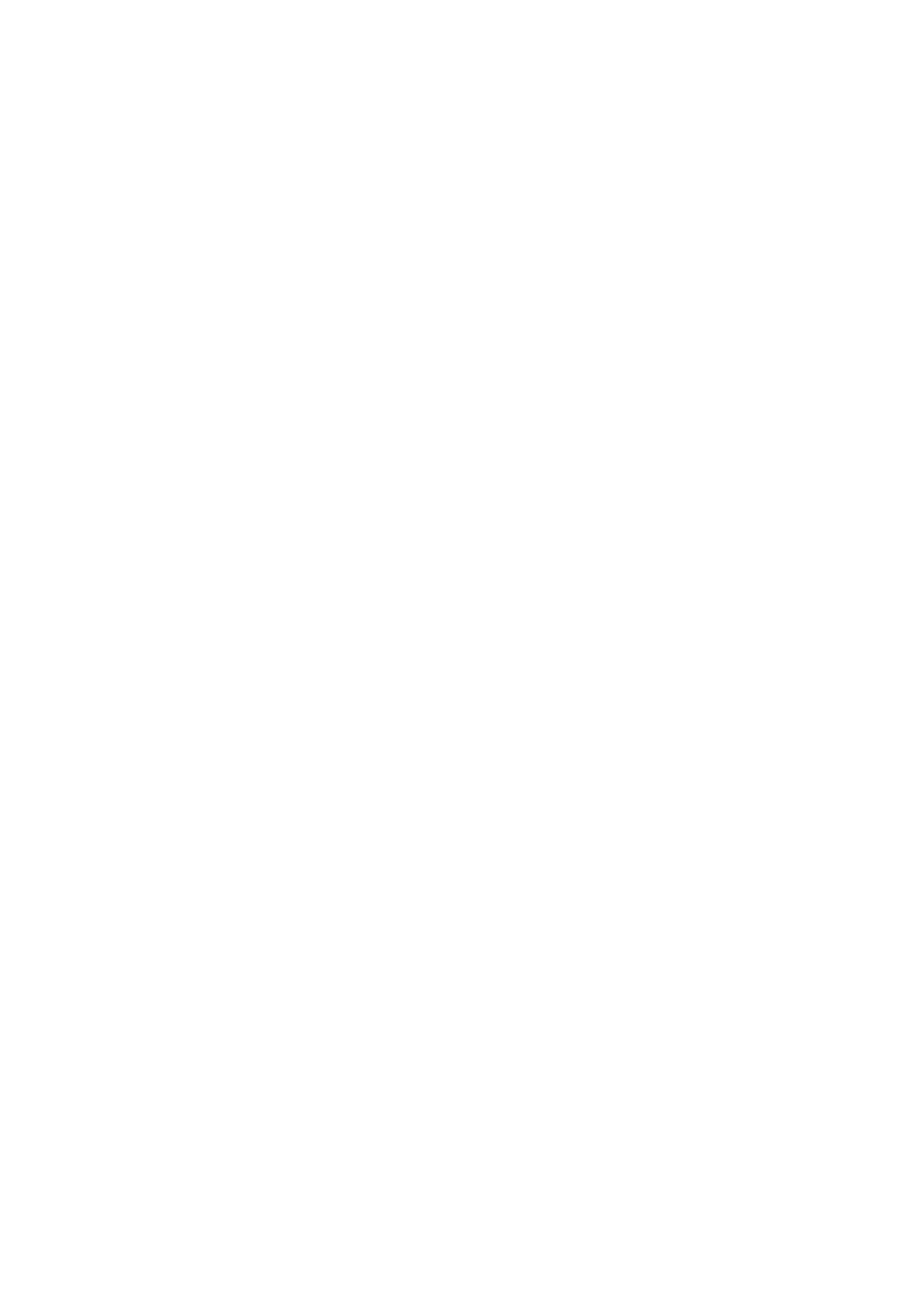
B1 – 1 – 2 SHIFT SOLENOID CONTROL
- AUTO TRANS ONLY –
The PCM is used to either open or pr ovide a path to earth for the 1-2 shif t solenoid. W hen the PCM provides a
path to earth, the 1-2 shift solenoid is considered “ON” and the voltage should read 0 volts.
