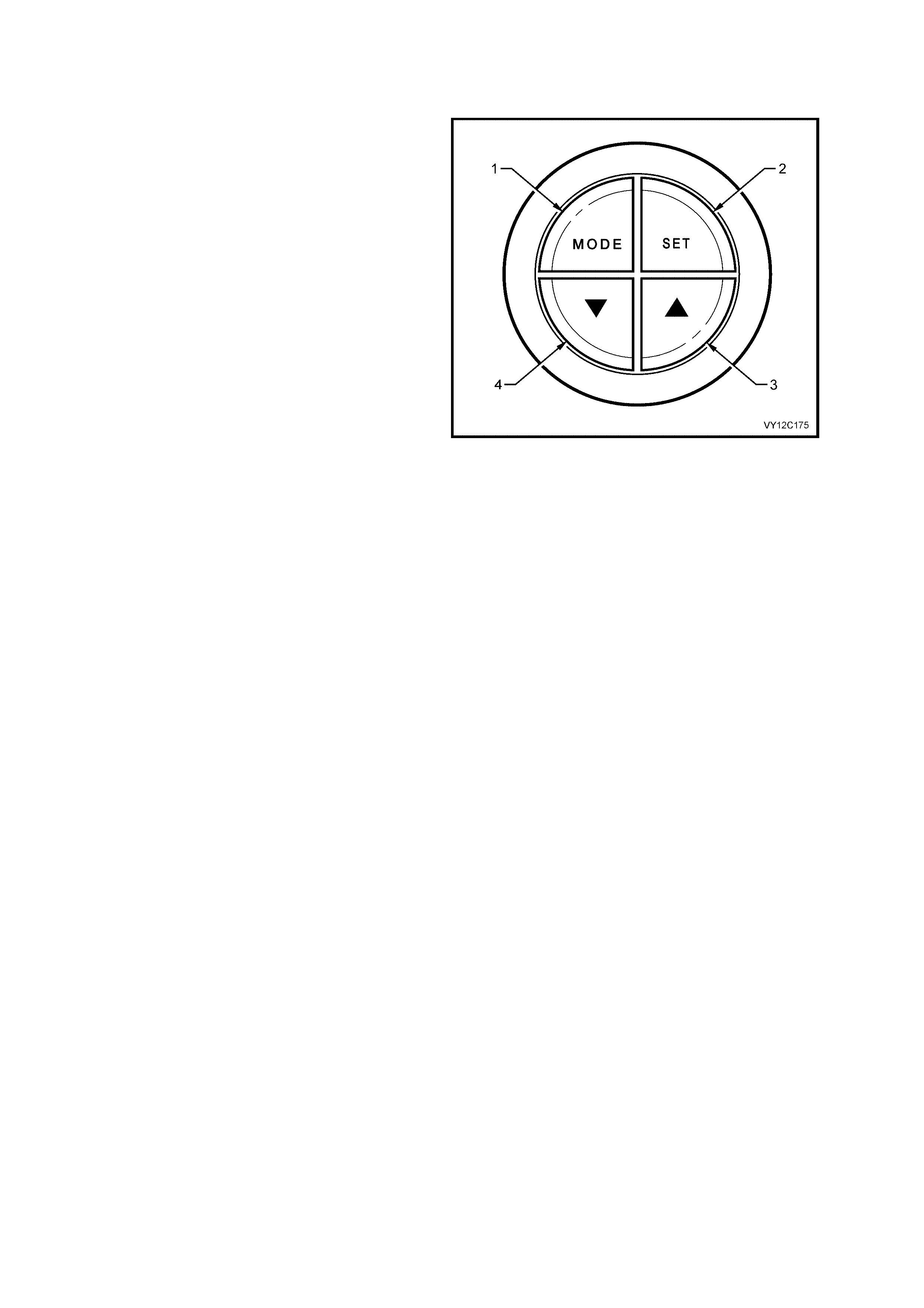
1.5 TRIP COMPUTE R — TRIP LE WINDOW CLUSTER
OPERATION
The buttons for the trip com puter are loc ated to the
left of the instrument cluster. The four buttons in
the switch assembly are MODE (1), SET (2), UP
(3) and DOWN (4).
The trip computer screens are displayed on the
MFD, and the two side Liquid Crystal Displays
(LCD). The MFD is located in the centre of the
instrument cluster below the gauges, and the two
side LCDs are located beneath the temperature
gauge on the left, and the fuel gauge on the right.
To scroll between the functions (three sets of
displays), press the MODE button for less than
2 seconds. The speed related details are provided
in the left window, the distance related details are
provided in the MFD, and the fuel related details
are provided in the window on the right.
When the ignition is turned on, the MFD initially
displays the start up sequence, then displays the
same trip computer functions as when the ignition
was last turned of f as long as the same priority key
is used.
The trip computer functions can be reset when the
Average Speed or Trip Time details are displayed
in the left window. To reset the trip computer
functions, press the SET button. This will reset all
functions, with the exception of Distance to Empty,
Overspeed Warning, Odometer, Time to Arrival,
Distance to Arrival, Remaining Fuel and
Instantaneous Fuel.
NOTE: If the wrong buttons have been accidentally
pressed, c aus ing the dis play to show other than the
normal readings, turn the ignition off, then on again.
Personal customisation of the trip computer is also
possible. Refer to 1.8 CUSTOMISATION MODE in
this Section.
Figure 12C-21
The trip computer functional sequence for the
triple-window cluster is shown in Figure 12C-22.
Pressing the MODE button steps through the
screens as shown in the flowchart. There are two
flow paths depending upon the selection of the
Trip A and B function in Customisation Mode:
• If Trip A and B is enabled, the screens in the
right-hand path will be displayed, or
• If Trip A and B is not enabled, the screens in
the left-hand path will be displayed.
The Dis tance to Arr ival function m u st be enabled in
Customisation Mode before the Time to Arrival /
Distance to Arrival / Remaining Fuel screens can
be accessed using the MODE button. These
screens are not available if T rip A and B function is
enabled. However they can be accessed from the
Trip B screens by pressing and holding the MODE
button for more than 2 seconds.
NOTE: If the instrument cluster is set as a Police
cluster, the MFD will always default to True Speed
Mode at ignition on. T he digital speedom eter is the
default display for Police instrument clusters.