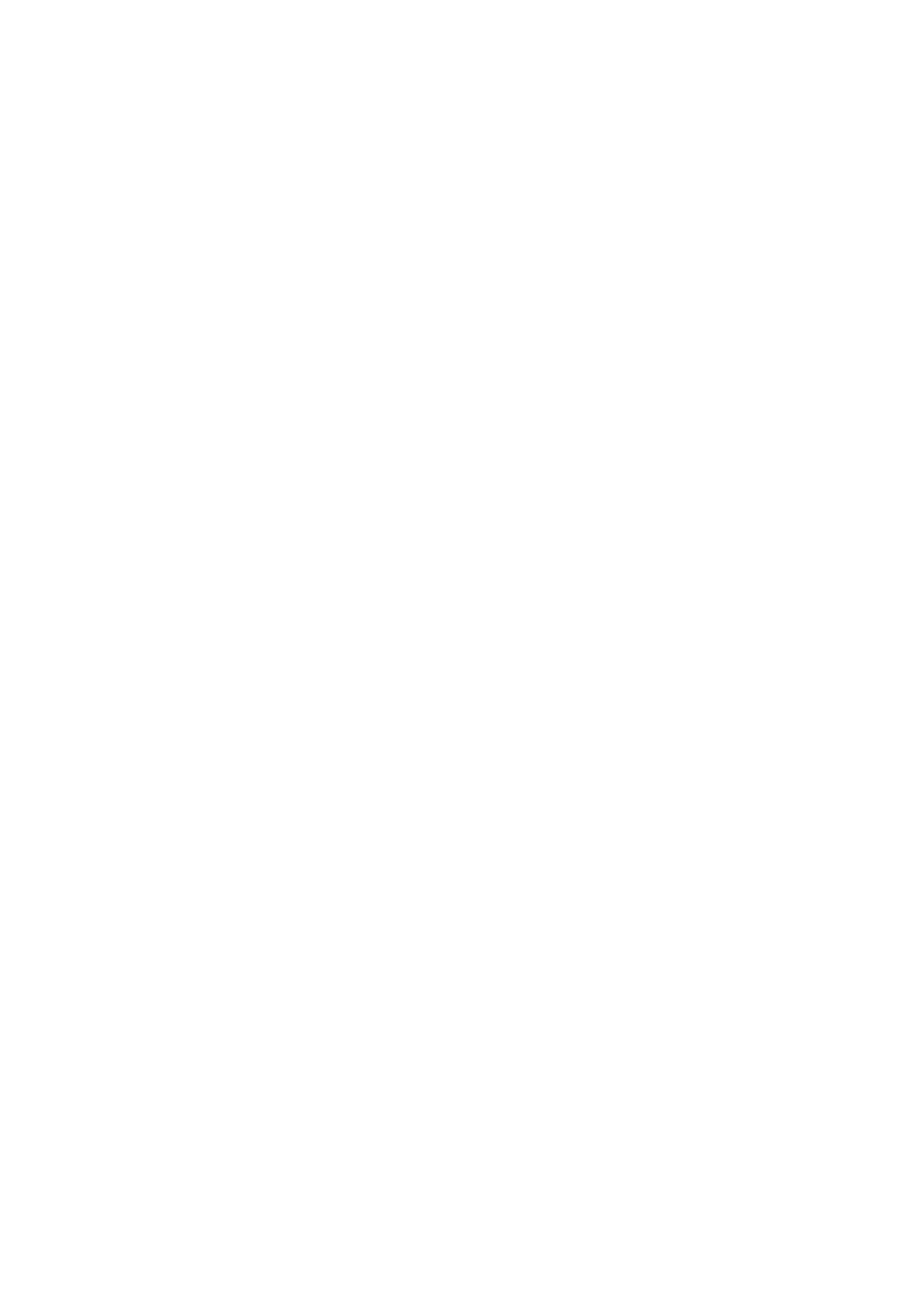
3.12 REAR SEATBELT BUCKLE ASSEMBLY,
COUPE
REMOVE
REINSTALL
3.13 CHILD SEAT ANCHORS
REMOVE
SEDAN
WAGON
UTILITY
COUPE
REINSTALL
4 DIAGNOSTICS
4.1 BASIC KNOWLEDGE REQUIRED
4.2 PRELIMINARY SYSTEM DIAGNOSIS
4.3 OPS / SRS SELF DIAGNOSTICS
4.4 TECH 2 DIAGNOSTICS
4.5 TECH 2 TEST MODES AND DISPLAYS
FOR OPS / SRS DIAGNOSIS
4.6 DIAGNOSTIC CHARTS
INTRODUCTION
CHART A -- DIAGNOSTIC CIRCUIT CHECK
CHART B -- SRS WARNING INDICATOR
INOPERATIVE
CHART C SRS WARNING INDICATOR
ILLUMINATED (NO DTCS STORED)
DTC 17 -- DRIVER’S AIRBAG CIRCUIT
SHORT TO BATTERY
DTC 18 -- DRIVER’S AIRBAG CIRCUIT
SHORT TO EARTH
DTC 19 -- DRIVER’S AIRBAG
CIRCUIT CAPACITANCE TOO HIGH
DTC 20 -- DRIVER’S AIRBAG
CIRCUIT CAPACITANCE TOO LOW
DTC 21 -- DRIVER’S AIRBAG
CIRCUIT RESISTANCE TOO HIGH
DTC 22 -- DRIVER’S AIRBAG
CIRCUIT RESISTANCE TOO LOW
DTC 247 – DRIVER’S AIRBAG CIRCUIT
POWER STAGE ERROR
DTC 33 -- PASSENGER’S AIRBAG
CIRCUIT SHORT TO BATTERY
DTC 34 -- PASSENGER’S AIRBAG
CIRCUIT SHORT TO EARTH
DTC 35 -- PASSENGER’S AIRBAG
CIRCUIT CAPACITANCE TOO HIGH
DTC 36 -- PASSENGER’S AIRBAG
CIRCUIT CAPACITANCE TOO LOW
DTC 37 -- PASSENGER’S AIRBAG
CIRCUIT RESISTANCE TOO HIGH
DTC 38 -- PASSENGER’S AIRBAG
CIRCUIT RESISTANCE TOO LOW
DTC 247 -- PASSENGER’S AIRBAG CIRCUIT
POWER STAGE ERROR
DTC 49 -- LEFT-HAND PRETENSIONER
CIRCUIT SHORT TO BATTERY
DTC 50 -- LEFT-HAND PRETENSIONER
CIRCUIT SHORT TO EARTH
DTC 51 -- LEFT-HAND PRETENSIONER
CIRCUIT CAPACITANCE TOO HIGH
DTC 52 -- LEFT-HAND PRETENSIONER
CIRCUIT CAPACITANCE TOO LOW
DTC 53 -- LEFT-HAND PRETENSIONER
CIRCUIT RESISTANCE TOO HIGH
DTC 54 -- LEFT-HAND PRETENSIONER
CIRCUIT RESISTANCE TOO LOW
DTC 247 -- LEFT-HAND PRETENSIONER
CIRCUIT POWER STAGE ERROR
DTC 65 -- RIGHT-HAND PRETENSIONER
CIRCUIT SHORT TO BATTERY
DTC 66 -- RIGHT-HAND PRETENSIONER
CIRCUIT SHORT TO EARTH
DTC 67 -- RIGHT-HAND PRETENSIONER
CIRCUIT CAPACITANCE TOO HIGH
DTC 68 -- RIGHT-HAND PRETENSIONER