B2 – NOT USED
B3 – ELECTRONIC SPARK TIMING (EST) OUTPUT
This terminal will have very low voltage with the ignition “ ON” but engine not running. W ith the engine running at
idle, the voltage should be slightly more than 1 volt. As the engine RPM goes up, this voltage will increases.
B4 – IGNITION MODULE BYPASS CONTROL
- IGNITION SYSTEM MODE CONTROL –
With ignition “ON” and engine not running this terminal will have very low voltage. As soon as the PCM sees
engine RPM of m ore than 1600 RPM (Electronic Spark Timing “run” threshold) the PCM turns on 5 volts to the
Ignition Module Bypass Control circuit, causing the ignition module to allow the PCM to operate the ignition
system.
B5 – SYSTEM EARTH
These terminals should have zero volts. They are connected directly to the engine earth.
B6 – CAMSHAFT POSITION INPUT SIGNAL
This signal is used by the PCM to “sequence” the energis ing of the fuel inj ectors, sim ilar to the firing order of an
engine. This allows the PCM to operate the fuel injectors in a “sequential fuel injection” mode. The camshaft
position sensor is actually wired to the ignition module. The ignition module sends one pulse per every two
crankshaft revolutions to the PCM to determine actual camshaft position, and thus, engine cycle sequence.
B7 – CRANKSHAFT 18X INPUT SIGNAL
The 18X crankshaft reference input signal is used to very accurately control EST spark timing at low engine
speeds – below 1200 RPM. Below 1200 RPM, the PCM monitors the 18X signal to control spark timing. At
engine speeds above 1200 RPM, the PCM uses the 3X c rankshaf t r ef er ence input s ignal to c ontrol s park timing.
(See 3X crankshaft reference terminal D12)
B8 – TRACTION CONTROL (TORQUE REQUESTED)
The ABS/ET C m odule will send a N.m signal to the PCM when torque reduction is requested fr om the ABS/ETC
module for traction control. This N.m signal should match closely with Torque Achieved N.m signal, when
traction control is being requested.
B9 – 3X CRANKSHAFT REFERENCE INPUT SIGNA L HIGH
This terminal c ould be called the “ tac h” input. It pr ovides the PCM with RPM and crankshaf t pos ition inf or mation.
With ignition “ON” but engine not running, the voltage will be either high or low, depending on crankshaft
position. As the crankshaft turns, the voltage will be an average of the two readings. The PCM uses the 3X
signal to control fuel injection, and spark timing with engine speeds above 1200 RPM.
B10 – CRANKSHAFT REFERENCE INPUT SIGNAL LOW
This terminal should always be zero volts. It is connected through the ignition module to engine earth.
B11 – TRACTION CONTROL (TORQUE ACHIEVED)
The PCM sends a N.m signal to the ABS/ETC module on the delivered torque circuit informing the ABS/ETC
module of response made to the desired torque N.m signal. This N.m signal should match closely with the
Requested Torque N.m signal. A problem with the
delivered torque circuit should cause a ABS/ETC DTC to set, and traction control to be disabled.
B12 – ENGINE COOLING FAN – HIGH SPEED RELAY CONTROL
This terminal will have battery voltage until the PCM energises the high s peed cooling fan relay by supplying the
earth; then it will be close to zero. The input that causes the PCM to energise the high speed fan relay is the
engine coolant tem perature s ensor. T he PCM will also energis e the high speed f an relay in the Diagnos tic Mode
– i.e., ignition “ON,” engine stopped, and DLC diagnostic “test” enable terminal earthed. Refer engine fan
TABLE A-12 of the VX Series Service Information for further explanation.
(The Body Control Module operates the cooling fan low speed relay)