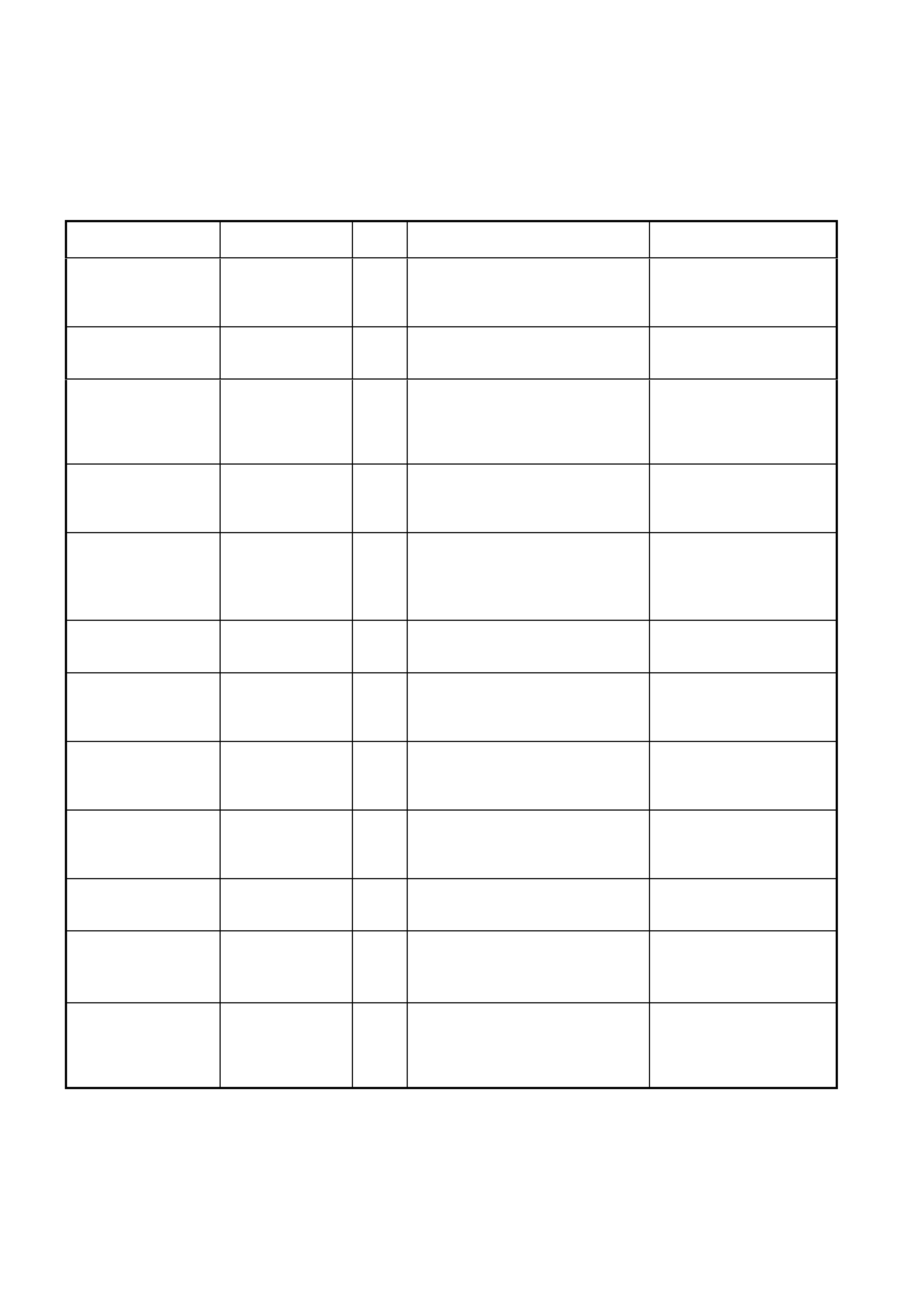
F0: DATA DISPLAY
F0: Data List
In this test mode, Tech 2 checks if the telematics module is actually receiving an input or inputs from the
appropriate sensor/s or antenna/s. If the sensor/s or antenna/s input/s are not being received, then carry out the
relevant system diagnosis as defined in the following chart.
Typical data list parameter nominal values, relevant telematics module pin number and specific diagnostic charts
are detailed in the following chart. If the actual data does not match the nominal value, then refer to the specific
diagnostic chart for that data parameter.
Data Parameter Display Pin No Nominal Values Diagnostic
Chart
Battery Voltage VOLTS 1 Should be within 0.5 volts of actual
vehicle battery voltage. Refer
Vehicle Battery Voltage
Diagnostic Chart in this
Section.
Backup Battery
Voltage Volts 13, 26 Backup Battery Voltage, should be
greater than 11.5 volts. Refer Backup Battery
Diagnostic Chart, in this
Section.
Backup Battery
Charger Active / Inactive 13, 26 Backup Battery Charger, will display
Active when the telematics backup
battery is being charged via the
telematics backup battery charging
circuit.
Refer Backup Battery
Diagnostic Chart in this
Section.
Ignition Switch On / Off SD Ignition Switch status, as read from
the serial data circuit normal mode
message. Should display On when
the ignition switch is on.
Refer No Serial Data
Diagnostic Chart in this
Section.
Operating Mode Pre-Delivery
Active
Service
Int Telematics module Operating Mode.
When the system is operating, should
display Active.
Refer 2.15 OPERATING MODES in
this Section for further information.
Refer
4.3 TECH 2 TEST MODES
F4: Program, F2: Operating
Mode, in this Section.
GPS Module Inactive / Active Int GPS Module status, should di splay
Active when the GPS engine is
operational.
Refer No GPS Signal
Diagnostic Chart in this
Section.
GPS Antenna Status Okay
Open Circuit
Short Circuit
Int Displays GPS antenna circ uit status,
should display Okay.
If Open Circ uit or Short Circuit is
displayed refer to diagnostic chart.
Refer No GPS Signal
Diagnostic Chart in this
Section.
2D or 3D GPS
Position Fix No / Yes Int Will display YES in the GPS has a 2D
or 3D satellite position fix. Will vary
depending upon vehicle and satellite
locations and time of day.
Refer No GPS Signal
Diagnostic Chart in this
Section.
GPS Satellites Not Visible /
Visible Int Should displa y Visible when at least
one GPS satellite has been detected.
Will vary depending upon vehicle and
satellite locations and time of day.
Refer No GPS Signal
Diagnostic Chart in this
Section.
GSM Module Active / Inactive Int Should display Active if GSM Module
is active and registered on the mobile
phone network.
Refer No GSM Signal
Diagnostic Chart in this
Section.
GSM Signal Strength NO SIGNAL OR 1 -
32 Int GSM Signal Strength, will vary from
1 – 32 depending on vehicle position
and GSM coverage. If No Signal is
displayed refer to diagnostic chart.
Refer No GSM Signal
Diagnostic Chart in this
Section.
SPEAKER VOLUME 1 - 8 11, 24 The speaker volume can be
programmed using Tech 2, 1 being
the quietest, to 8 being the loudest.
This displays the current speaker
volume setting.
Refer
4.3 TECH 2 TEST MODES
F4: Program, F1: Speaker
Volume Adjustment in this
Section.
SD = Serial Data, Int = Internal Telematics Module Value