the AUT O position and the ignition switched ON.
The lights will operate as normal in other switch
positions.
The light sensor is part of the sun sensor / remote
receiver module and is located in the instrument
panel pad of the vehicle between the dem ist ducts.
The light sensor is used to monitor the amount of
light in front of the vehicle. The BCM monitors the
output of this sensor via circuit 272 (terminal E10)
and determines when the light levels are low
enough to turn the lights on.
TECH 2 can be used to select several different
ON/OFF light levels to suit the customer
preferences. The automatic lights off feature works
as per normal (automatic lights off without twilight
sentinel) during automatic light control (including
auto lights off delay period).
Approach illumination (Lux and High Series
BCM)
The approach illumination feature turns the vehicle
head and/or park lamps on (dependant on
headlamp switch position) f or 30 s econds when the
doors are unlocked with the remote coded key.
This provides additional customer security when
approaching the vehicle at night. T he lights will turn
off again if the vehicle is locked with the remote
coded key within 30 seconds of the approach
illumination being activated.
When the approach feature is activated,
subsequent operation of the remote coded key
unlock button will reactivate the lights to remain on
for a further 30 seconds.
The approach illumination feature only operates
during dark conditions. The BCM monitors the
output of the sun sensor and determines when the
light levels are low enough to enable the approach
illumination feature.
The lights resume to normal operation when the
ignition is switched to the on position.
TECH 2 has the capability to enable and disable
the approach illumination feature.
DIAGNOSTIC AIDS
If a driver com plains of the headlam ps com ing on to early
(during daylight), or too late (well after dusk), the
sensitivity of the twilight can be program med using TECH
2.
By adjusting the sensitivity down (below the default value
of 4) the headlamps will turn on latter.
By adjusting the sensitivity up (above the default value of
4) the headlamps will switch on earlier.
NOTE: Sensitivity range is 0 – 7, if the TECH 2 operator
selects a sensitivity level of 8 or 9, the value will default to
0.
TEST DESCRIPTION
The num ber s below refer to step num bers in the following
diagnostic chart.
1-5. Functional check of automatic light control system.
6. Uses TECH 2 to operate headlights in the AUTO
position to establish whether problem is with input or
output of BCM.
7. Checks for power and earth to sun sensor / remote
receiver module.
8. Uses TECH 2 to check LIGHT SENSOR LEVEL
signal at microprocessor of BCM.
9. Checks for BCM output drive of AUTO LIGHTS ON.
10. Checks circuit 308.
11. Checks for battery voltage supply at sun
sensor/remote receiver module (circuit 740).
12. Checks circuit 271.
13. Checks LIGHT SENSOR LEVEL signal at input to
BCM.
14. Checks and defines fault of circuit 272.
15. Uses TECH 2 to turn headlights off in the AUTO
position to establish whether pr oblem is with output or
input of BCM.
16. Checks LIGHT SENSOR LEVEL signal at input to
BCM.
17. Tests for false output drive from BCM or short circuit
in wiring.
Figure 12J-2-16