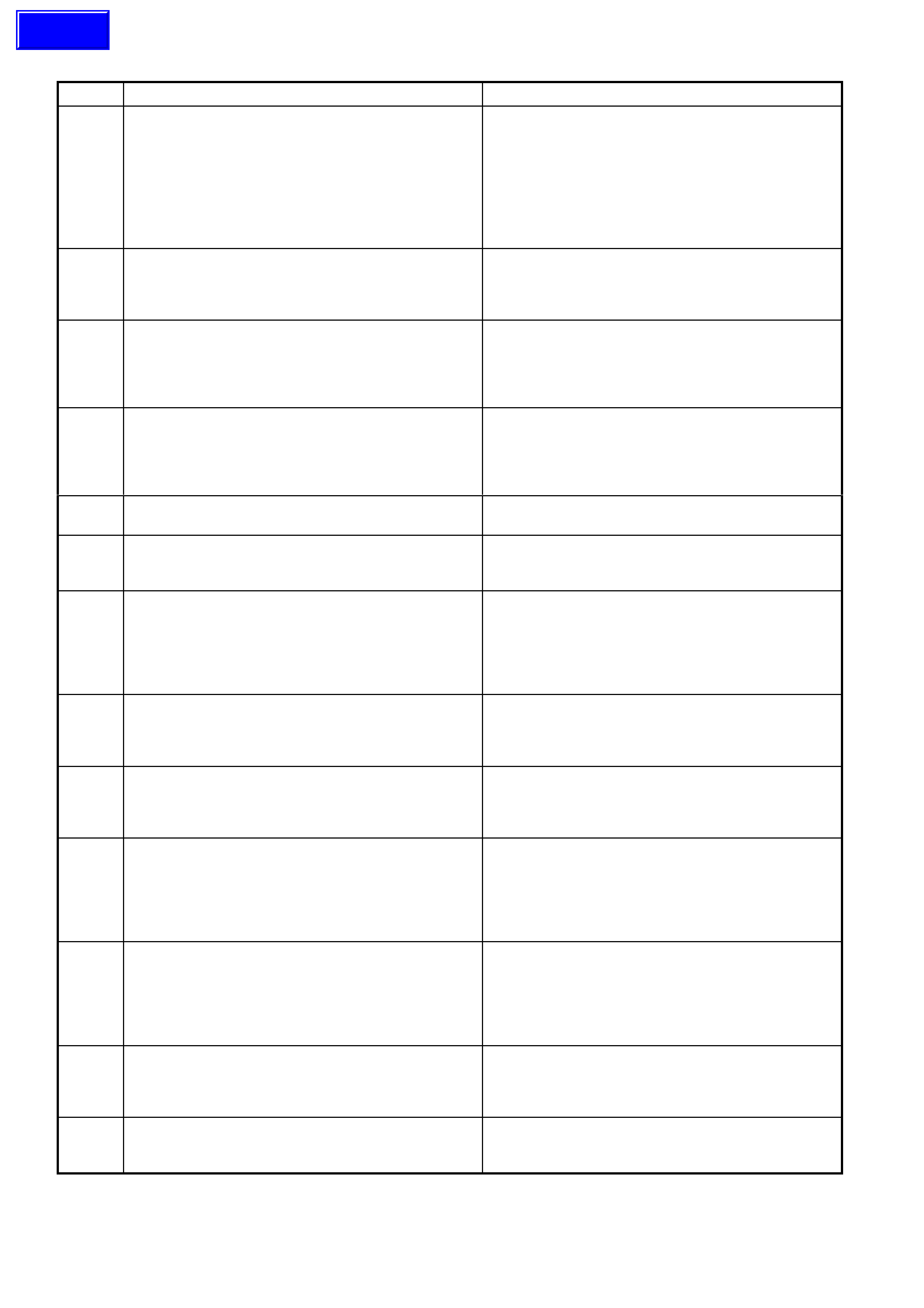
The following table sets out the diagnostic trouble codes for the BCM.
DTC CODE DESCRIPTION REFER
1 Output Overload. The DTC sets when a short to
battery voltage is detected on the following outputs:
Indicators, Front Intermittent Wiper, Aircon / Priority 2,
Demist / Priority 1, Main Horn, Accessory Relay and
Low Speed Fan.
