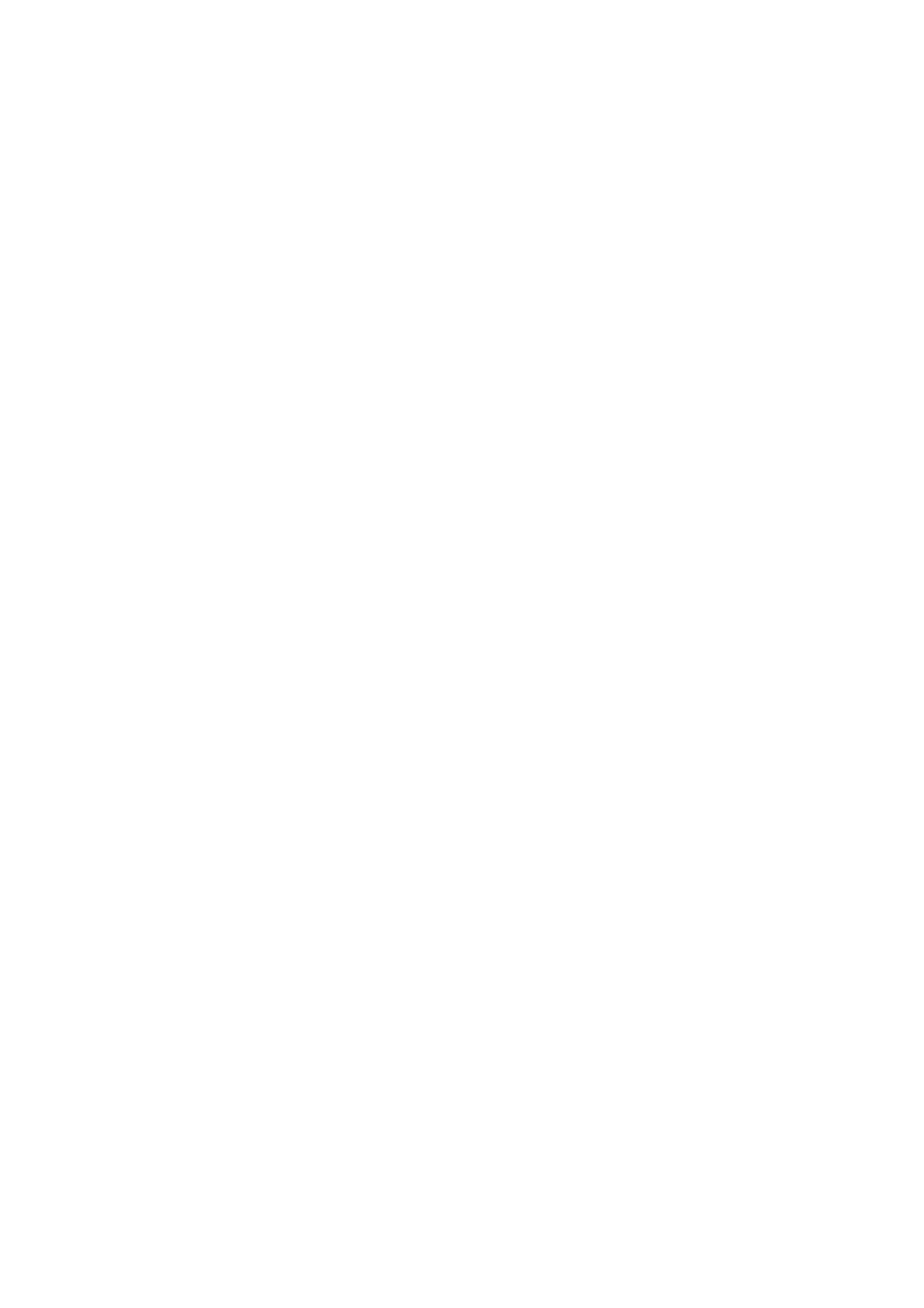
Ignition Module Bypass Control circuit, causing the ignition module to allow the PCM to operate the ignition
system.
D10 - ELECTRONIC SPARK TIMING (EST) OUTPUT
This terminal will have very low voltage with the ignition "O N" but engine not running. W ith the engine r unning at
idle, the voltage should be slightly more than 1 volt. As the engine RPM goes up, this voltage will increases.
