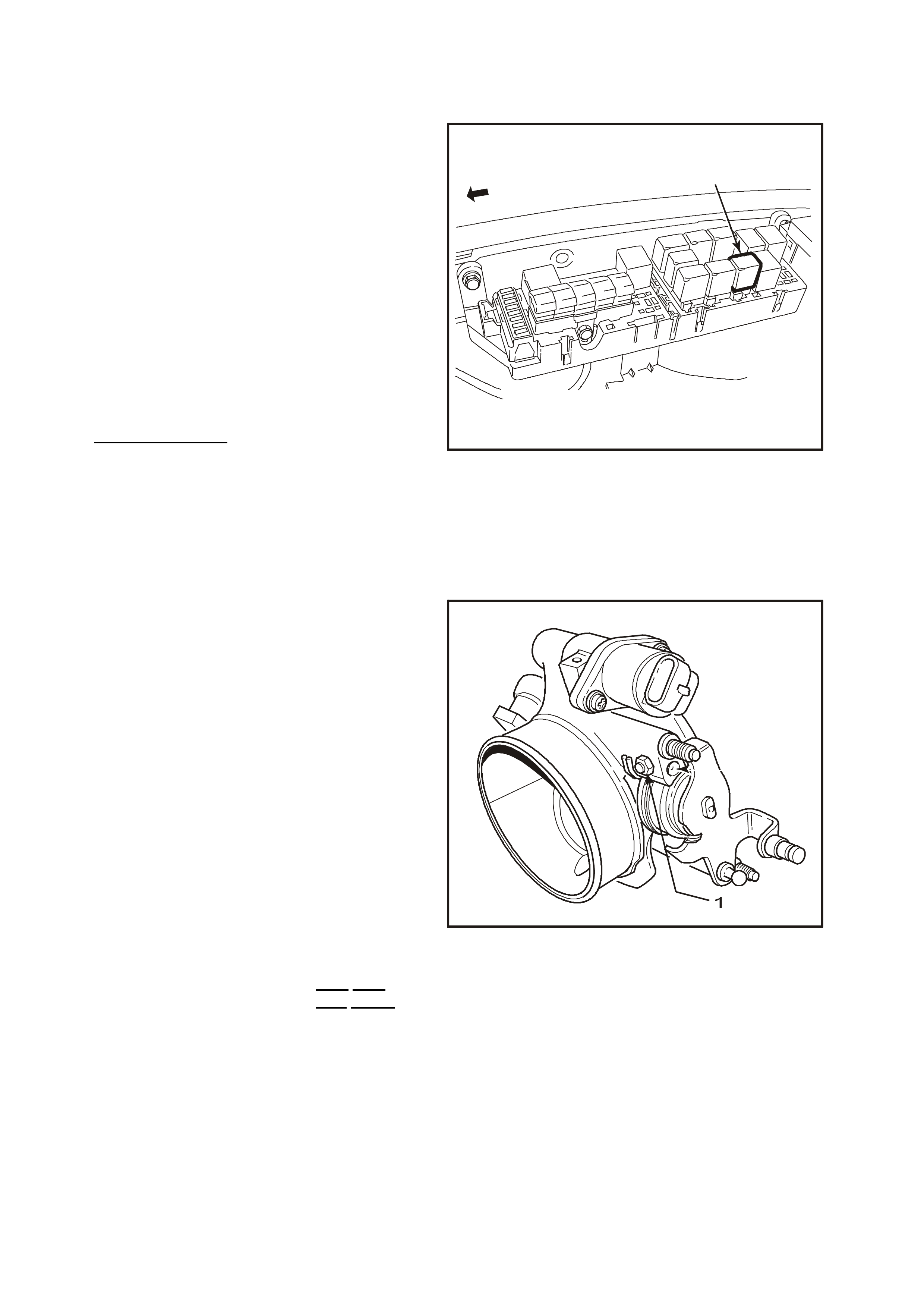
3.10 FUEL CONTROL SYSTEM
FUEL PUMP RELAY
The fuel pump relay (1) is located in a relay
housing, in the engine compartment. The relay
housing is positioned forward of the right side
(driver's side) strut tower, in front of the cooling
system coolant recovery reservoir. Other than
checking for loose connectors, the only service
possible is replacement.
FUEL PRESSURE RELIEF PROCEDURE
IMPORTANT:
UNLESS THIS PROCEDURE IS FOLLOWED
BEFORE SERVICING FUEL LINES OR
CONNECTIONS, FUEL SPRAY INTO THE
ENGINE COMPARTMENT COULD OCCUR!
1. Remove "Fuel Pump Relay" from engine
compartment relay housing.
2. With throttle closed, crank engine - engine m ay
start and idle until fuel supply remaining in fuel
line is exhausted. W hen engine stops, engage
starter again for 10 seconds to ensure
dissipation of any remaining pressure.
3. Refit fuel pump relay (1).
1
4239
Figure 6C1-3-18 Fuel Pump Relay Location
THROTTLE STOP SCREW - RESET PROCEDURE
IMPORTANT:
Engine idle for this V6 application must be check ed
every 80,000KM. If the IAC valve counts are
greater than 25 at idle, the throttle body must be
removed and cleaned. Refer to
Throttle Body Cleaning Procedure in this
Section.
The T hrottle Stop Screw (1) controls the minimum
throttle opening (nominal "Closed throttle"
position). It is preset at the factory and must not
be reset unless:
I. The s crew is known to have been inadvertently
reset,
-OR-
II. Clearly instructed to do so by a diagnostic
Table.
Engine idle speed, which will vary with engine
temperature, is PCM - controlled and is not
adjustable.
PCM - Controlled idle speed (IAC) and
Throttle stop screw setting (RPM) ARE NOT
THE SAME!
4346
Figure 6C1-3-19 Throttle Stop Screw Location
Thro ttle stop screw setting (RPM) must always be less than the PCM controlled idle s peed, and is chec ked only
after temporarily disabling the PCM's method of controlling idle speed, the Idle Air Control system. The throttle
stop screw setting is the least likely cause of an abnormal idle condition, therefore resetting the screw should
only be considered as a last resort. An incorrect setting is likely to cause a deterioration in idle stability.
IMPORTANT: - Inspect
• Before any adjustments are made, ensure that no vacuum leaks exist. Check all vacuum hoses, MAF air
ducts, inlet manifold gasket, throttle body-to-manifold attachment, and any vacuum-operated devices. The
engine must be at normal operating temperature before any checking or resetting is attempted.
WITH THIS ENGINE CONTROL SYSTEM, ANY VACUUM LEAK WILL RESULT IN A LOW/ROUGH IDLE
SPEED.