When DTC 1 is set, refer to the section relevant to the
function listed.
Note: DTC 1 can also be set by electrical transients.
Therefore, if DTC 1 is set and there are no noticeable
problems with the vehicle, clear DTC and check
function of BCM outputs. If DTC does not reset and
BCM outputs are functioning correctly, disregard
DTC 1.
2 Slip Ring Communication Error. Each time the BCM
receives a message with an invalid checksum via the
slip ring a counter is incremented. Twenty consecutive
bad messages mu st be received to set the DTC .
Refer to 4.7 THEFT DETERRENT SYSTEM in this
Section.
5 Tail Lamp Bulb Failure. The BCM monitors the
current in the tail lamp circuit. The DTC sets and
illuminates a telltale in the instrument cluster if the tail
lamp current is below the factory preset value for more
than 3 seconds.
Refer to 4.20 REAR LAMP FAILURE WARNING
SYSTEM in this Section.
6 Stop Lamp Bulb Failure. The BCM monitors the
current in the stop lamp circuit. The DTC sets and
illuminates a telltale in the instrument cluster if the stop
lamp current is below the factory preset value for more
than 3 seconds.
Refer to 4.20 REAR LAMP FAILURE WARNING
SYSTEM in this Section.
7 No Serial Data From PCM. The DTC sets if PCM
serial data lost for 10 seconds. Refer to 4.2 SERIAL DATA COMMUNICATION in this
Section.
17 Not Okay To Start Received From PCM. The DTC
sets when the BCM is in passive arm mode and
attempting to start without a valid slip ring message.
Refer to 4.3 REMOTE RECEIVER / KEY in this
Section.
18 Auxiliary (Secondary and Tertiary) Serial Data Bus
Fault. The data bus isolator will remain closed for
625 ms after entering the short loop poll sequence. If
no PCM communication is received, the isolator will be
opened. If the BCM receives PCM communication after
the isolator has been opened the DTC is set.
Refer to 4.2 SERIAL DATA COMMUNICATION in this
Section.
19 EEPROM Error. The EEPROM data is divided into
eight tables, and each table has a checksum. When
each table is loaded into RAM, the checksum is
verified. If the checksum is wrong the DTC is set.
Clear the DTC. If the DTC sets again, remove fuse F29
to reset the BCM.
20 RAM Error. The BCM maintains a RAM copy of the
EEPROM data. Each of the eight tables is checked
periodically to verify the checksum. If the checksum is
wrong the DTC is set.
Clear the DTC. If the DTC sets again, remove fuse F29
to reset the BCM.
21 Battery Voltage Too Low. The DTC sets if the battery
voltage drops below 8 V for 20 seconds. Refer to Section 6D1-1A, CHARGING SYSTEM – V6
ENGINE (100 AMP), Section 6D1-1B, CHARGING
SYSTEM – V6 ENGINE (120 AMP), Section 6D2-1,
CHARGING SYSTEM – V6 S/C ENGINE, or Section
6D3-1, CHARGING SYSTEM – GEN III V8 ENGINE as
appropriate for further diagnosis.
22 Battery Voltage Too High. The DTC sets if the battery
voltage is above 16 V for 20 seconds. Refer to Section 6D1-1A, CHARGING SYSTEM – V6
ENGINE (100 AMP), Section 6D1-1B, CHARGING
SYSTEM – V6 ENGINE (120 AMP), Section 6D2-1,
CHARGING SYSTEM – V6 S/C ENGINE, or Section
6D3-1, CHARGING SYSTEM – GEN III V8 ENGINE as
appropriate for further diagnosis.
23 Door Lock / Unlock Circuit Overload. The DTC sets
when the doors have been activated 10 times in rapid
succession. Once activated the doors will timeout for a
period of 32 seconds.
Refer to 4.5 CENTRAL DOOR LOCKING in this
Section.
24 Remote Key Rolling Code Error. Each time an RF
message is received the Rolling Code is checked. The
DTC sets if the Rolling Code is out of range.
To resynchronize the rolling code, turn the ignition on
with the remote key.