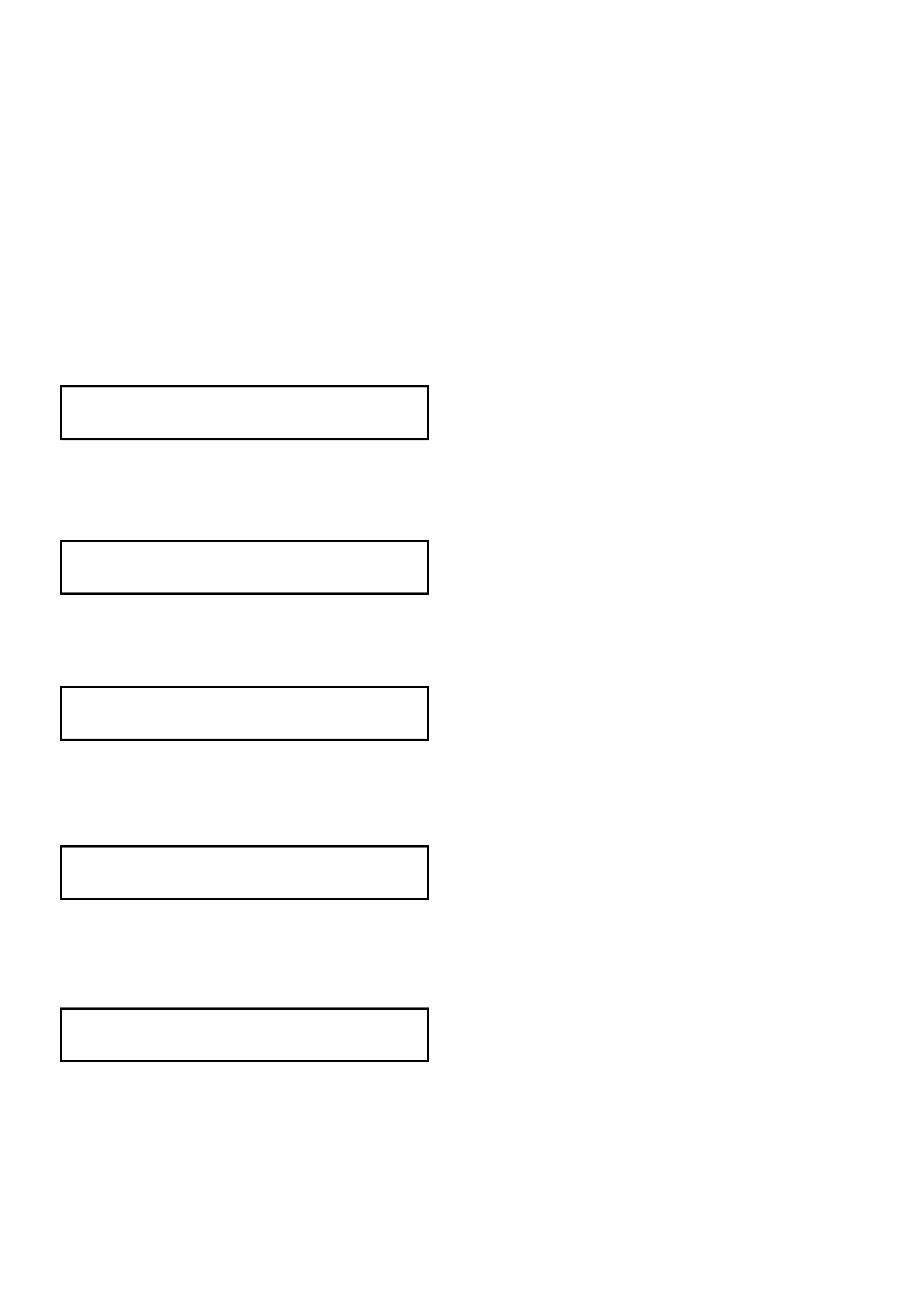
REINSTALL
Reinstallation is the r everse of rem oval proc edures
noting the following:
GENERAL PROCEDURE:
1. Lubricate both the trans m ission output shaf t (V6 engine and m anual tr ansm ission) and final drive pinion spigots
with molybdenum disulphide grease to Holden Specification HN1271.
2. For those VX models with a sliding front yoke, remove any foreign matter that may have adhered to the front
universal joint yok e and lubricate with tr ans mission lubricant. Ins er t yoke on to trans mission m ains haf t, index ing
the splines.
3. Clean threads of centre bearing carrier to underbody reinforcement bolts and underbody weld nuts.
4. Reinstall the front of the propeller shaft assembly first, supporting the centre and rear sections.
5. While still supporting the centre bearing area, slide the propeller shaft assembly forward to allow engagement of
the rear spigot, then slide rearward to fully engage.
6. Raise the centre bearing assembly and reinstall the bolts and washers to secure to the underbody
reinforcement. Tighten both bolts to the correct torque specification.
CENTRE BEARING CARRIER TO
UNDERBODY REINFORCEMENT 20 – 35 Nm
BOLT TORQUE SPECIFICATION
7. Before reinstalling the attaching bolts and washers to the propeller shaft rear coupling and pinion flange, align
marks on pinion flange and rear coupling (or marks made on removal), refer to Fig. 4C-8.
8. Provided no thread damage is evident, reinstall the original rear propeller shaft coupling to final drive pinion
flange bolts and washers, tightening to the correct torque specification.
PROPELLER SHAFT REAR
COUPLING TO PINION FLANGE 105 – 125 Nm
BOLT TORQUE SPECIFICATION
VX MODELS WITH V6 ENGINE AND MANUAL TRANSMISSION
9. Install NEW r ubber coupling to transm ission output flange retaining nuts bef ore tightening to the correct tor que
specification.
RUBBER COUPLING TO TRANSMISSION
OUTPUT SHAFT FLANGE RETAINING 50 – 85 Nm
NUT TORQUE SPECIFICATION
10. Reinstall the exhaust system as follows;
V6 ENGINED MODELS (MANUAL TRANSMISSION ONLY)
a. Reinstall the twin exhaust pipes to the exhaust manifolds, then reinstall the retaining nuts and tighten the
nuts to the specified torque.
EXHAUST PIPE FLANGE TO
EXHAUST MANIFOLD NUT 18 – 35 Nm
TORQUE SPECIFICATION
b. Reinstall the support rubber to the transmission mount bracket post.
c. Reconnect both wiring harness connectors to the oxygen sensors.
d. Check that the catalytic converter to intermediate exhaust pipe bolts, springs and sealing ring are all in a
serviceable c ondition. Reinstall the sealing ring, springs and bolts , tightening the bolts to the cor rect torque
specification.
INTERMEDIATE EXHAUST PIPE
TO CATALYTIC CONVERTER 40 – 50 Nm
BOLT TORQUE SPECIFICATION