D11 - CRANKSHAFT REFERENCE INPUT SIGNAL LOW
This terminal should always be zero volts. It is connected through the ignition module to engine earth.
D12 - 3X CRANKSHAFT REFERENCE INPUT SIGNAL HIGH
This terminal could be called the "tach" input. It provides the PCM with RPM and crankshaft position
information. With ignition "ON" but engine not running, the voltage will be either high or low, depending on
crank shaft position. As the crankshaft turns, the voltage will be an average of the two readings. The PCM uses
the 3X signal to control fuel injection, and spark timing with engine speeds above 1200 RPM. (See 18X
crankshaft reference terminal D4)
D13 - OXYGEN SENSOR INPUT SIGNAL
- RIGHT BANK -
W ith ignition "ON" and engine not running, the voltage should be 350 - 450 millivolts (0.350 - 0.450 volts). This
is the PCM-supplied 02 c ircuit "bias" voltage. With the engine running and after the 02 s ensor is hot, the voltage
should be rapidly changing, somewhere between 10 - 1000 millivolts (0.010 - 1.000 volt).
D14 - OXYGEN SENSOR EARTH
- RIGHT BANK -
This terminal should have zero volts. It is connected directly to the engine earth. This terminal earths the PCM
circuitry for the O2 voltage monitor inside the PCM.
D15 - OXYGEN SENSOR INPUT SIGNAL
- LEFT BANK -
W ith ignition "ON" and engine not running, the voltage should be 350 - 450 millivolts (0.350 - 0.450 volts). This
is the PCM-supplied 02 c ircuit "bias" voltage. With the engine running and after the 02 s ensor is hot, the voltage
should be rapidly changing, somewhere between 10 - 1000 millivolts (0.010 - 1.000 volt).
D16 - OXYGEN SENSOR EARTH
- LEFT BANK -
This terminal should have zero volts. It is connected directly to the engine earth. This terminal earths the PCM
circuitry for the O2 voltage monitor inside the PCM.
E1 - BOOST CONTROL SOLENOID
The PCM oper ates a norm ally closed solenoid valve, which contr ols vac uum to the By-Pass Valve Actuator. The
PCM turns "ON" the solenoid , to allow vacuum to the By-Pass Valve Actuator, to close the By-Pass valve and
allow full boost. If the PCM is not energising the boost solenoid, the voltage measured at this terminal should
equal battery voltage. If the PCM is controlling the solenoid, the measured voltage will be between battery
voltage and 0.50 volts.
E2 - FUEL INJECTOR 3 - CONTROL
E3 - FUEL INJECTOR 2 - CONTROL
E4 - FUEL INJECTOR 5 - CONTROL
The voltage seen at these terminals actually comes through the injectors, which are connected to +12 volts.
With the engine not running, the voltage seen would be battery voltage. With the engine running at idle, the
charging system increases the voltage slightly, so this voltage will increase. With higher engine RPM or more
engine load, the resulting increase in injector pulse frequency or injector pulse width will cause this voltage to
appear slightly less.
E5 - FUEL PUMP CONTROL MODULE
A duty cycle earth signal on this circuit varies depending on engine load. Under normal driving conditions, the
duty cycle earth signal supplied from the PCM to the Fuel Pump Control Module (terminal 7 of the Fuel Pump
Control Module) is at 33% duty cycle. This 33% duty cycle runs the Fuel Pump at a lower fuel flow rate. When
the vehicle is in a heavy engine load condition, the PCM will switch from 33% duty cycle to 100% duty cycle.
This will cause the Fuel Pump to operate at a high fuel flow rate to compensate for the higher engine load
condition. T his change in duty cycles does not change the f uel sys tem operating fuel pressur e, but changes the
fuel flow rate.
E6 - PRNDL A
E7 - PRNDL B
E8 - PRNDL C
These circuits along with PCM circuit F15 indicate to the PCM what transmission gear the driver has selected.
The PCM will then send a command via the serial data line to the instrument panel cluster (smart cluster) to
indicate to the driver what gear has been selected.