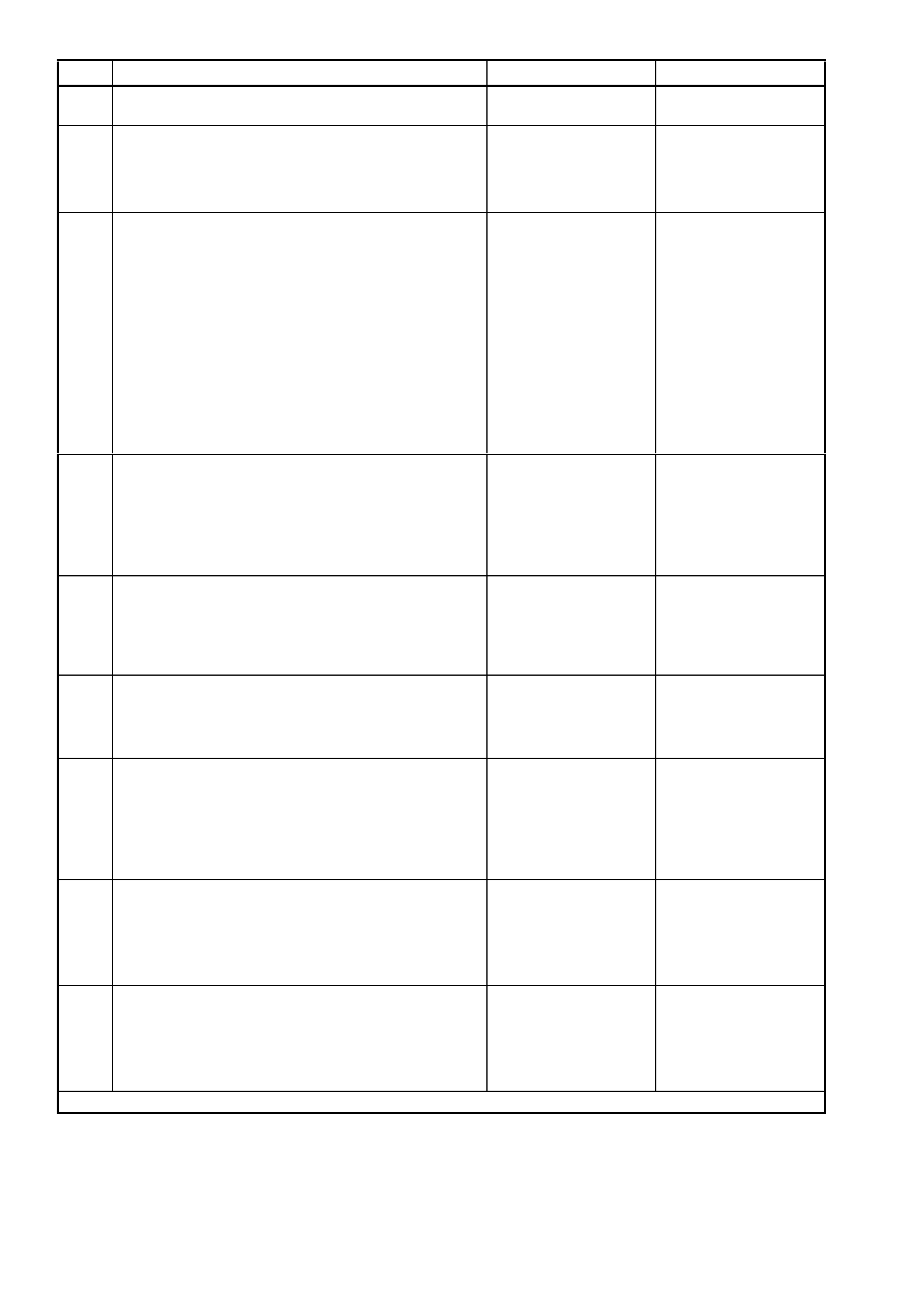
STEP ACTION YES NO
1. 1. Check the fuse F18.
Is it serviceable? Go to Step 2. Replace fuse F18.
2. 1. Replace the accessory control relay within the
passenger compartment fuse and relay panel
assembly, refer to Section 12O, FUSES, RELAYS
AND WIRING HARNESSES.
Does the wiper system operate?
System serviceable. Go to Step 3.
3. 1. Remove the wiper arm assemblies, refer to
2.3 FRONT WIPER ARM ASSEMBLY.
2. Remove the plenum cover assembly and water
deflector assembly, refer to 2.5 PLENUM COVER
ASSEMBLY,EXEPT COUPE, or 2.6 PLENUM
COVER ASSEMBLY,COUPE.
3. Disconnect the wiring harness connector M17 – X1.
4. W ith a multimeter, probe with the positive lead to the
harness connector M17 – X1 pin 1 and the negative
lead to the harness connector M17 – X1 pin 4.
5. Switch the ignition to ACC or ON position, and the
wiper and washer control switch to low speed
position.
Is the reading on the multimeter battery voltage?
Go to Step 7. Go to Step 4.
4. 1. W ith a multimeter, probe with the positive lead to the
harness connector M17 – X1 pin 1 and the negative
lead to body earth.
2. Switch the ignition to ACC or ON position, and the
wiper and washer control switch to low speed
position.
Is the reading on the multimeter battery voltage?
There is a fault in circuit
550. Diagnose the
circuit. Repair or
replace circuit 550.
Go to Step 5.
5. 1. Test wi per and washer control switch S247, refer to
2.9 WIPER AND WASHER CONTROL SWITCH.
Is the wiper and washer control switch serviceable? Go to Step 6.
Replace the wiper and
washer control switch
S247, refer to
2.9 WIPER AND
WASHER CONTROL
SWITCH.
6. 1. Repeat step 3 and read the value of the multimeter.
Is the reading on the multimeter battery voltage? Go to Step 7.
There is a fault in circuit
342, 70, 243,or 95.
Diagnose the circuits.
Repair or replace circuit
342, 70, 243,or 95.
7. 1. W ith a multimeter, probe with the positive lead to the
harness connector M17 – X1 pin 2 and the negative
lead to body earth.
2. Switch the ignition to ACC or ON position, and the
wiper and washer control switch to high speed
position.
Is the reading on the multimeter battery voltage?
Go to Step 8. There is a fault in circuit
92. Diagnose the circuit.
Repair or replace circuit
92.
8. 1. W ith a multimeter, probe with the positive lead to the
harness connector M17 – X1 pin 1 and the negative
lead to body earth.
2. Switch the ignition to ACC or ON position, and the
wiper and washer control switch to INT position.
Is the reading on the multimeter battery voltage?
Go to Step 9.
There is a fault in circuit
96. Diagnose the circuit.
Repair or replace circuit
96.
9. 1. Disconnect the body control module harness
connector A15 – X1.
2. With a multimeter, check for continuity between the
harness connector M17 – X1 pin 5 and the harness
connector A15 – X1 pin 1.
Is there continuity?
System serviceable.
For further diagnosis,
refer to Section 12J,
BODY CONTROL
MODULE.
There is a fault in circuit
196. Diagnose the
circuit. Repair or
replace circuit 196.
When all diagnosis and repair are completed, check the system for correct operation.