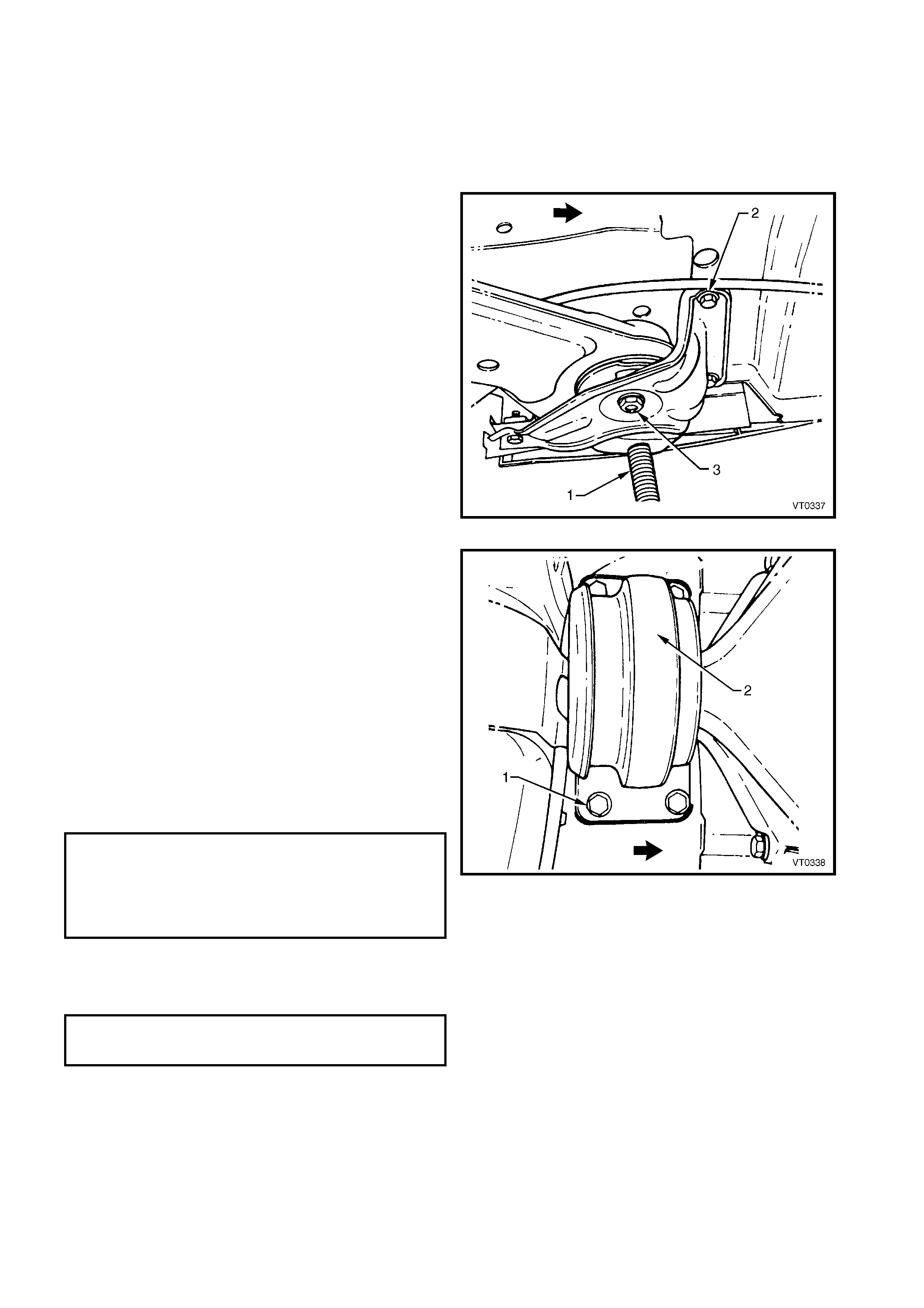
REAR SUSPENSION FRAME ASSEMBLY
LT Section No. 07-150A
NOTE. The rear suspension frame assembly centering
tool needs to be held in position during the alignment
procedure. Therefore, assistance will be required to
complete this operation.
1. Using chassis stands (1), support the vehicle at
hoist pad locations.
2. Remove the wheels, refer to Section 10,
WHEELS AND TYRES.
3. Remove intermediate muffler and pipe assembly
together with rear muffler and pipe assembly.
Refer to Section 8B, EXHAUST SYSTEM.
4. From underneath the vehicle, support the final
drive assembly with a trolley jack. Raise the jack
slightly to take some of the weight off the final
drive mount.
5. Loosen the three M10 screws (2) attaching the
rear suspension support insulator bracket to the
vehicle, LH and RH side.
6. Loosen the rear frame assembly M14 attaching
bolts (3) LH and RH side.
Figure 1A2-21
7. Loosen the four scr ews (1) attaching the final drive
rear mount (2).
8. Fit rear suspension centering tool No AU 458 (1),
refer to Figure 1A2-23.
NOTE: The rear crossmember centering tool locates
into 19 mm diameter body datum holes (2) positioned
forward of the rear suspension frame assembly.
9. With the help of an assistant, manoeuvre the rear
suspension assembly until the location pins (3) of
the rear crossmember centering tool engage the
alignment holes on the rear frame assembly.
10. Tighten the rear frame assembly M14 attaching
bolts LH and RH side to the specified torque, refer
to (3) Figure 1A2-21.
11. Tighten the f our s c rews (1) attac hing the f inal dr ive
rear mount (2), refer to Figure 1A2-22.
Figure 1A2-22
REAR SUSPENSION FRAME
ASSEMBLY ATTACHING BOLT
TORQUE SPECIFICATION Stage 1 125 Nm
Stage 2 Turn 30°- 45°
Min. total 135 Nm
FINAL DRIVE REAR MOUNT ATTACHING
SCREWS TORQUE SPECIFICATION 30.0 – 45.0 Nm