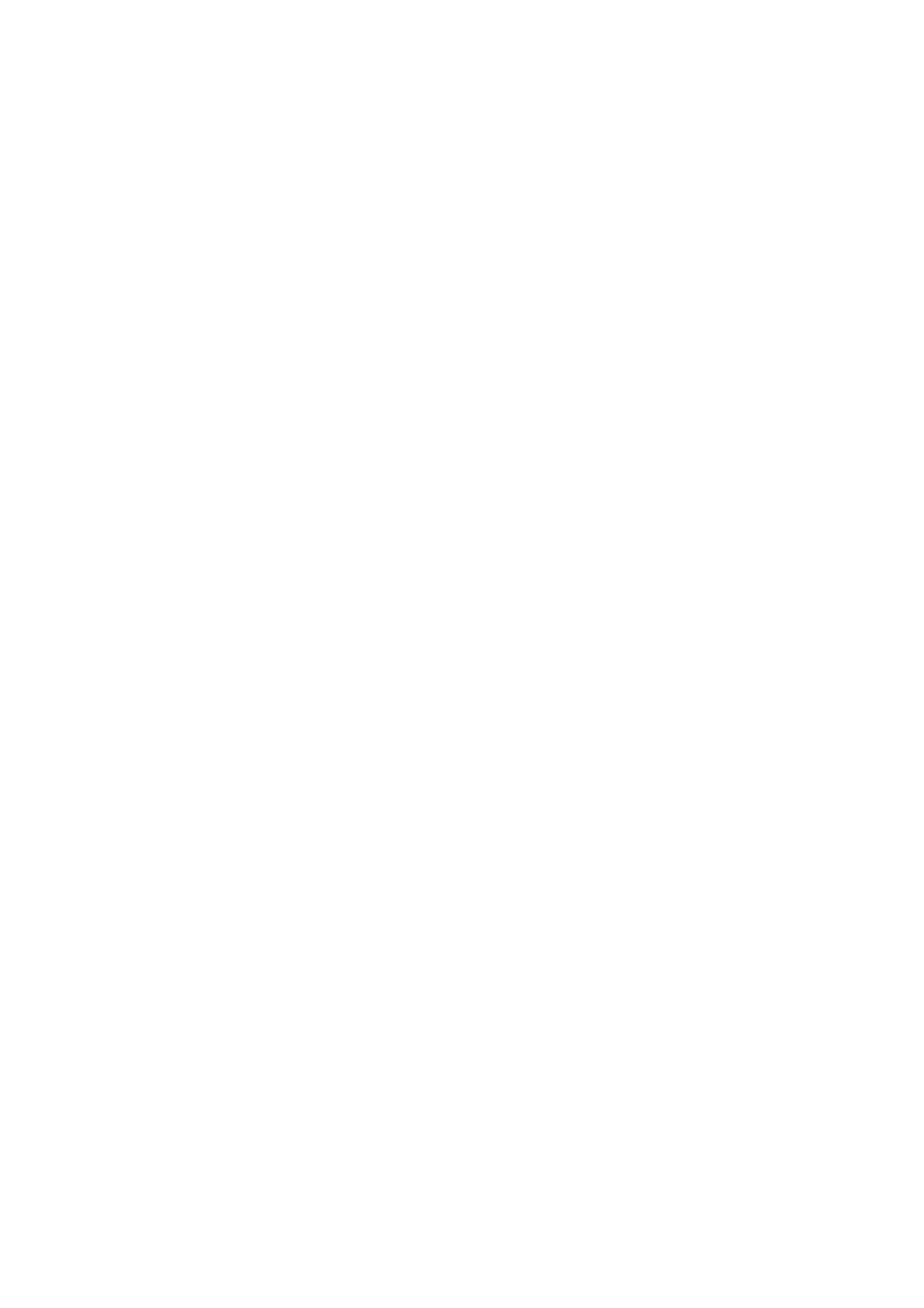
Instrument Illumination (All): In this mode, TECH 2 commands the BCM to brighten or dim the instrument
cluster and trip computer illumination lamps.
Precondition: Ignition ON.
Auto Lights On (ALL): In this mode, with the ignition on and the headlamp switch in the Auto position, TECH 2
commands the BCM to turn the headlamps on and off.
Precondition: Headlamps Switch in the Auto position.
Rear Lamp Bulb Fail (HI): In this m ode and with ignition switched O N, TECH 2 c om m ands the BCM to switch
on and off Rear Lamp Bulb Failure Warning in the instrument cluster.
Precondition: Ignition ON.
Rear Stop Lamp Bulb Fail (HI): In this mode and with ignition switched ON, T ECH 2 comm ands the BCM to
switch on and off Rear Stop Lamp Failure Warning in the instrument cluster.
Precondition: Ignition ON.
Rear Lamp Fuse Fail (H I): In this mode and with ignition s witched ON, TECH 2 commands the BCM to switch
on and off Rear Lamp Fuse Failure Warning in the instrument cluster.
Precondition: Ignition ON.
Low Speed Cooling Fan (ALL): In this mode, T ECH 2 com mands the BCM to switch on and then off , (will switch
off automatically after approx imately four seconds pr ovided the PCM is not commanding the low fan on) the engine
cooling low speed fan relay.
Precondition: Ignition ON.
Data Bus Isolator (ALL): In this mode, the BCM data bus isolator switch can be opened or closed.
To check if the data bus isolator is operating, while commanding the data bus isolator open with TECH 2, start
engine and monitor the trip c omputers “ins tant f uel c onsumption” display while varying the engine speed. When the
data bus isolator switch is opened, the trip computers instant fuel consumption display will not update.
Precondition: Ignition ON.
Central Lock ing (ALL): In this mode, TECH 2 commands the BCM to operate all door lock actuators.
Precondition: Ignition OFF.
Rear Compartment (ALL): In this mode, TECH 2 commands the BCM to activate the sedan rear compartment
lock actuator.
Precondition: Ignition ON.
Wipers (ALL): If Wipers is s elected, an additional application m enu will be displayed of fering extra func tional tests
of the vehicles wiper system.
Front Wipers (ALL): In this mode, the front windshield wipers can be driven On and Off.
Precondition: Ignition ON.
Rear Wipers (LU, MI & MIAL): In this mode, the rear screen wipers can be driven On and Off.
Precondition: Ignition ON.
Power Windows (HI, LU, MI & MIAL): If Power Windows is selected, an additional application menu will be
displayed offering extra functional tests of the vehicles window system.
Driver’s Window Down (HI, LU, MI & MIAL): In this mode, the driver’s window can be driven down.
NOTE: Before entering and conducting this test, ensure that driver's window is fully up.
Precondition: Ignition ON.
Front Passenger’s Window Down (HI, LU, MI& MIAL): In this mode, the front passenger's window can be
driven down.
NOTE: Before entering and conducting this test, ensure that the front passenger's window is fully up.
Precondition: Ignition ON.
Power Window Relay (HI, LU, MI& MIAL): In this m ode, TECH 2 can command the BCM to turn the power
window relay ON and OFF.
Precondition: Ignition ON.
Antenna (HI, LU): In this mode, TECH 2 commands the BCM to raise or lower the antenna.
Precondition: Ignition ON.
Horn (ALL): In this mode, the horn can be commanded ON and OFF.
Precondition: Ignition ON.
Interior Illumination Relay (ALL): In this mode, TECH 2 commands the interior illumination relay ON or OFF.
Preconditions: Ignition and Interior Light ON.