CIRCUIT CAPACITANCE TOO LOW
DTC 69 -- RIGHT-HAND PRETENSIONER
CIRCUIT RESISTANCE TOO HIGH
DTC 70 -- RIGHT-HAND PRETENSIONER
CIRCUIT RESISTANCE TOO LOW
DTC 247 -- RIGHT-HAND PRETENSIONER
CIRCUIT POWER STAGE ERROR
DTC 81 -- LEFT-HAND SIDE IMPACT
AIRBAG CIRCUIT SHORT TO BATTERY
DTC 82 -- LEFT-HAND SIDE IMPACT
AIRBAG CIRCUIT SHORT TO EARTH
DTC 83 -- LEFT-HAND SIDE IMPACT AIR
BAG CIRCUIT CAPACITANCE TOO HIGH
DTC 84 -- LEFT-HAND SIDE IMPACT AIR
BAG CIRCUIT CAPACITANCE TOO LOW
DTC 85 -- LEFT-HAND SIDE IMPACT AIR
BAG CIRCUIT RESISTANCE TOO HIGH
DTC 86 -- LEFT-HAND SIDE IMPACT AIR
BAG CIRCUIT RESISTANCE TOO LOW
DTC 247 -- LEFT-HAND SIDE-IMPACT
AIRBAG CIRCUIT POWER STAGE ERROR
DTC 97 -- RIGHT-HAND SIDE IMPACT AIR
BAG CIRCUIT SHORT TO BATTERY
DTC 98 -- RIGHT-HAND SIDE IMPACT AIR
BAG CIRCUIT SHORT TO EARTH
DTC 99 -- RIGHT-HAND SIDE IMPACT AIR
BAG CIRCUIT CAPACITANCE TOO HIGH
DTC 100 -- RIGHT-HAND SIDE IMPACT AIR
BAG CIRCUIT CAPACITANCE TOO LOW
DTC 101 -- RIGHT-HAND SIDE IMPACT AIR
BAG CIRCUIT RESISTANCE TOO HIGH
DTC 102 -- RIGHT-HAND SIDE IMPACT AIR
BAG CIRCUIT RESISTANCE TOO LOW
DTC 247 -- RIGHT-HAND SIDE-IMPACT
AIRBAG CIRCUIT POWER STAGE ERROR
DTC 129 -- LEFT PERIPHERAL
ACCELERATION SENSOR LINE FAULT
DTC 130 -- RIGHT PERIPHERAL
ACCELERATION SENSOR LINE FAULT
DTC 131 -- LEFT PERIPHERAL
ACCELERATION SENSOR COMMUNICATION
FAULT
DTC 132 -- RIGHT PERIPHERAL
ACCELERATION SENSOR COMMUNICATION
FAULT
DTC 133 -- LEFT PERIPHERAL
ACCELERATION SENSOR IDENTIFICATION
FAULT
DTC 134 -- RIGHT PERIPHERAL
ACCELERATION SENSOR IDENTIFICATION
FAULT
DTC 135 -- LEFT PERIPHERAL
ACCELERATION SENSOR HARDWARE
FAULT
DTC 136 -- RIGHT PERIPHERAL
ACCELERATION SENSOR HARDWARE
FAULT
DTC 161 -- CONFIGURATION MISMATCH:
TOO LITTLE OR TOO MANY LOOPS IN
OPS / SRS
DTC 163 -- INFLATABLE RESTRAINT
CONTROL MODULE (SDM) INTERNAL
FAULT
4.7 DRIVERS SEATBELT WARNING INDICATOR
SWITCH DIAGNOISIS
5. TORQUE WRENCH SPECIFICATIONS
6. SPECIAL TOOLS